Animation of one cycle of the plant cutting machine.
This project is a result of my Electromechanical Systems as a precursor to next semester's real Senior Design project. As a team we were given specific customer requirements to meet regarding a tobacco plant harvesting machine for the use of producing vaccines. The machine was to have an input of 10 plant trays at a time that held 200 plants each at a 5cm pitch. These 10 trays were to be held in an input and output cart, inbetween which the trays would be flipped upside down and the plants would be cut off into a bin. We had to break down the requirements further by asking the "customer" questions, then we did a functional decomposition to understand what tasks the machine had to be responsible for. Our team then came up with possible solutions for these separate functions using a morphological chart, and we chose appropriate designs using a Pugh chart system. The next step was to work backwards from our time requirements of each machine step to determine the appropriate acceleration profile to size the motors. We ended up using dc motors for the horizontal and vertical motion of the mover platform, and rotary and linear pneumatics for the flipping and cutting motions. Next we designed the machine in and rendered it at important steps throughout the process, as is illustrated below. After assembling the machine in Solidworks using a wide range of off the shelf components and custom pieces, we came up with a Bill of Materials and did a pro forma analysis to judge the financial feasibility of this project. By replacing one worker at $16, our machine was 17 times more efficient and with an initial cost of about $150,000, over a 5 year life span the net present value of this machine came to about $2 million.
Let's start by having a look at the process that went into designing the machine with some of our scratchwork and drawings.

A first design concept of the mover platform.

Our timing workflow which then guided us to choose an appropriate acceleration profile.

Calculations for the flipping mechanism. At first we were strongly considering making the flipping unit powered by a dc motor and gear reductions.

Some thought out concepts of how the flipping mechanism might interface with the cutting table.

An more in depth explanation for how much force the flipping mechanism will be responsible for and how we will achieve this using two pneumatic rotary actuators.

Explaining how the pancake air cylinders will hold the weight of the tray when flipping, and how the powerful blade will chop the plants off the tray.

A final concept of what the flipping unit and cutting bed with cutting mechanism will look like.
_____________________________________________________________________________________
Below we have an in depth look at one cycle of our plant cutting machine. The plant tray that will be used in this step by step explanation is depicted by the ironman like color scheme for clarity:

At 0 seconds the mover platform is at its home position, ready to begin a new cart of trays.

At 6 seconds the mover platform positions itself under the tray and lifts up until the pins in the platform interface with the corresponding holes in the plant tray.
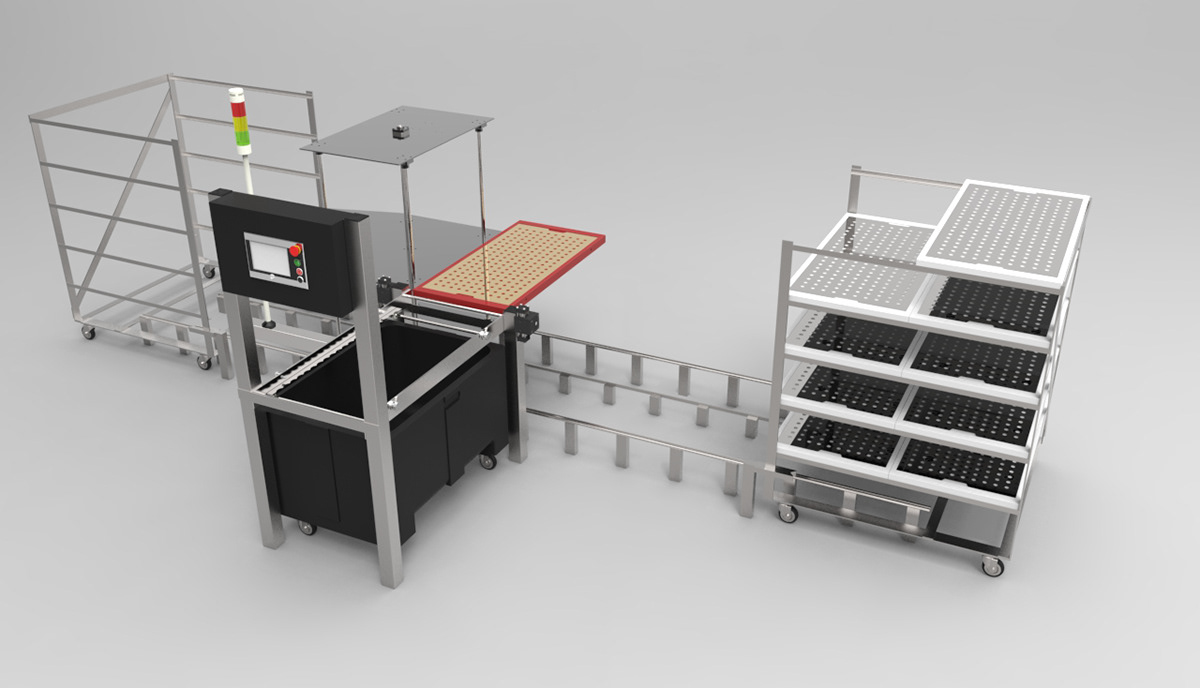
At 12 seconds the mover platform goes back to its home position with the tray ready to be picked up and flipped over.

At 13 seconds the flipper arms move to surround the plant tray.

At 14 seconds the flipper arms fully surround the plant tray and the 4 pneumatic pins are inserted into the plant tray.

A close up view of one of the 4 pneumatic pins responsible for securing the plant tray to the flipper arms.

At 17 seconds two high torque pneumatic rotary actuators flip the tray over into the cutting bed.

The bottom view of the plant tray on the cutting bed about to be cut at 17 seconds.

The plant cutting blade at 17.5 seconds mid way through shearing the tray plants off into the bucket.

The pneumatically actuated plant cutting blade at the end of its stroke at 18 seconds.

The tray in the cutting bed with the plants removed at 18 seconds ready to be flipped back onto the mover platform which has maneuvered itself during the cutting operation.
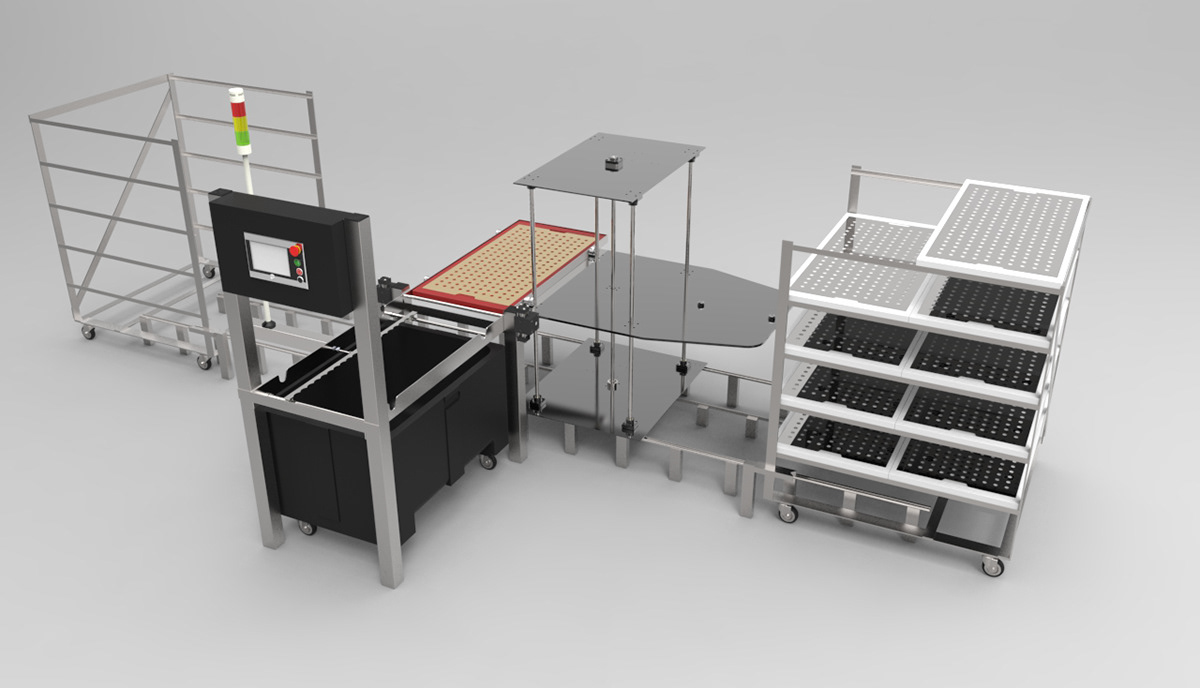
At 21 seconds the tray is flipped back onto the mover platform using the 180 degree rotary pneumatic actuators in reverse.

At 23 seconds the arms move back into the cutting table allowing the mover platform to put the tray into the empty cart.

At 29 seconds the mover platform places the empty tray into the empty cart.

At 35 seconds the mover platform is back to its home position ready to start a new cycle.