
The award winning Arion is a revolutionary clothes ironing system developed to suit the lifestyles of students and young professionals. It harnesses the power of hot air, pressure and moisture to effortlessly remove creases from clothing in a fast, safe and effective manner. The system has also the unique ability to dry and iron clothing straight from the washing machine in one automated process

The Arion in the process of ironing a pair of pants directly from the washing machine.
It can iron a pair of pants from wet in 15 minutes
It can iron a pair of pants from wet in 15 minutes

The airbag is produced from a porous membrane. When inflated the airbag expands applying an even pressure across the entire inner surface of the garment. this gentle pressure straightens out the creases and removes wrinkles from within. hot air is simultaneously forced through the clothing fibers to speed up the process
The Arion can iron a T-shirt in 3 minutes start to finish and by inflating to fill the exact shape of the garment, one airbag can accomadate all sizes.
The Arion can iron a T-shirt in 3 minutes start to finish and by inflating to fill the exact shape of the garment, one airbag can accomadate all sizes.
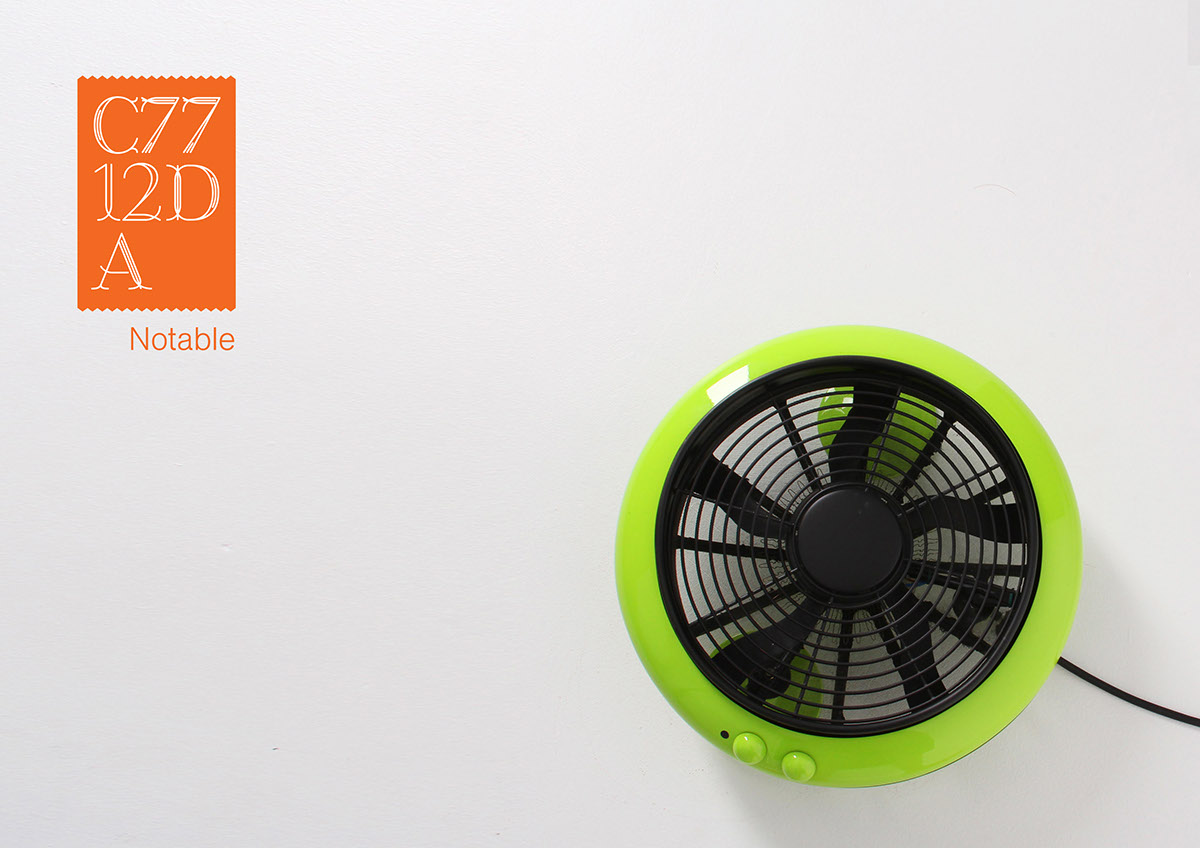
The Arion is a multifunctional design that doubles as a space heater/cooling fan
Design Brief
Vision
To create a revolution in the way we iron clothing. I will aim to transform ironing it into a positive, pleasurable experience. When the user walks away from an interaction with this product they should be smiling.
Background
The initial idea came from observing the student trick of using a hair dryer to remove creases from clothing. There are a lot of benefits to using this method so I decided to explore the idea of creating a purpose built product for the task.
Market
Through research I have found that students and young professionals tended to avoid marathon ironing sessions in favour of the just in time approach to ironing. So it was vital to take into account this preferred approach to ironing when developing the Arion.
Vision
To create a revolution in the way we iron clothing. I will aim to transform ironing it into a positive, pleasurable experience. When the user walks away from an interaction with this product they should be smiling.
Background
The initial idea came from observing the student trick of using a hair dryer to remove creases from clothing. There are a lot of benefits to using this method so I decided to explore the idea of creating a purpose built product for the task.
Market
Through research I have found that students and young professionals tended to avoid marathon ironing sessions in favour of the just in time approach to ironing. So it was vital to take into account this preferred approach to ironing when developing the Arion.
Product Development
There are three basic elements required to effectively remove creases from clothing. Pressure, Heat and Moisture.
There are three basic elements required to effectively remove creases from clothing. Pressure, Heat and Moisture.

Pressure
I realised early on that the pressure could be achieved trough inflating an airbag using a relatively high volume fan. After a lot of testing I found that domestic fans were not up to the task. They were not able to produce the pressure needed to inflate wet clothing. So I mocked up a basic prototype which consisted of a car cooling fan and a pillow case. By doing this I could prove the basic concept very early on. I introduced heat by pointing a hair dryer into the inlet under the fan. Early results were very promising. This gave me the confidence to set out the hard points of the design. After a lot of sourcing finally decided on using a car fan for the actual design. It had what I needed. It could push a high volume of air, it could be quiet, and it was an existing off the shelf component which would have all the inherent advantages that go with.
I realised early on that the pressure could be achieved trough inflating an airbag using a relatively high volume fan. After a lot of testing I found that domestic fans were not up to the task. They were not able to produce the pressure needed to inflate wet clothing. So I mocked up a basic prototype which consisted of a car cooling fan and a pillow case. By doing this I could prove the basic concept very early on. I introduced heat by pointing a hair dryer into the inlet under the fan. Early results were very promising. This gave me the confidence to set out the hard points of the design. After a lot of sourcing finally decided on using a car fan for the actual design. It had what I needed. It could push a high volume of air, it could be quiet, and it was an existing off the shelf component which would have all the inherent advantages that go with.

Second Stage Prototype performing a more in-depth analysis of the systems function using external heat source

Fan Blade Design
I found that sloping blade fans produced less noise than straight blade fans albeit at a reduction in air pressure. I decided to trade off air pressure for noise reduction to maintain a quality user experience. Add to that the sound deadening effects of the airbag and we were left with a very satisfactory 25dB output at 1 meter.
Straight blade Car Fan 38dB
Curved Blade Car Fan 30dB
Hair Dryer 60-95dB
I found that sloping blade fans produced less noise than straight blade fans albeit at a reduction in air pressure. I decided to trade off air pressure for noise reduction to maintain a quality user experience. Add to that the sound deadening effects of the airbag and we were left with a very satisfactory 25dB output at 1 meter.
Straight blade Car Fan 38dB
Curved Blade Car Fan 30dB
Hair Dryer 60-95dB

Tuning the air tunnel
During testing I found that the airbag was not inflating adequately. Increasing the power did not solve the issue. I found the problem was the low pressure area directly above the centre of the fan blade was creating a partial vacuum which drew fast moving high pressure air in from the sides creating a vortex. This caused the airbag to lose shape.
I solved this issue and reduced the turbulence by narrowing the tunnel walls on the upper side of the fan just enough to force the fast flowing air towards the centre of the air tunnel. This had the effect of dragging the turbulent air up through the system which helped to keep a constant stream of air flowing. This required a lot of tuning of the tunnel shape to get the balance right. Too sharp a narrowing of the tunnel created a vortex in itself, too slight a narrowing and the high pressure air would not neutralise the turbulent air in the centre of the tunnel. By narrowing the exit of the air tunnel, the top lip would also be the right size to accommodate the airbag and still maintain a pleasing aesthetic.
During testing I found that the airbag was not inflating adequately. Increasing the power did not solve the issue. I found the problem was the low pressure area directly above the centre of the fan blade was creating a partial vacuum which drew fast moving high pressure air in from the sides creating a vortex. This caused the airbag to lose shape.
I solved this issue and reduced the turbulence by narrowing the tunnel walls on the upper side of the fan just enough to force the fast flowing air towards the centre of the air tunnel. This had the effect of dragging the turbulent air up through the system which helped to keep a constant stream of air flowing. This required a lot of tuning of the tunnel shape to get the balance right. Too sharp a narrowing of the tunnel created a vortex in itself, too slight a narrowing and the high pressure air would not neutralise the turbulent air in the centre of the tunnel. By narrowing the exit of the air tunnel, the top lip would also be the right size to accommodate the airbag and still maintain a pleasing aesthetic.

Heating Element
I sourced the heating element from an off the shelf domestic fan heater to keep development and manufacturing costs down. By positioning the heating element in the obvious location above the fan while maintaining a safe distance from the garment above, the overall height of the unit would need to be raised by 100mm. In doing so I would be compromising the proportions of the design. To get around this I took the unorthodox approach and positioned the heating element below the fan and around the motor. By taking this approach I was able to add the heating element without having to increase the height at all because by positioning it around the motor I was utilising dead space. The reduction in efficiency by having to push hot instead of cold air through the fan blades was a justifiable trade off. Through prior testing I had achieved a surplus in air pressure within the airbag. By trading off a small amount of this surplus air pressure I was able to maintain the desired look of the unit.
I sourced the heating element from an off the shelf domestic fan heater to keep development and manufacturing costs down. By positioning the heating element in the obvious location above the fan while maintaining a safe distance from the garment above, the overall height of the unit would need to be raised by 100mm. In doing so I would be compromising the proportions of the design. To get around this I took the unorthodox approach and positioned the heating element below the fan and around the motor. By taking this approach I was able to add the heating element without having to increase the height at all because by positioning it around the motor I was utilising dead space. The reduction in efficiency by having to push hot instead of cold air through the fan blades was a justifiable trade off. Through prior testing I had achieved a surplus in air pressure within the airbag. By trading off a small amount of this surplus air pressure I was able to maintain the desired look of the unit.
Applying Moisture
I needed a way to apply moisture to the clothing to increase the efficiency. I wanted to avoid using a steam generator for several reasons. I did not feel it was critical to the function of the product; it added cost and most importantly it added complexity to the design, something I was determined to avoid where possible. The solution was simple and effective; a squeeze water bottle. It was the ideal solution, cheap and easy to use but more important, it allowed the user to interact with the product. The user could apply more water on the hard to iron areas of the clothing giving them a heightened sense of control over the process.
Collapsible Airbag Vs Solid Manikin
Early on in the development process, I decided for various reasons that it was important that the manikin for holding the garment was produced from a flexible material and not a rigid structure. A rigid structure would not easily accommodate different garment sizes and would not be able to apply the pressure needed to aid the ironing process. By making the manikin out of a flexible material it could be inflated to fit all size garments using one size airbag. Another major advantage was that the flexible material could be collapsed for easy storage. This was a very important feature for the intended market who predominantly lived in small urban dwellings with limited space. On top of that it also opened the possibility for designing a multifunction product that could double as a space heater eliminating the requirement for storage while not in use. This really appealed to me as I intended this to be a desirable product that people would want to own and display.
To avoid the complexity of trying to design an airbag to accommodate both pants and shirts/T-shirts. I decided it with be simpler and more effective to use separate interchangeable airbags one for pants and one for shirts/T-shirts to be expanded upon if needed to include fun inflatable shaped for other uses.
Initial testing using cotton for the air bag proved unsatisfactory. The lack of elasticity coupled with the high moisture retention meant that it was less than ideal for its intended purpose. I final settled on a Nylon/Elastane weave similar to that used in surfing rash guards. It had all the required properties; elastic, breathable, durable and crease resistant.
I needed a way to apply moisture to the clothing to increase the efficiency. I wanted to avoid using a steam generator for several reasons. I did not feel it was critical to the function of the product; it added cost and most importantly it added complexity to the design, something I was determined to avoid where possible. The solution was simple and effective; a squeeze water bottle. It was the ideal solution, cheap and easy to use but more important, it allowed the user to interact with the product. The user could apply more water on the hard to iron areas of the clothing giving them a heightened sense of control over the process.
Collapsible Airbag Vs Solid Manikin
Early on in the development process, I decided for various reasons that it was important that the manikin for holding the garment was produced from a flexible material and not a rigid structure. A rigid structure would not easily accommodate different garment sizes and would not be able to apply the pressure needed to aid the ironing process. By making the manikin out of a flexible material it could be inflated to fit all size garments using one size airbag. Another major advantage was that the flexible material could be collapsed for easy storage. This was a very important feature for the intended market who predominantly lived in small urban dwellings with limited space. On top of that it also opened the possibility for designing a multifunction product that could double as a space heater eliminating the requirement for storage while not in use. This really appealed to me as I intended this to be a desirable product that people would want to own and display.
To avoid the complexity of trying to design an airbag to accommodate both pants and shirts/T-shirts. I decided it with be simpler and more effective to use separate interchangeable airbags one for pants and one for shirts/T-shirts to be expanded upon if needed to include fun inflatable shaped for other uses.
Initial testing using cotton for the air bag proved unsatisfactory. The lack of elasticity coupled with the high moisture retention meant that it was less than ideal for its intended purpose. I final settled on a Nylon/Elastane weave similar to that used in surfing rash guards. It had all the required properties; elastic, breathable, durable and crease resistant.

During testing of the “Pants Airbag” I encountered issues maintaining enough pressure to hold the shape of the upper legs as they tended to droop under the weight of the wet garment. To combat this in the interim I applied a spray on water resistant fabric sealant. This had the effect of partially restricting the rate of airflow through the garment allowing more rigid inflation. In production this would be easily achieved via a variable density weave. This would inevitably slow down the ironing process but I felt it was a necessary trade off that needed to be made to maintain the overall vision of the project.
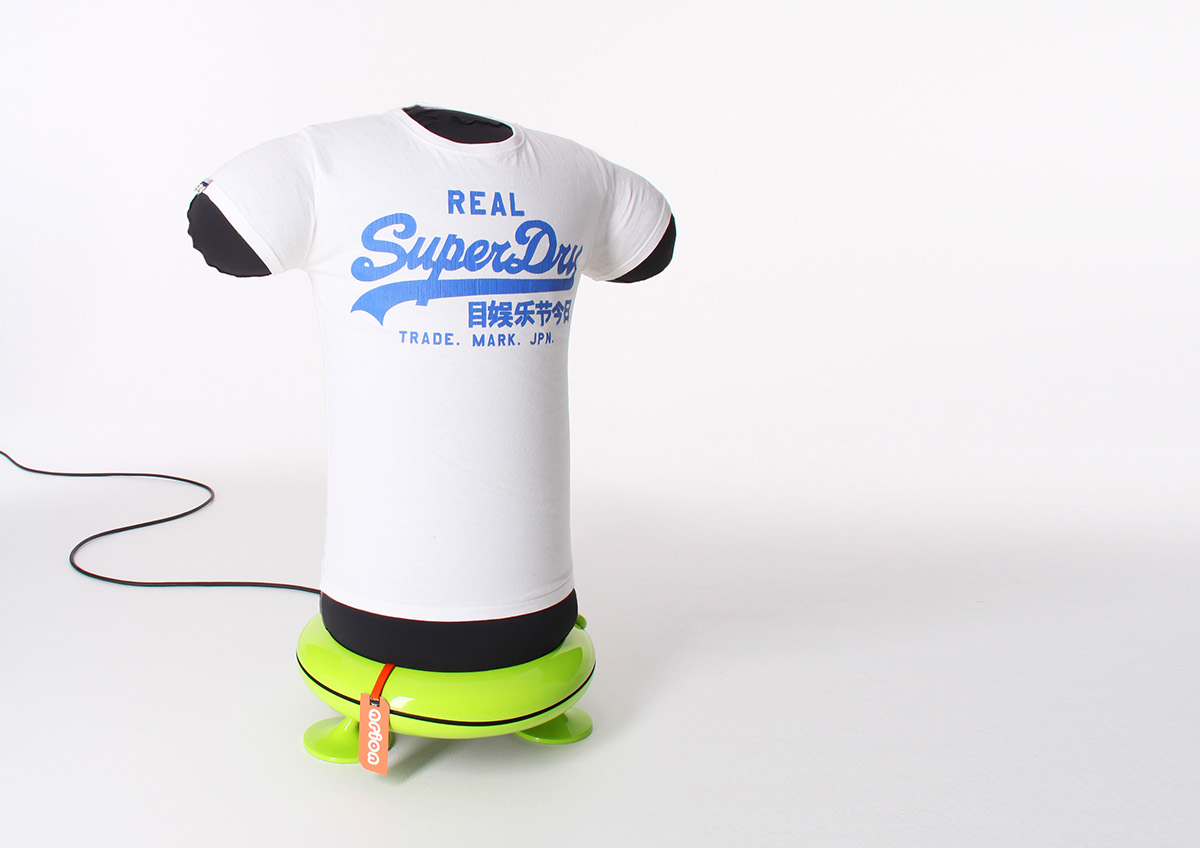
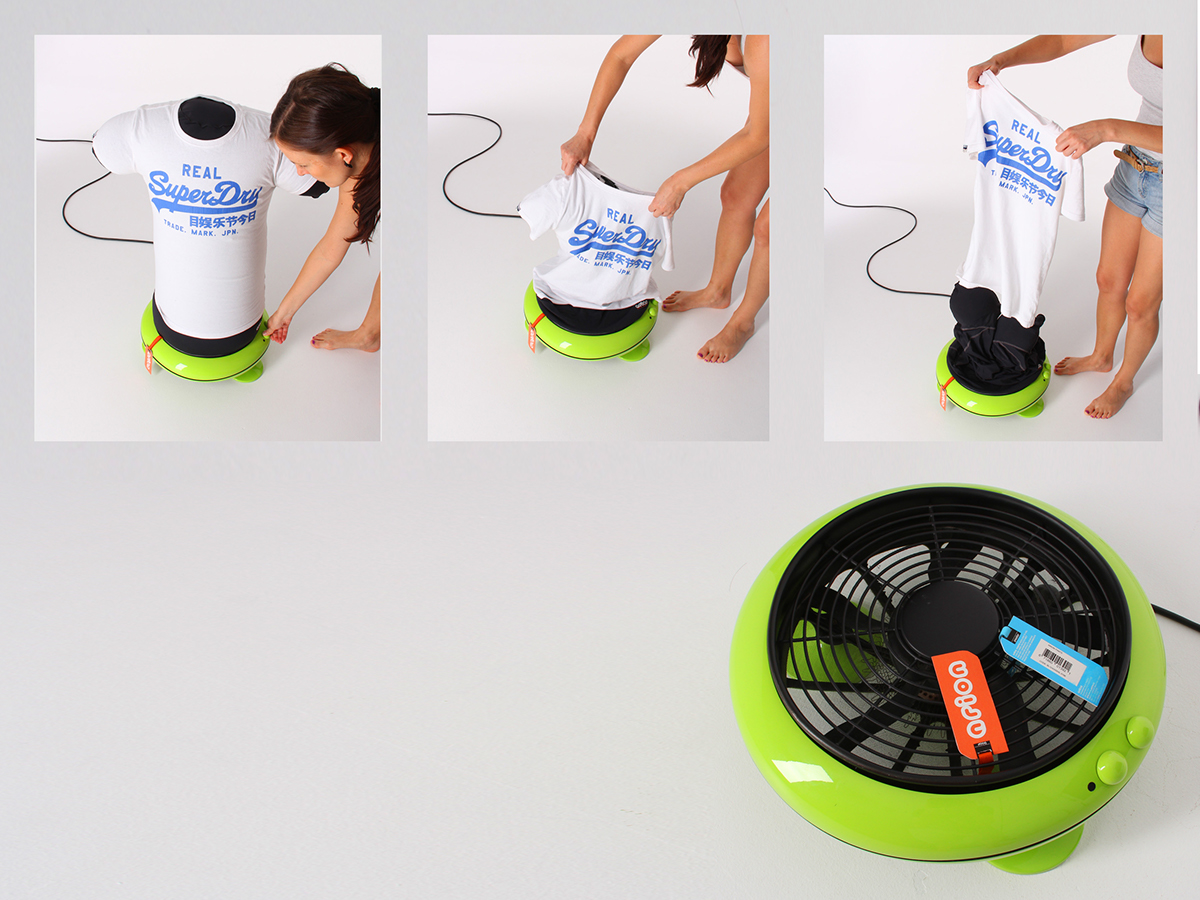
Removing T-shirt after ironing process is completed

The Arion can also be used to aerate sneakers