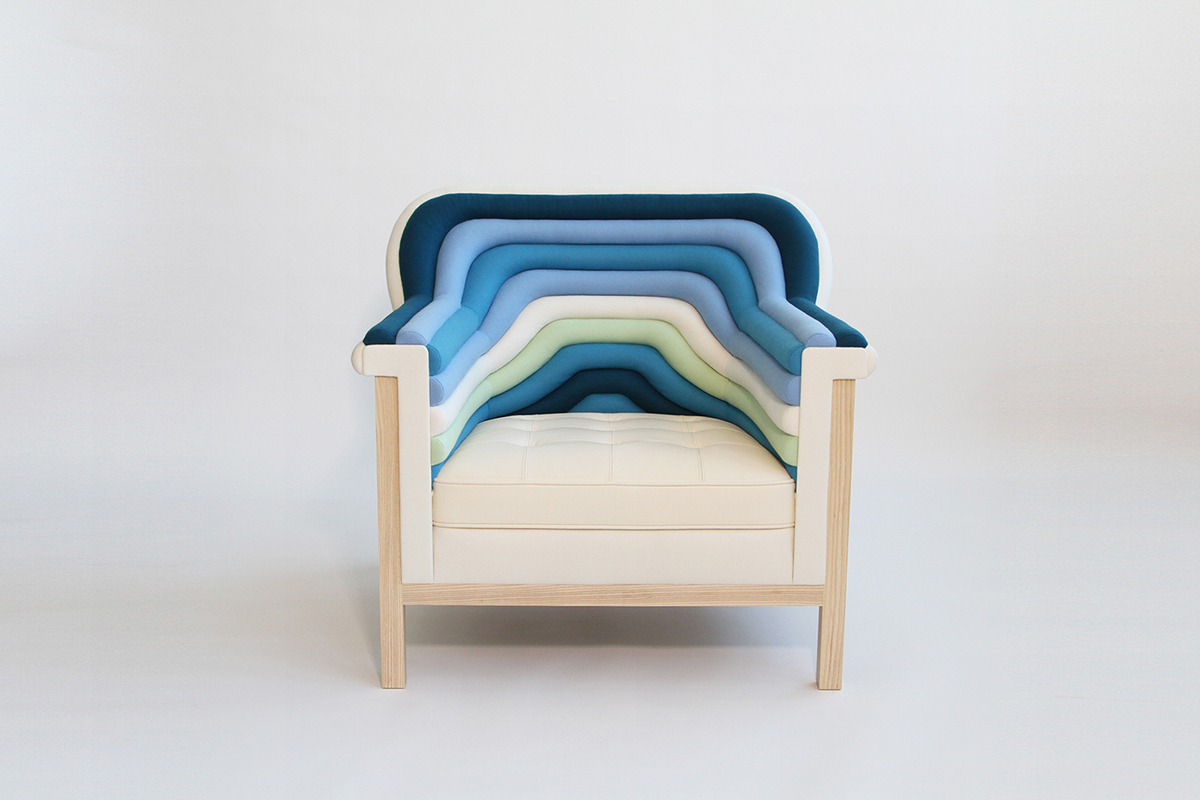
Journeyman Furniture
Cool - Chair
Reaching the end of my 3-year long studies at Linköping's University gave me an opportunity to summarize everything I had learned. This was by putting all my knowlegde into one final examination furniture called Journeyman Furniture.
With the Journeyman Furniture, I got an opportunity to make the whole production cycle of a furniture from the beginning to the end by myself. From designing, making the product drawings, carpeting to furniture upholstering. When designing the chair, a Mexican exchange student Kaleb Cardenas Zavala collaborated the designing phase as part of his studies with me.
In a Journeyman work the furniture is examined by the master furniture upholsterers three times. All the choices made, materials used, technical quality of the work, technical construction and furnitures functionality was evaluated and scored.
With the Journeyman Furniture, I got an opportunity to make the whole production cycle of a furniture from the beginning to the end by myself. From designing, making the product drawings, carpeting to furniture upholstering. When designing the chair, a Mexican exchange student Kaleb Cardenas Zavala collaborated the designing phase as part of his studies with me.
In a Journeyman work the furniture is examined by the master furniture upholsterers three times. All the choices made, materials used, technical quality of the work, technical construction and furnitures functionality was evaluated and scored.
As I created a new technique to the back and armrests, combining different wadding materials together, I chose to also combine my Journeyman work to my Bachelor's Examination work. In my Bachelor's Examination I studied more closely different materials used under/combined with the upholstery fabric. By using one material or combining different modern and traditional wadding materials together, you can get varieties of different qualities, looks and touches to your furniture surface.
What are the materials that will be the most durable over time?
Which one of the materials/combinations will give an even, beautiful and comfortable surface?
Are they washable? Can you succesfully use materials never used before as a wadding, such as horse hair? These were some of the questions I was looking answers for during my examination work.
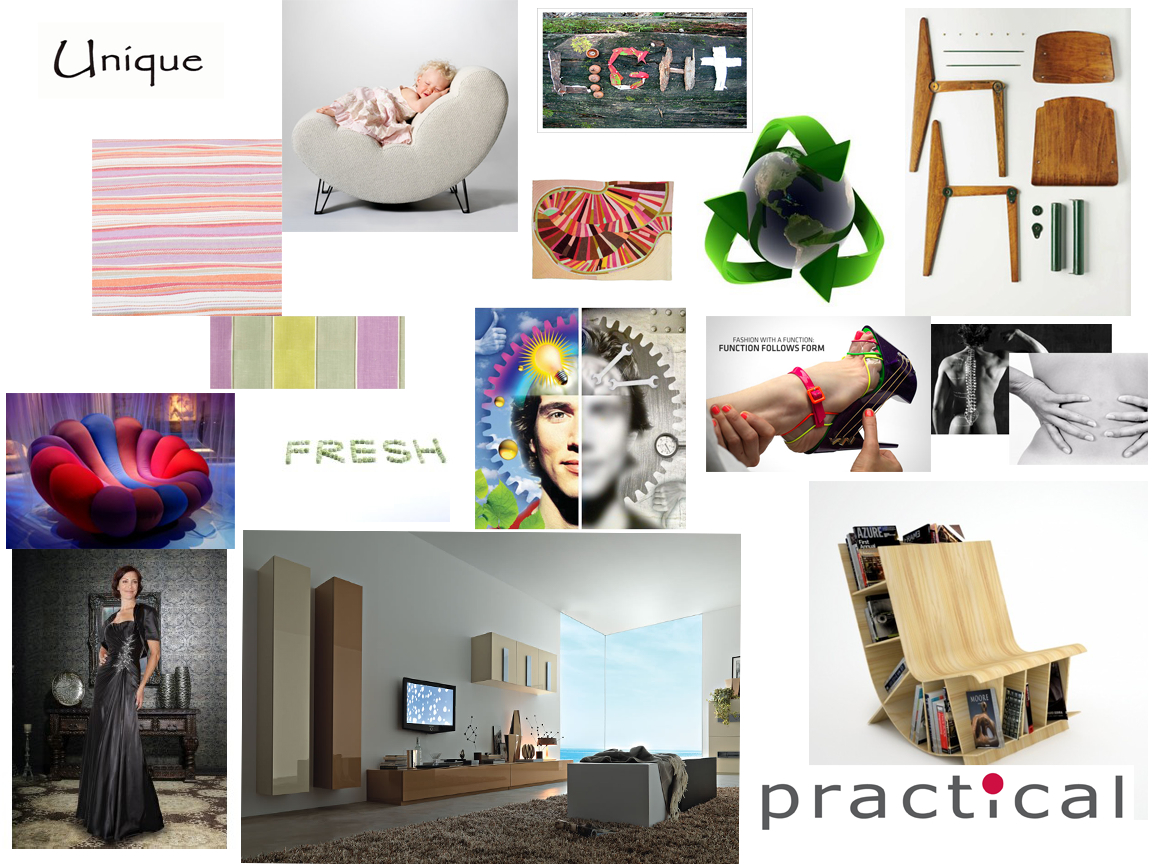
Mood board
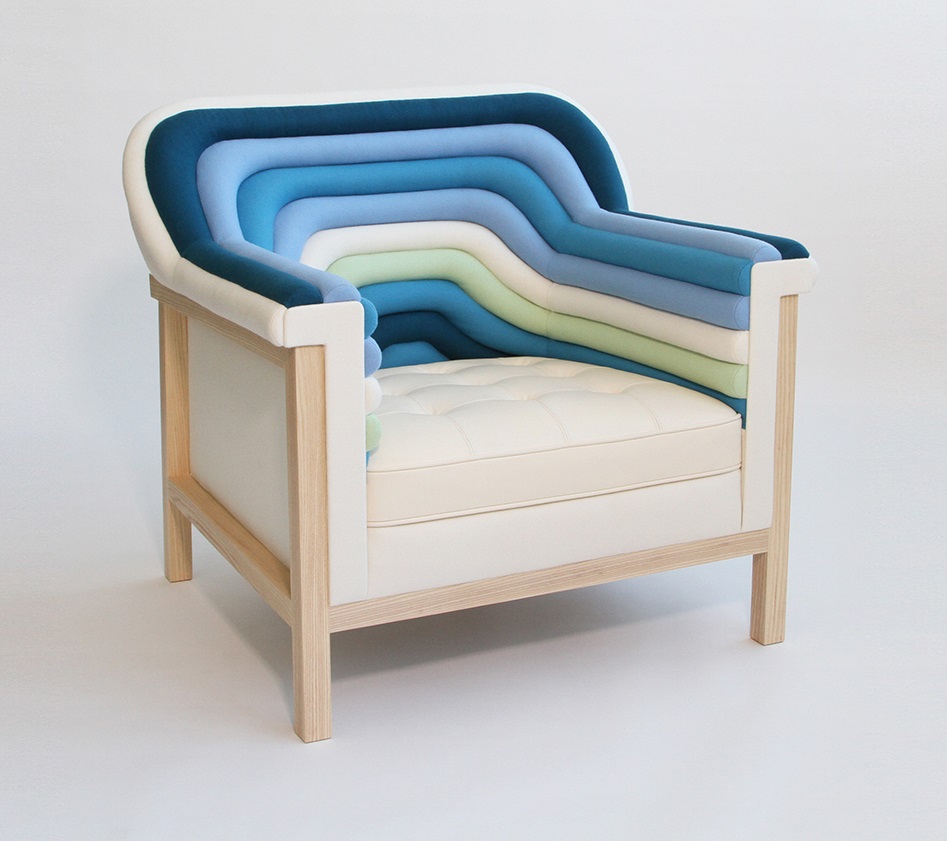
What is a Journeyman Furniture?
A Journeyman Furniture in furniture upholstery is build up with traditional techniques and materials, and is the most challenging work for the furniture upholsterer. In this examination work the specific high difficulty techniques listed by the examinators have to be included in order to receive the approval to proceed to the production phase. All the furniture upholstering work has to be planned and done by the furniture upholsterer herself, without receiving any help.
The permission to start the journeyman work is requested minimum of two months ahead from the STC (Swedish Master Furniture Upholsterers Central Union). This is to give the examinators time to go thru the application with detailed product drawings and a workplan with detailed timeplanning. The highest possible score, five points, can be received only by adding the most difficult techniques with the highest quality of work. Doing furniture upholstery on a Journeyman Furniture at this advanced level will take approximately between 300 - 700 working hours, depending on the furniture and the methods used.
A Journeyman Furniture in furniture upholstery is build up with traditional techniques and materials, and is the most challenging work for the furniture upholsterer. In this examination work the specific high difficulty techniques listed by the examinators have to be included in order to receive the approval to proceed to the production phase. All the furniture upholstering work has to be planned and done by the furniture upholsterer herself, without receiving any help.
The permission to start the journeyman work is requested minimum of two months ahead from the STC (Swedish Master Furniture Upholsterers Central Union). This is to give the examinators time to go thru the application with detailed product drawings and a workplan with detailed timeplanning. The highest possible score, five points, can be received only by adding the most difficult techniques with the highest quality of work. Doing furniture upholstery on a Journeyman Furniture at this advanced level will take approximately between 300 - 700 working hours, depending on the furniture and the methods used.





The story of Cool-Chair
Even though using traditional techniques and materials, I wanted to create an innovative, fun and unique chair with a modern look. I also wanted it to be a fresh, light and at the same time invitingly comfortable easy chair.
Even though using traditional techniques and materials, I wanted to create an innovative, fun and unique chair with a modern look. I also wanted it to be a fresh, light and at the same time invitingly comfortable easy chair.
As I specially like to be creative with colours and colour combinations, I wanted to have the possibility to implement this aspect of myself in this project. I also wanted to make an ecofriendly, ergonomical and multifunctional chair.
I presented my ideas in overview on a moodboard. I Then delivered it to Kaleb Cardenas Zavala, who was visiting our school for three months as an exchange student from Mexico, where he is specializing in industrial design. Kaleb delivered me with four different sketches and helped me to formulate my wishes into expressing them as a consept. He also came up with the idea to use a traditional furniture upholstery material, horse hair as a wadding material, which I thought was a brilliant idea.
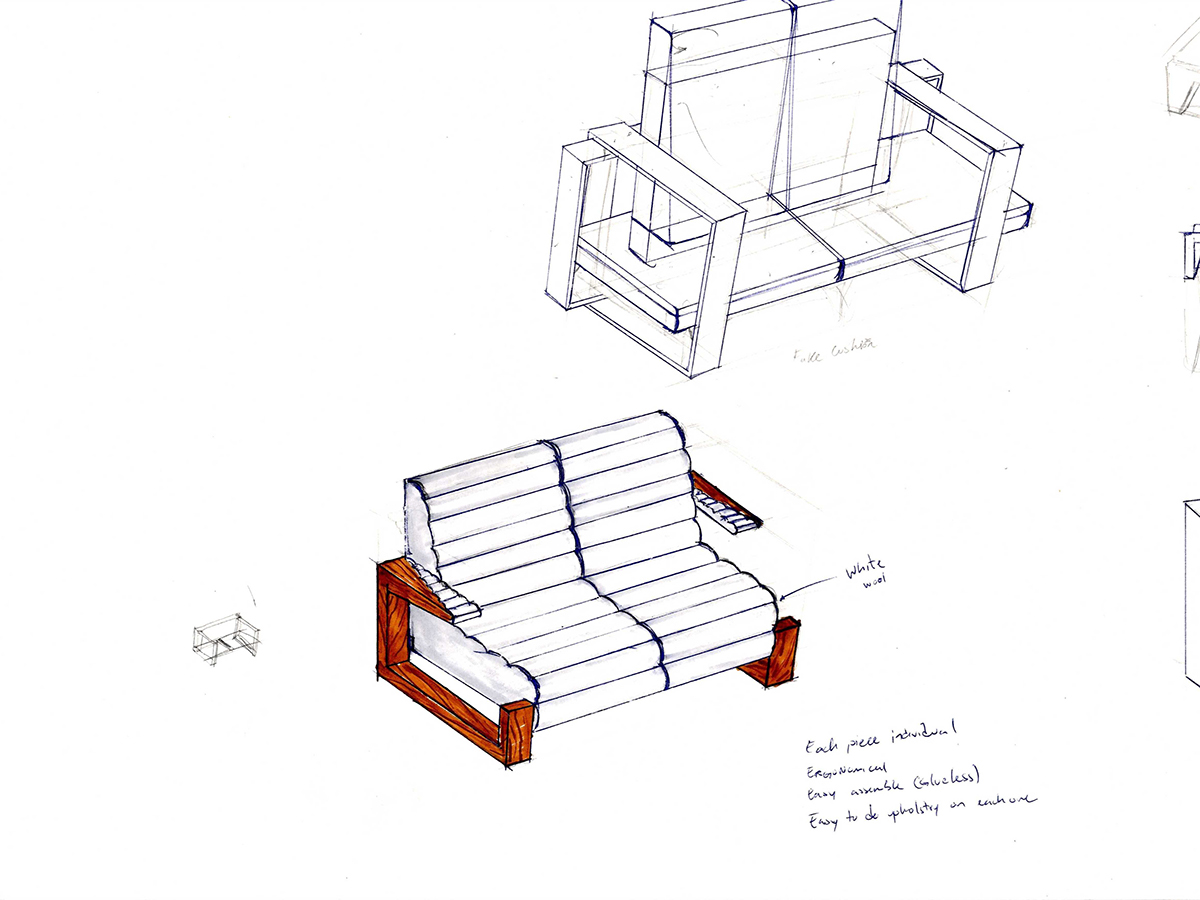
Kalebs sketches
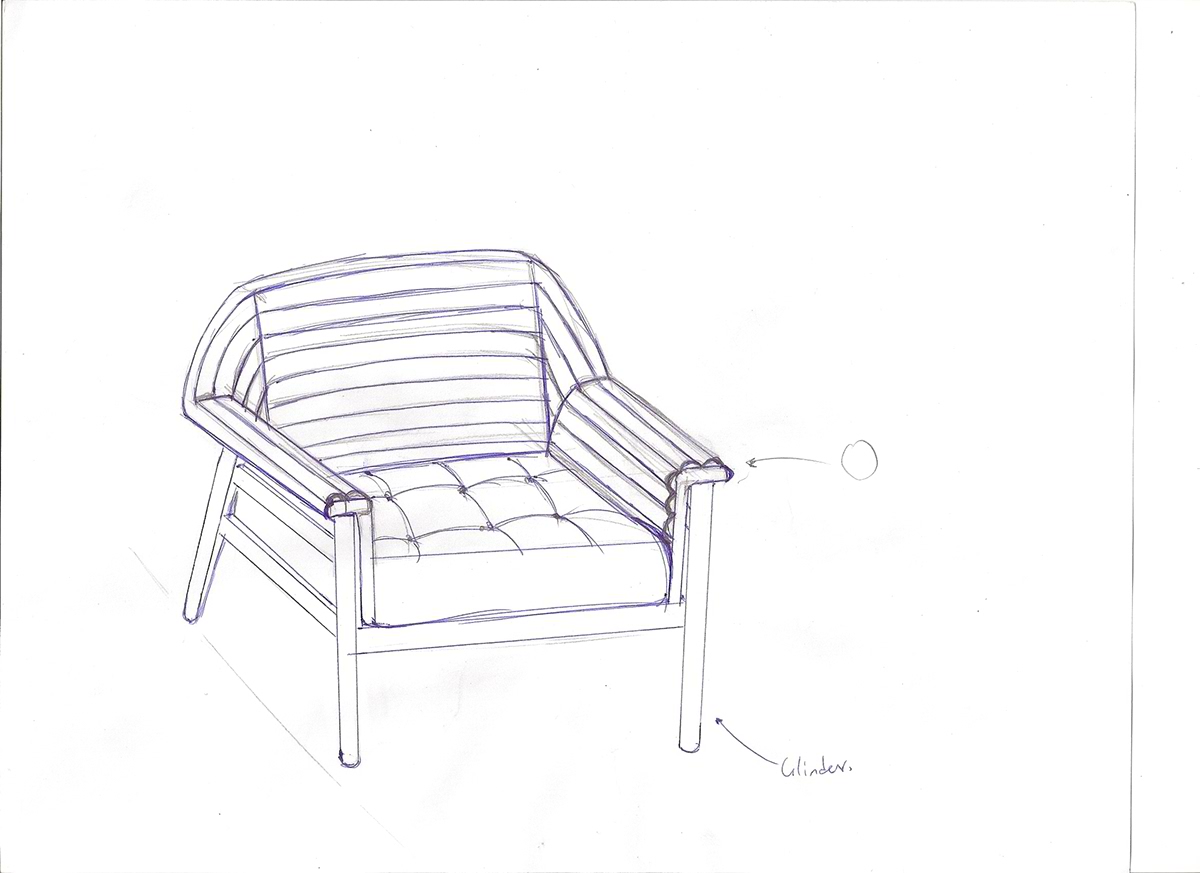
The sketch I chose to develop further.
I chose one of his sketches and started developing it further, adding new dimentions and applying new construction parts, such as a special seat called “a marked pillow”. The most difficult traditional seat construction technique in furniture upholstery, which I wanted to do. Adding the new dimentions and shaping the form was for better fitting the chair for the upcoming traditional furniture upholstery work. It was also for making the chairs shape ergonomical and for making it after my own preferences for the final look.
In this work phase I decided what elements and techniques I wanted to include required by the Swedish Master Furniture Upholsterers Central Union, and how I was going to manufacture them.
I wanted the wadding have higher and wider stripes to add more material as at the same time adding more comfort. The final measurements and construction of each part I decided when drawing the chairs production drawings in solidworks, a 3-D software. After I had decided the measurements, shape and construction, Kaleb made an approximate render of the chairs final look. This was to give a better idea of the chairs shape for the examinators.

Here I test with plasticine how the wadding/piping for back and armrests will work with the model.

To decide the form and angles where the armrests meets the backrest, I make small plasticine models. This is to have a better idea of the desirable result and also giving guidelines when drawing it.
When building up the frameconstruction, a cabinetmaking student at my school, Erik Pettersson built up the most difficult part between the armrest and the backrest. He assisted me in choosing some of the fastening methods and also helped me when gluing the parts together.
Martin Altwegg, a cabinetmaking teacher at my school helped me by making the fastening method and gluing the outerframe pieces together.
Martin Altwegg, a cabinetmaking teacher at my school helped me by making the fastening method and gluing the outerframe pieces together.
Erik gluing the seat frame pieces together with me.
A corner of the armrest done with the traditional furniture upholstery technique.
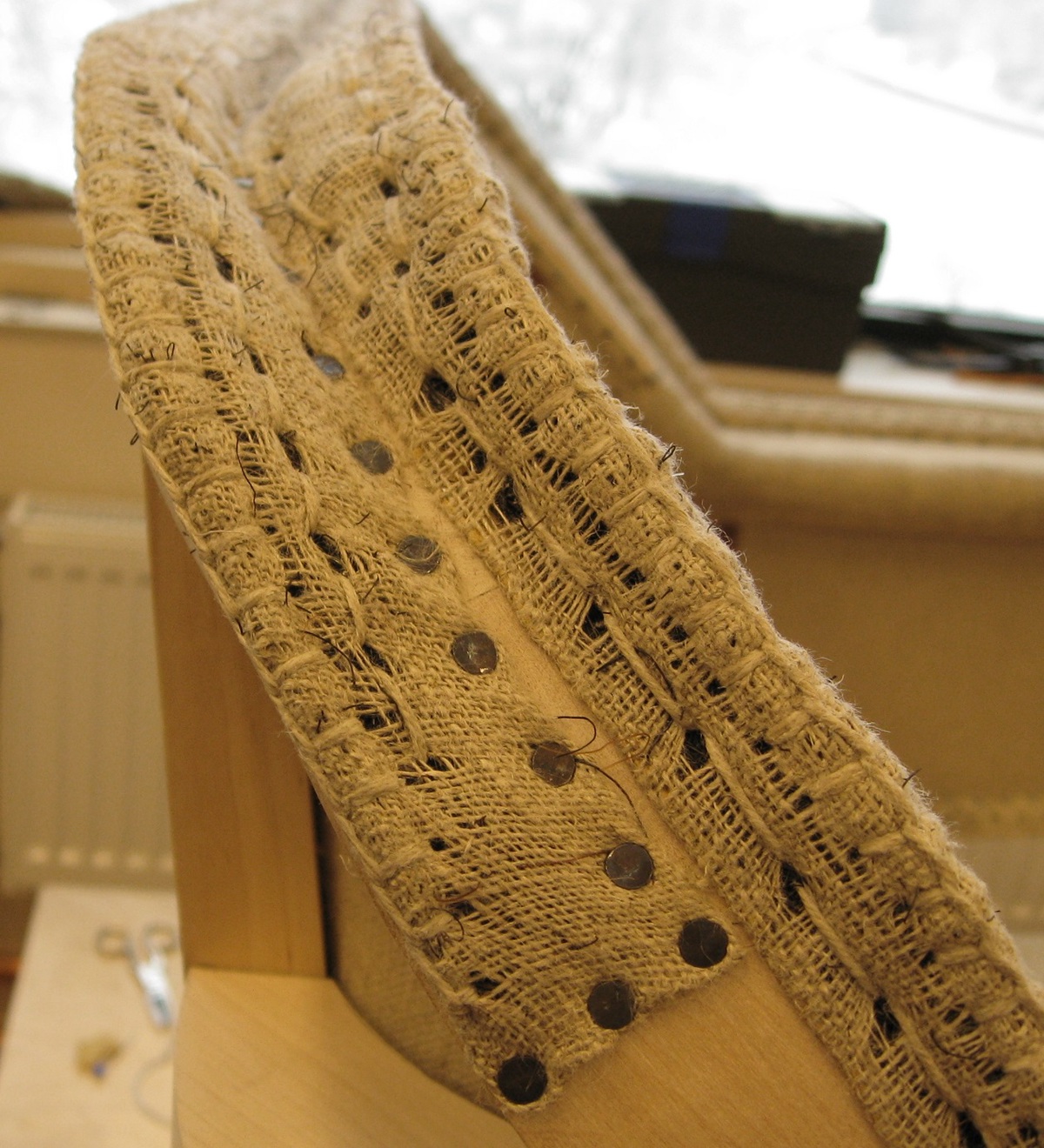
The backrest done with the traditional furniture upholstery technique.
For the back- and armrests of the chair I started developing further the idea of horse hair as a wadding material. This ended up with doing a bigger study over both traditional and modern materials with 16 different tests. I chose to apply the technique that, in my opinion, gave an even beautiful surface and is also very comfortable.This was a combination with several different materials, including horse hair.

I made 16 tests with different materials and material combinations to decide how to build up the piping method with a best possible result.
I developed a detachable cover of the back- and armrest piping method, that can be removed later on,
if desired. The chair can also be used without this detachable cover and will then have a plain surface.
The cover can also be made in different patterns and naturally with different colours, which makes this chair
a diverse furniture that can have multible different looks.
For the colour combination on the back- and armrests I used natures themes as an inspiration.
I tested on several different combinations together, and of these themes “ocean” was the one I chose to use.
The woven wool fabric from Kvadrat is called Divina3 and it is 100% new wool. I chose this fabric because
of it's naturally good qualities, such as long durability, dirt resistance, fire safeness and ecofriendliness. Divina3 has not been treated chemically in order to improve it's properties.
On the seat I chose to use leather from Tärnsjö Garveri. A leather tanning factory in Sweden known for their high quality leather produced with vegetable tanning.
On the seat I chose to use leather from Tärnsjö Garveri. A leather tanning factory in Sweden known for their high quality leather produced with vegetable tanning.

Using nature as an inspiration I test different colour combinations of Divina3 together.
Owner: Karoliina Priha
Design: Karoliina Priha and Kaleb Cardenas Zavala
Drawings, frameconstruction, carpentry and furniture upholstery: Karoliina Priha