36 Doors were sold for a certain location. Problem; they didn't fit. None of our doors would have fitted. But the order was big enough to see if it was financially interesting to design a custom door for this situation.
The challenge was to design one door (to keep good profit margins) that would fit all four different building scenarios (including tolerances), take mandatory fire doors into account (that were not yet installed) and all in an acceptable time frame. Ultimately, from the moment Sales explained their problem to delivery took just under 20 weeks.
The challenge was to design one door (to keep good profit margins) that would fit all four different building scenarios (including tolerances), take mandatory fire doors into account (that were not yet installed) and all in an acceptable time frame. Ultimately, from the moment Sales explained their problem to delivery took just under 20 weeks.

I went to take a look on location to see exactly what the customer needed. The warehouse was still under construction. I had to do it with construction drawings (with remeasured deviations), work flow description and technical drawing of the fire doors that would also be placed.

1) Look if the project is profitable;
It turned out that many integrated (safety) functions of our doors were unnecessary. They basically needed a door that closed of the room visually. By making a price calculation it showed there was a large enough budget to develop custom parts and cover any (development) risks. Normally our doors are mounted against a construction, but here it was more logic to install the door between the steel construction. The concept became a pre-assembled "box", which would house basically the entire door.
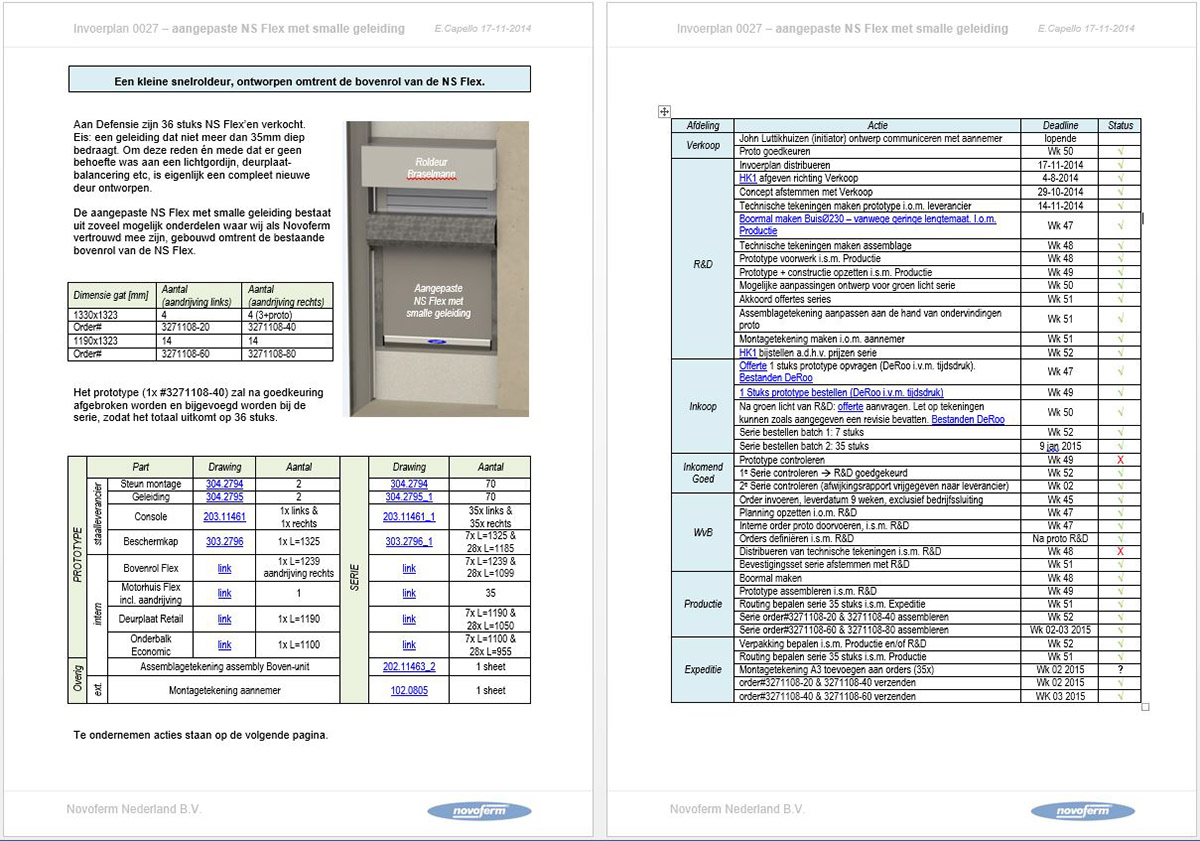
I compiled a brief plan to inform the project team, share relevant files and maintain the planning.

Because there was not much information to go on and different building scenarios, there was a certain risk things would not fit in the end. So before I would move forward spending money (by ordering parts) and spending man run time (by involving colleagues)
I drew all four scenarios and had the contractor approve it.

2) Look if the concept is realistic for our production;
I tried to use as much as existing parts to keep material costs down and stay with familiar processes so man-hour also did not add on to much. Eventually I only had to design four custom parts and adjust only four production drawings (shown here).
I tried to use as much as existing parts to keep material costs down and stay with familiar processes so man-hour also did not add on to much. Eventually I only had to design four custom parts and adjust only four production drawings (shown here).

Two of the four custom parts where needed to create a "box" that houses the top roller, door leaf and motor. By delivering it pre-assembled, it was easier to ship and quicker to install.

3) Design it so external mechanics are able to do the installation;
By delivering a pre-assembled design, in just eight simple steps the door (including wiring the control box) could be installed. This kept assembling simple and assembly time attractive.
By delivering a pre-assembled design, in just eight simple steps the door (including wiring the control box) could be installed. This kept assembling simple and assembly time attractive.
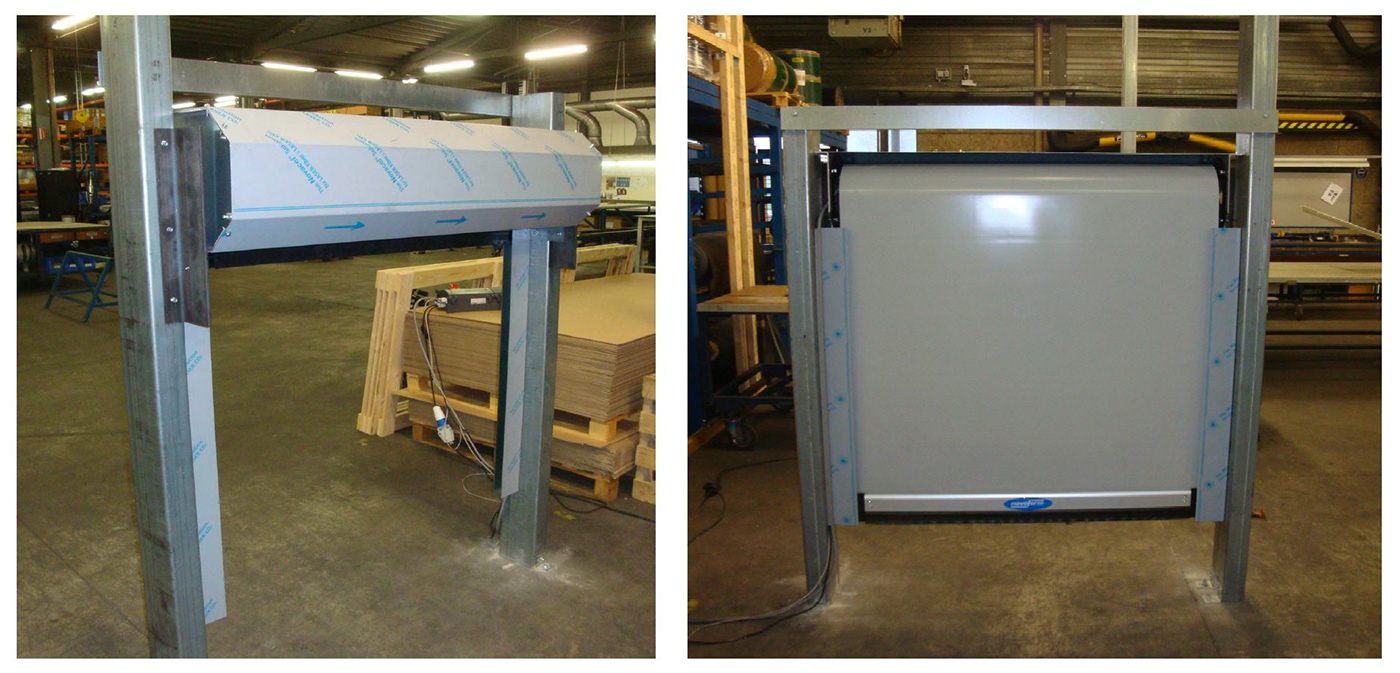
By building a steel frame I mimicked the situation to build the prototype against.

This project took place in the warehouse where (parts of) the Joint Strike Fighter was going to be assembled. For security reasons, it was unfortunately not possible to take pictures of the installed doors.