Production Module for Thermoforming Custom Tactile Sign Panels
A single operator can prep and thermoform up to 50 custom tactile sign panels per day. Below we outline the progression of product through the thermoforming production module. Examples of finished and semi-finished product are shown as well.
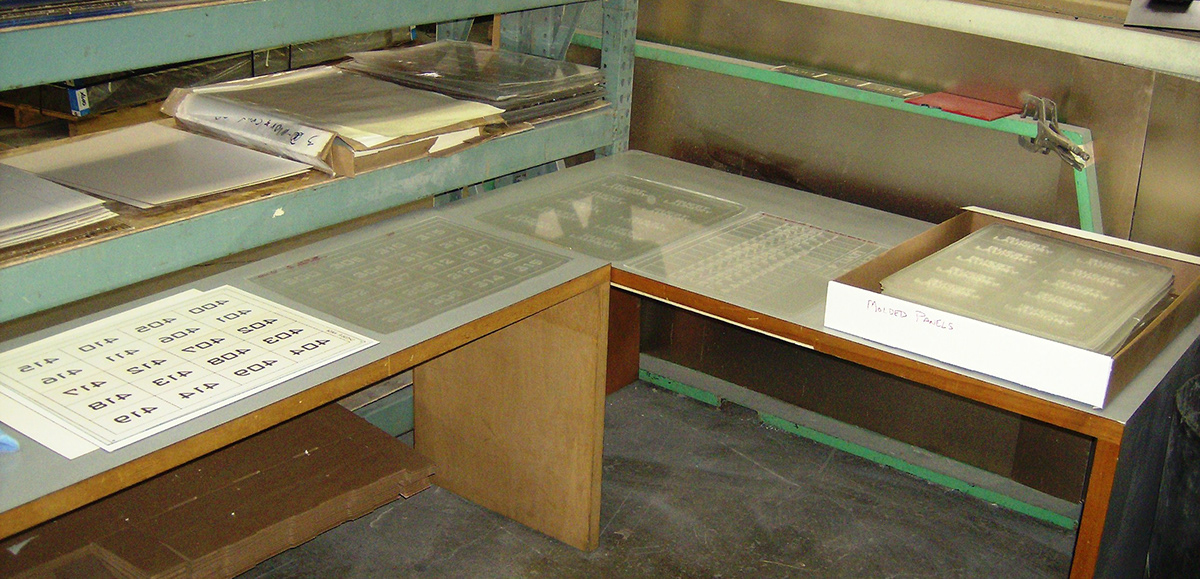
The operator used a Grimco Thermoforming Press (20"x26" format) to produce 40 panels of custom tactile signs. The operator cleaned and prepped 26 molds throughout the run (reusing molds for 14 additional panels). Production consisted of 42 peices of 1/8" Acrylite FF clear extruded acrylic (18"x24").
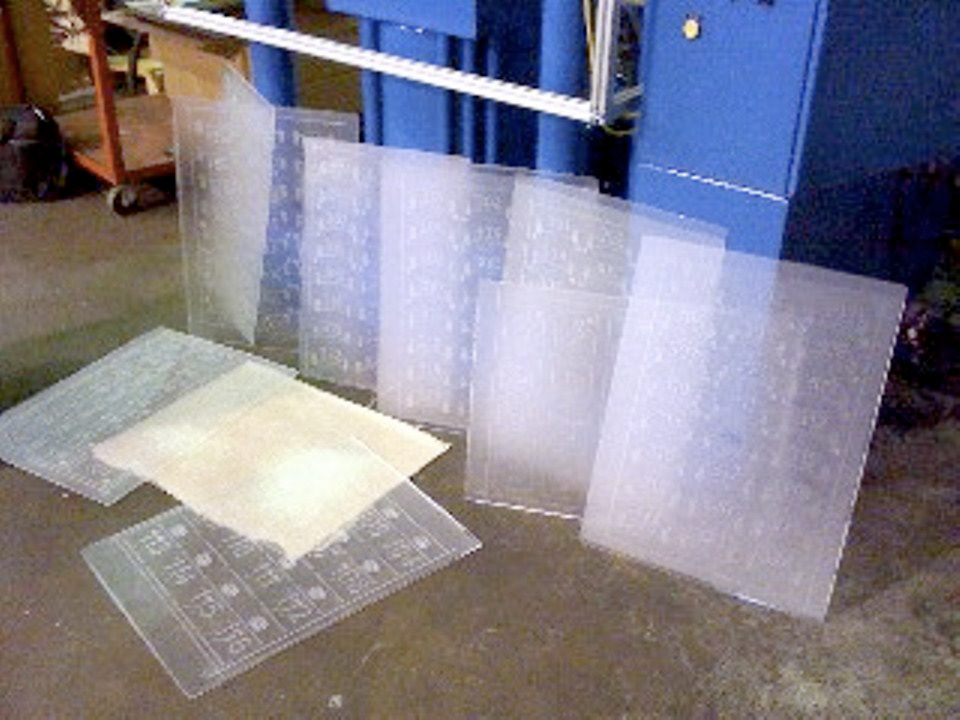
Total press time was 10:00 minutes per panel. While each panel was in the press, the operator cleaned molds and the acrylic to be formed. The operator was able to clean and prep all molds and acrylic in under two hours during panel production. The operator began the production run at 8:00am and pressed the final panel at 4:00pm.

Each panel was inspected after being formed. If panel was approved, it would be moved to the surface treatment phase. If a panel contained a major flaw, the acrylic would be flipped upside down and run again. No additional material was required. An example of a finished sign from this mold is shown below in this project.

To remove surface imperfections transfered from the mold (router marks), a flat sander was used. Each panel required from 1:00 to 2:00 minutes of sanding treatment using 120 grit sandpaper.

After sanding treatment, each panel was washed with a standard cleanser to remove shop dust and grease. It is ideal to use a degreasing agent such as "Simple Green" with a nylon scrub brush and power washer. Average wash time was approximately 1:00 minute per panel.

Each thermoformed and treated panel was placed on a router table for finish cutting. The individual signs were then cleaned for surface painting. Once painted, raised graphics were hot stamped with a contrasting color.

A finished tactile sign from the production photo above, this sign was thermoformed using a "slate stone" textured mold (Pionite). The 1/4" acrylic was back painted with black acrylic polyurethane paint with a blocked out section remaining clear. Raised graphics were hot stamped with black, white and red foils. The finished sign was mounted to a silver back plate using silver stand-offs. This sign was thermoformed and finished the same day.

An example of encapsulated photoluminescent sheet to produce emergency signs. A sheet of .040" photoluminescent was fused between a sheet of 1/8" Acrylite FF clear acrylic and 1/8" Acrylite FF white opaque acrylic. Graphics were hot stamped black. No clear coat required. When charged, this sign will glow for over 8 hours.

The process allows for using multiple thermoplastics such as ABS and PETG (shown above). PETG can be formed at lower temperatures and shear cut for easier finishing.

We encapsulated craft store leaves in this small panel of signs. Almost any material can be forever embedded into custom tactile signs without the use of adhesives, making the thermoforming process the most versatile method of tactile sign manufacturing on the market.

A 20" x 26" capacity thermoforming press by Grimco Hydraulics. The press is designed to manufacture a wide variety of tactile sign panels. Each press is custom built to client specifications. For more information, visit Grimco Hydraulics at www.grimcopresses.com