The following set of images document the design and bespoke making process for two large scale cast glass sculptures by Australian artist Peter Kovacsy.
This project started in April and was completed in August 2021
"TOGETHER" Cast glass sculptures
Material: Clear Blackwood Crystal, hand made in Australia
Size: Height 89cm to 97cm, Width 31cm to 35cm,
Depth 8cm to 10cm, Weight 42kg to 46kg
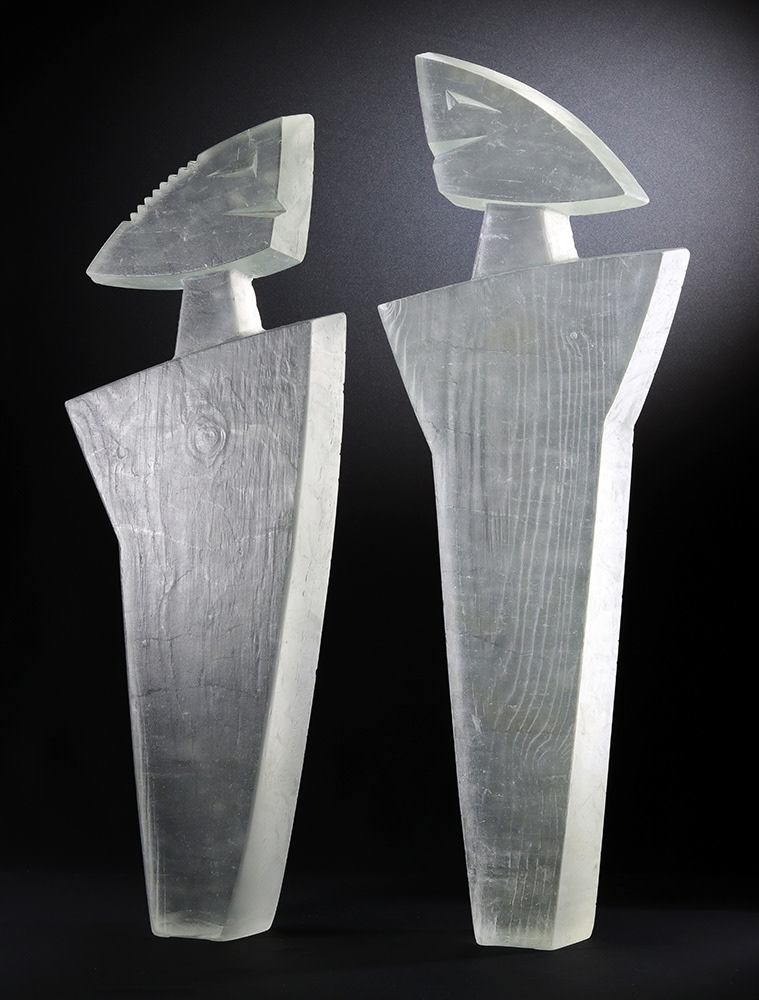
“The photo shoot” at the end of each project I get to play gaffer and photographer! Here’s what the lighting set looked like if you walked in the studio door on the day - 25/8/2021

The last stage in a commissioned project is when I get to sign and date the completed work, today was that day - 25th August 2021

The last step in the making process of these semi-abstract cast glass figurate forms is to cut and hone flat the
rear surface on the lead crystal.

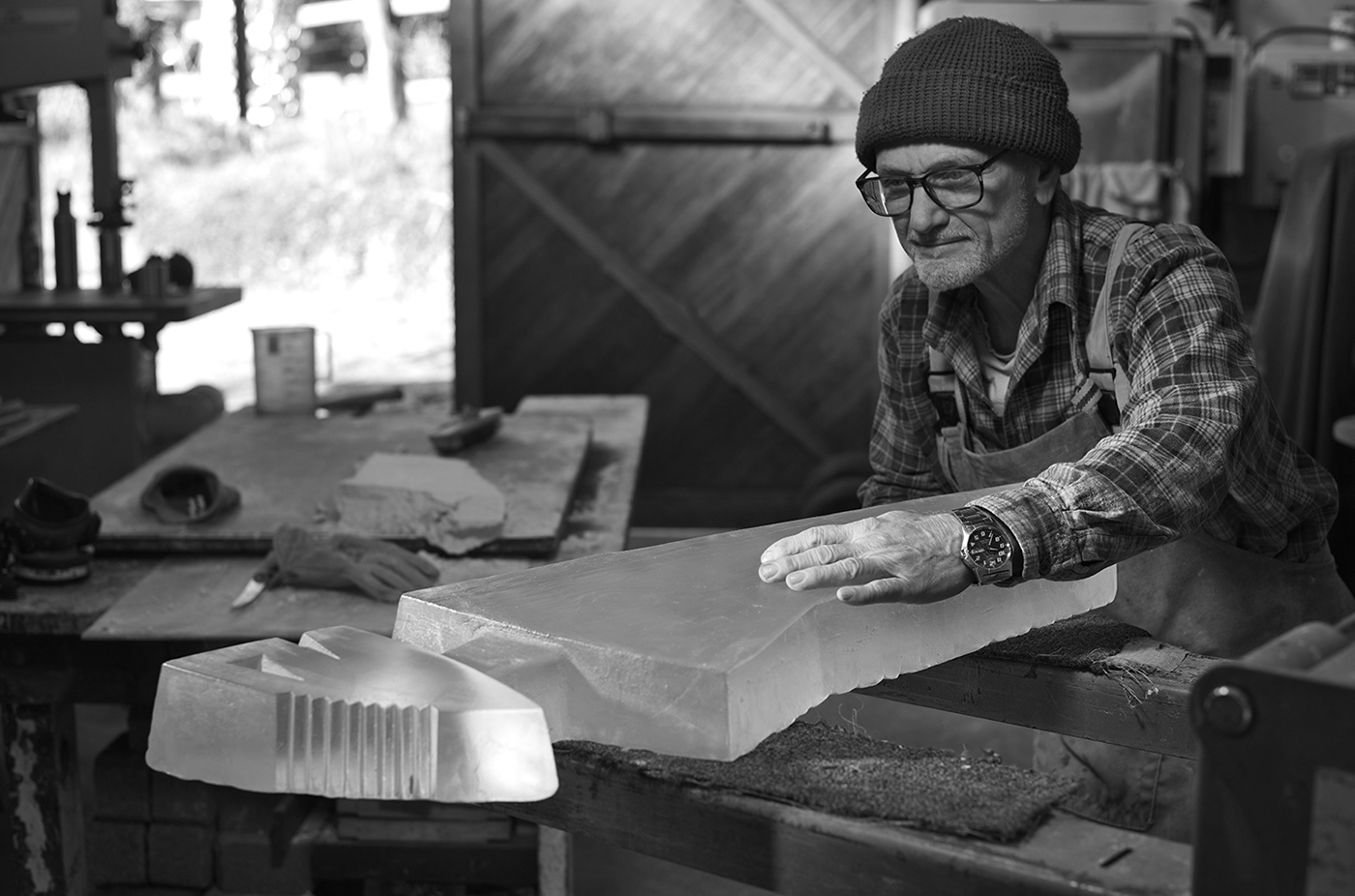
Peter removing the moulds from the kiln hearth onto the workbench.
Peter inspecting the mould filled with lead crystal after the completion of a 30 day firing schedule!

Australian artist Peter Kovacsy opening the kiln after a 30 day firing schedule
To fill each mould Peter carefully packed 40kg to 46kg of clear lead crystal into each of the plater moulds. Prior to loading the crystal it was washed and dried. Date 9th July 2021.
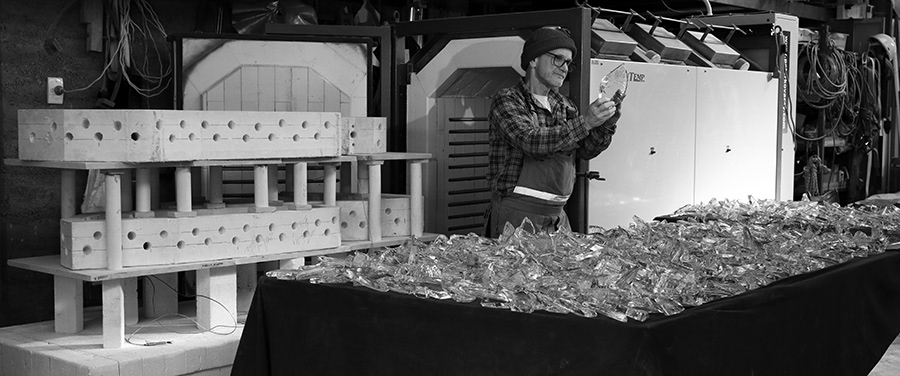
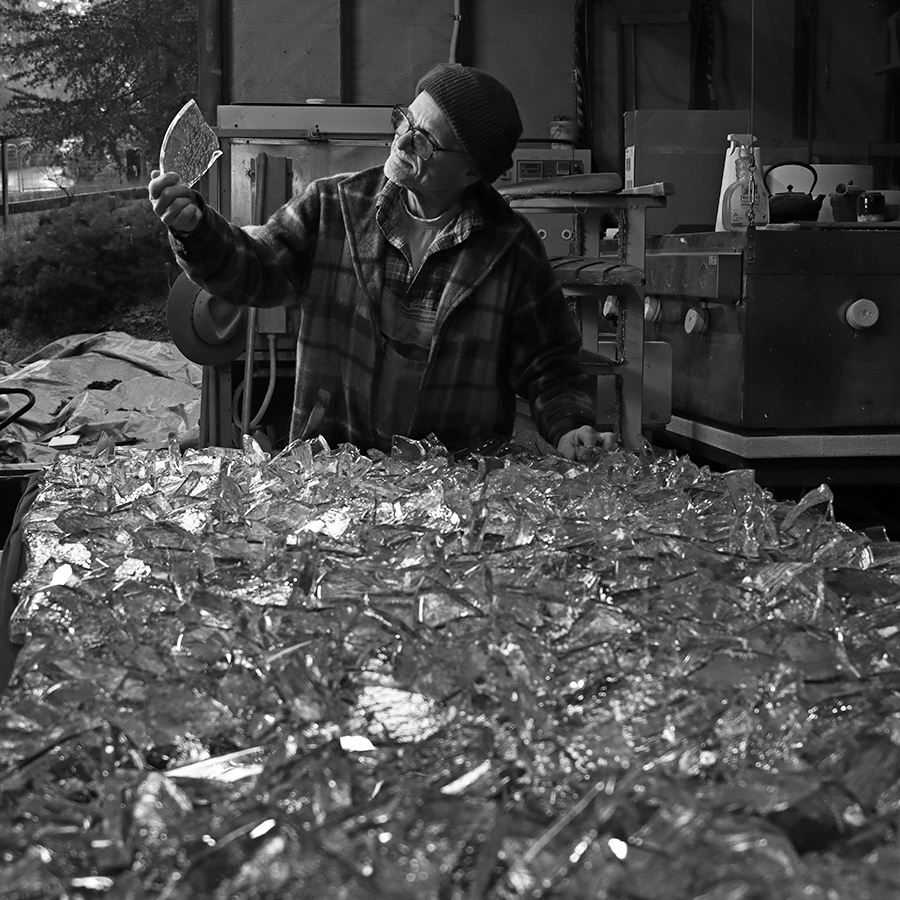
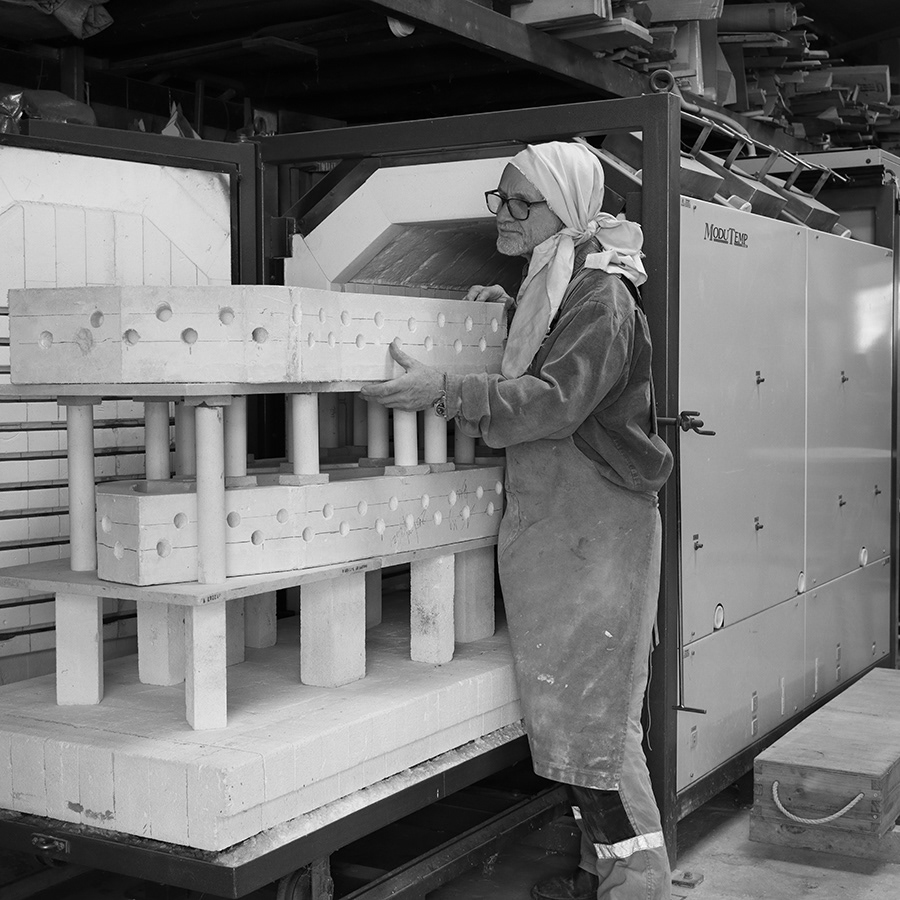
To help control thermal mass in such large moulds Peter bores 25mm holes into the side walls of the mould. The holes increase the overall surface area and aid in heat distribution and annealing.
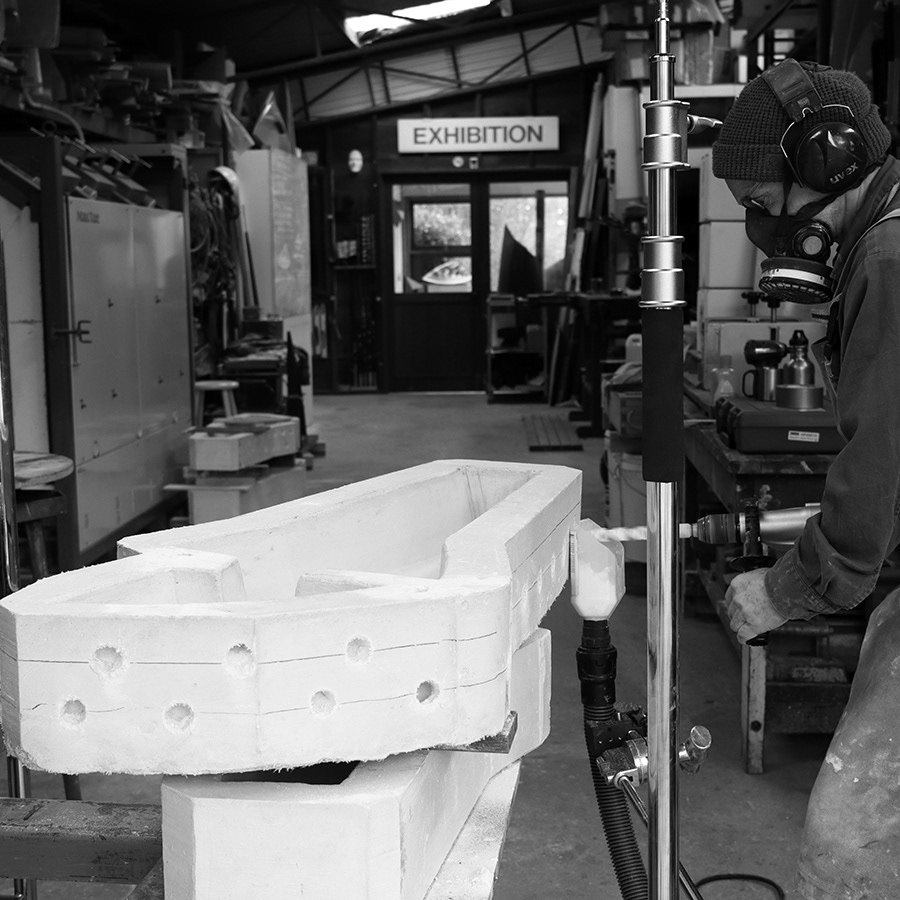
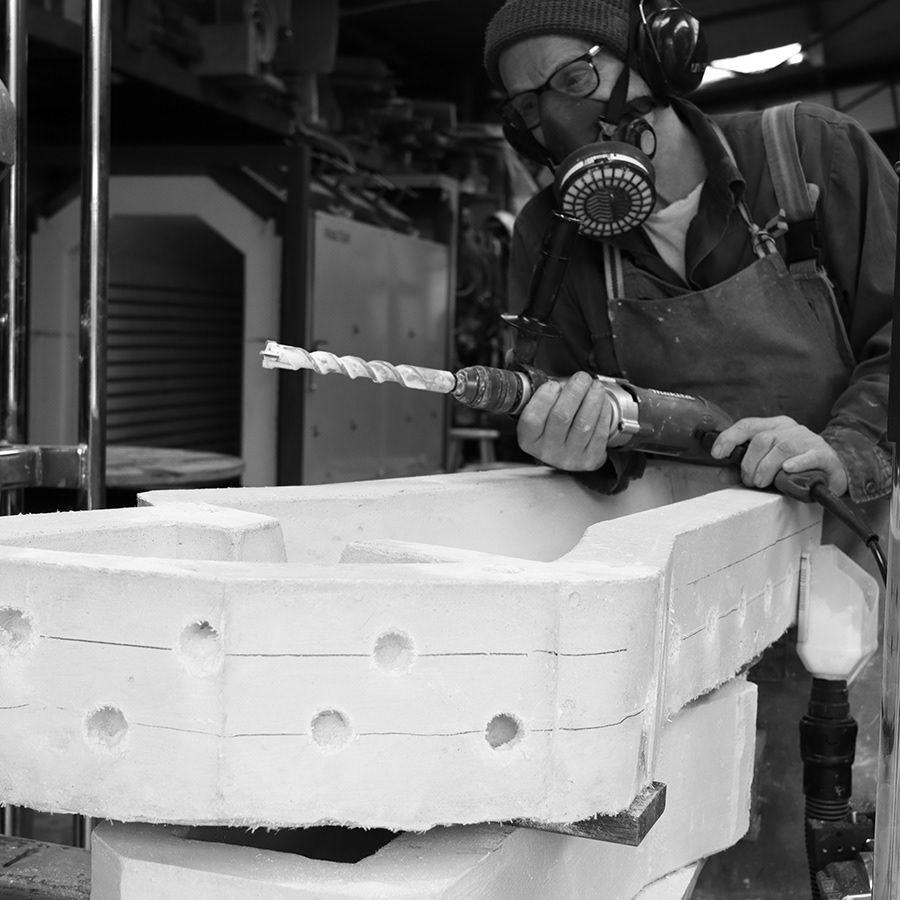
Peter packs wet moulds into a makeshift warm air drying cabinet for 10 to 12 days. The warn flow of air will pr sry the moulds and remove around 60% of the moisture.
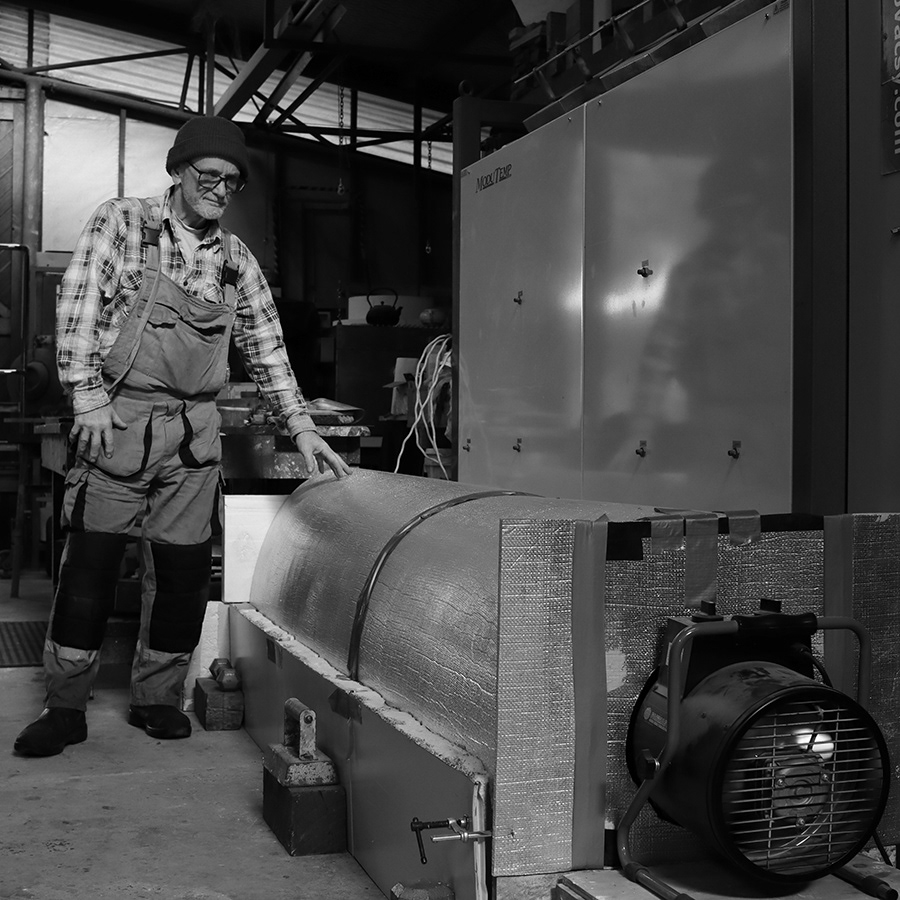
The 2 plaster moulds for He & She ready for pre drying. These mould when wet weigh from 80kg to 70kg.
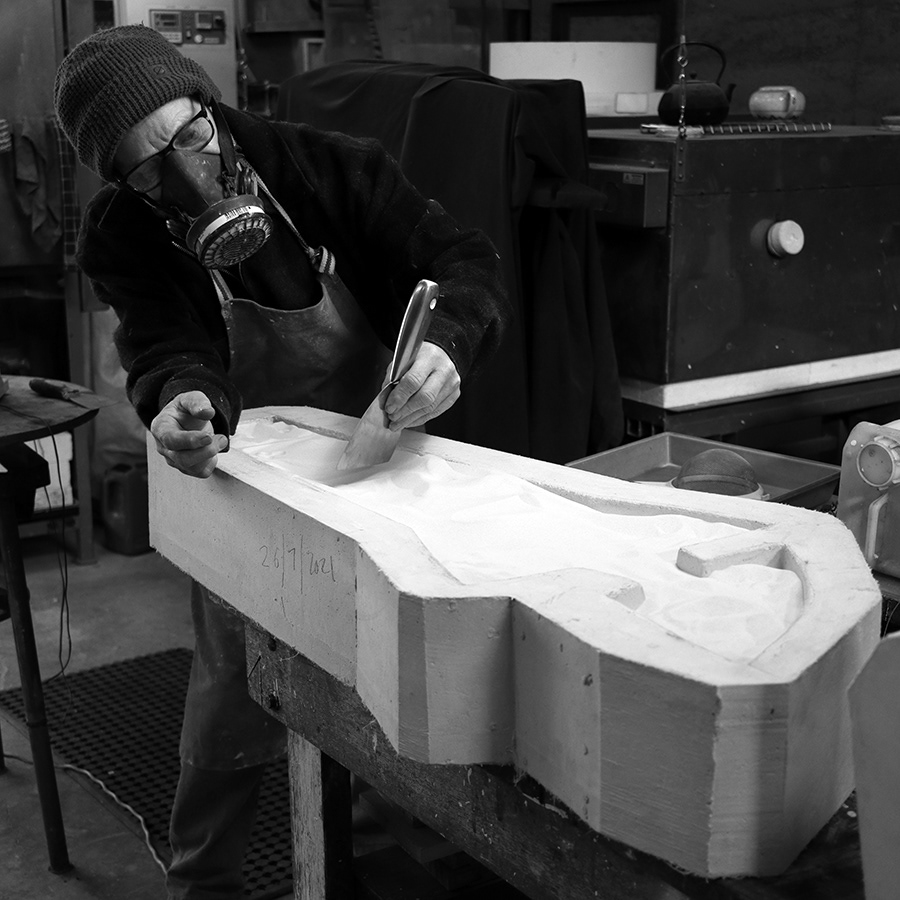

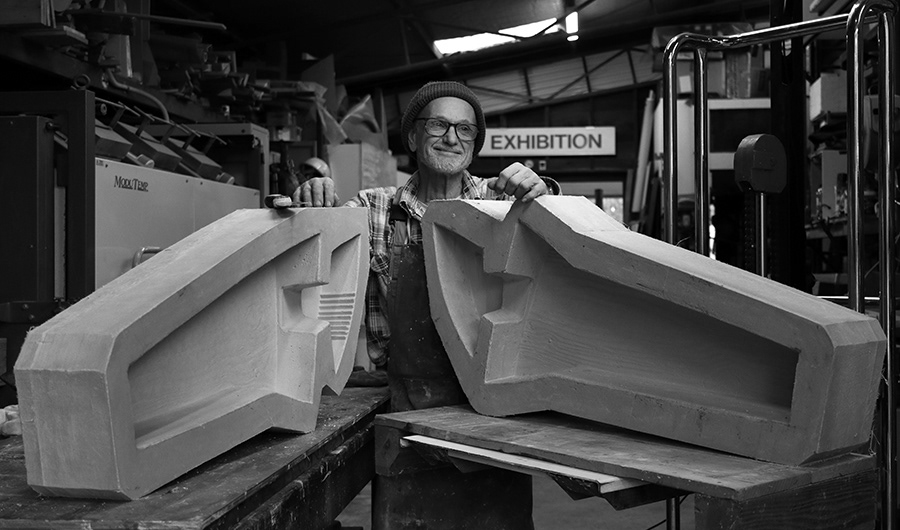
Here you can see the wet mould for He and the pattern block that was used to produce the plater mould.
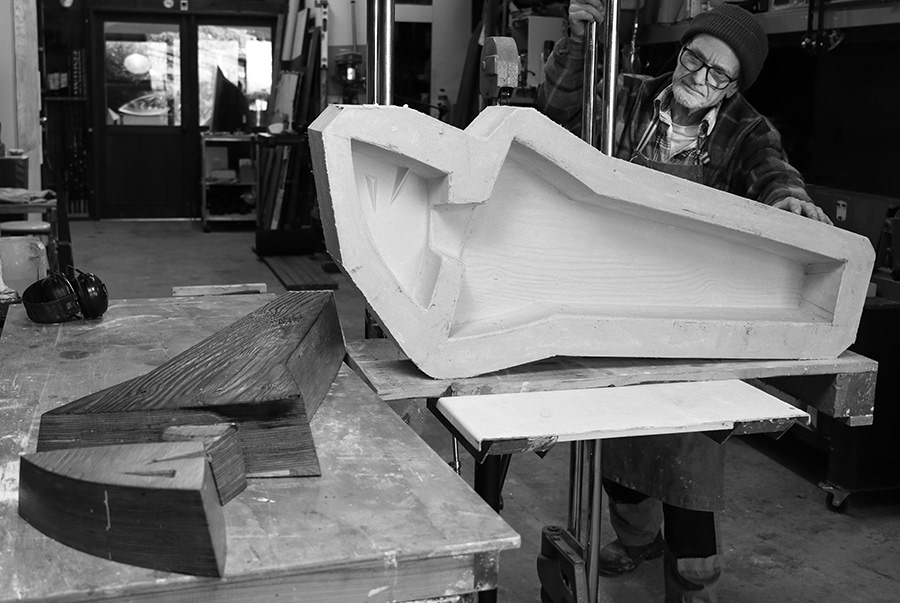
This is the plater casting mould for She, while still wet I often need to refine the surface by hand.

Each timber pattern block is made up by combining 3 components, this aids in the removal of each block from the the plater mould.


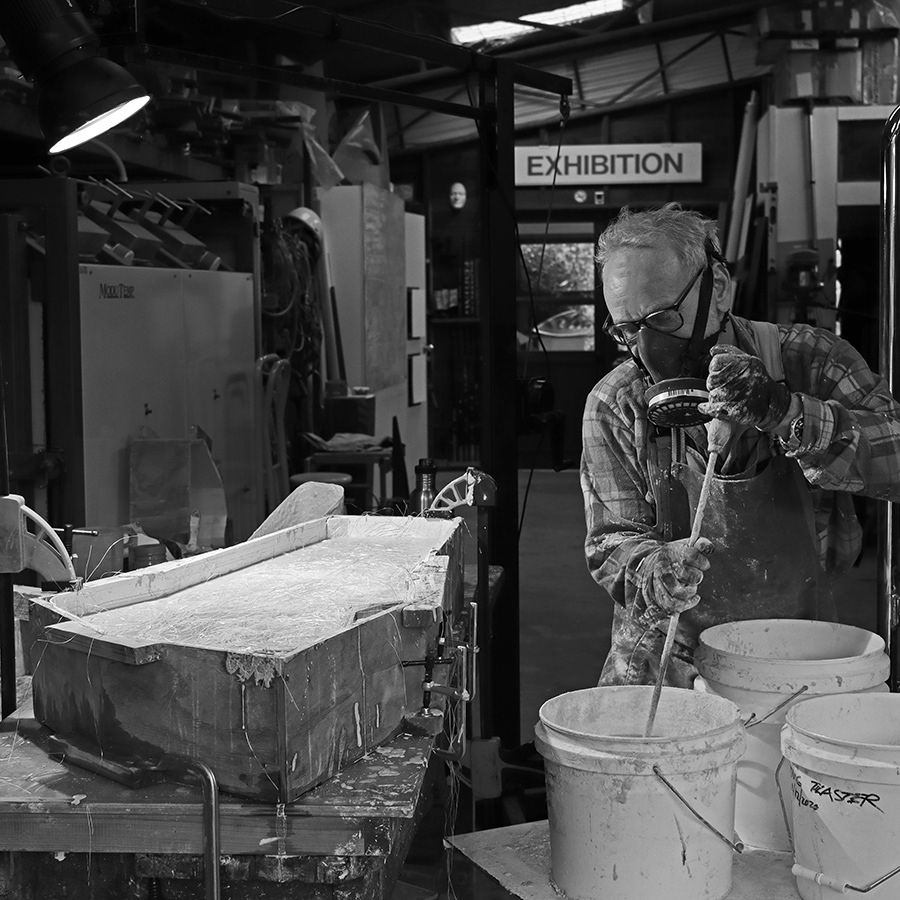

To achieve the required outcome for complex annealing Peter modifies the formwork prior to pouring each mould. Achieving an even mould wall thickness helps control heat differential during the lengthy annealing schedule.
Due to the scale of each mould large quantities of mould mix are required. For this tricky casting project two types of mould mix have been produced. A fine face mix will pick up surface details on the pattern blocks and a coarse structural mix will hold the weight of crystal and tolerate thermal load.
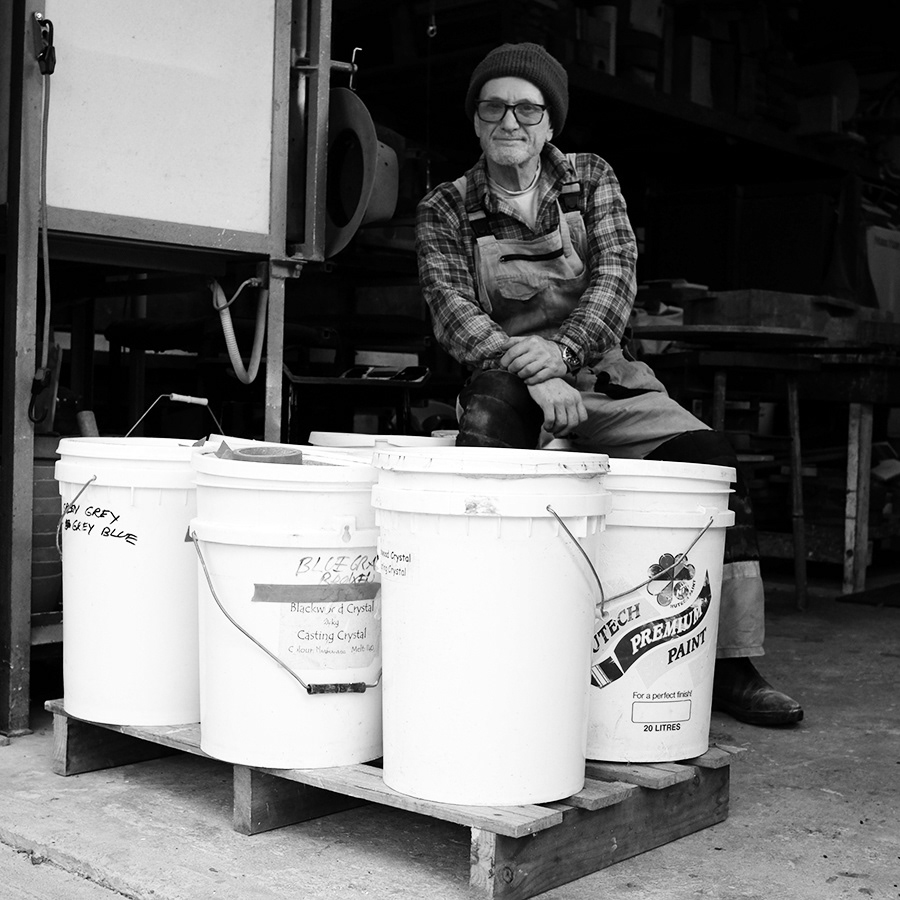
Peter's moulds for casting glass are made with casting plaster, foundry sand, silica flour, chopped fibreglass and alumina hydrate.

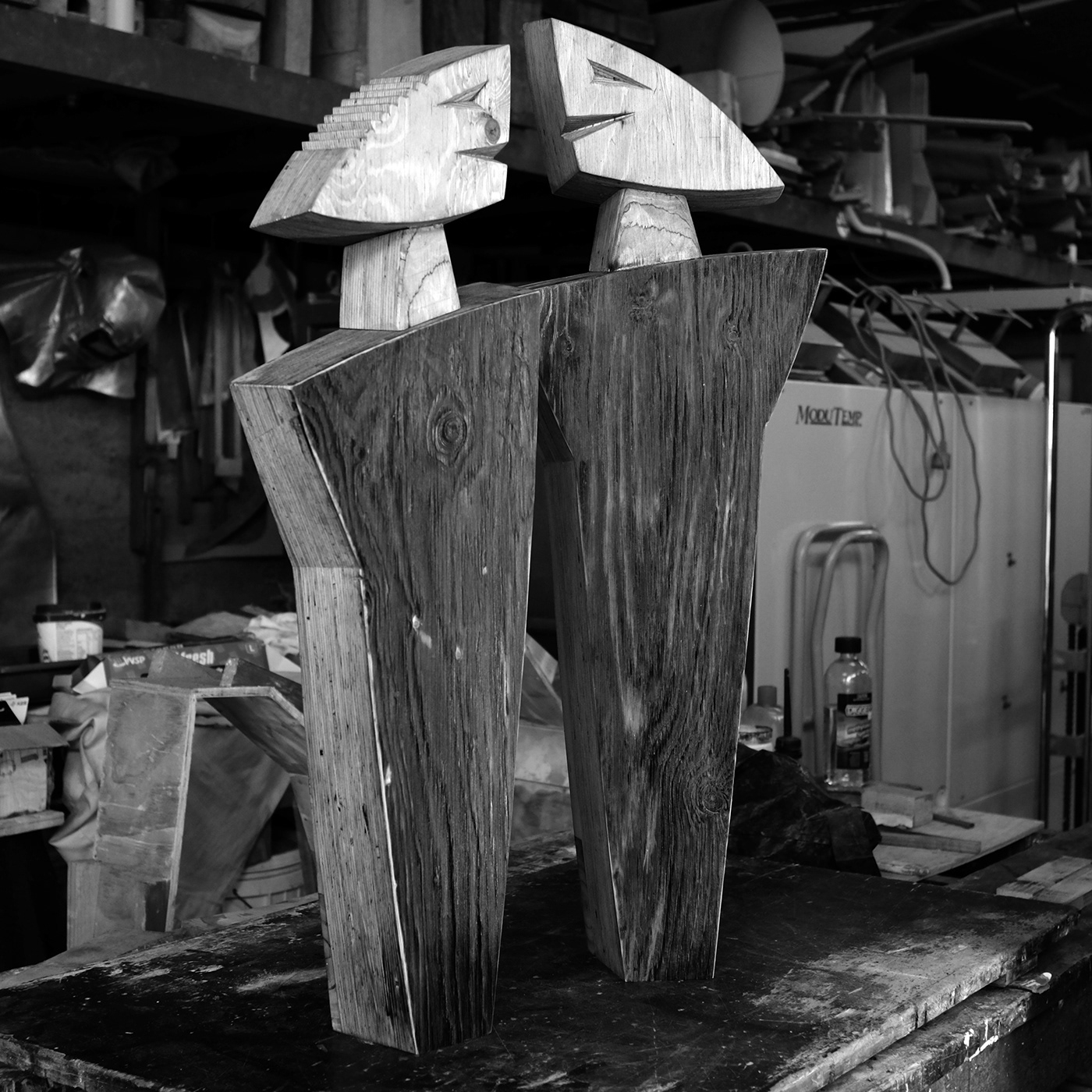
By using pine timber for pattern blocks I can generate a natural grain texture that will be captured by the mould, and picked up by the molten glass. These large glass sculptures will be cast in clear lead crystal, the natural wood grain patten will be a surface feature and major feature in the finished work.
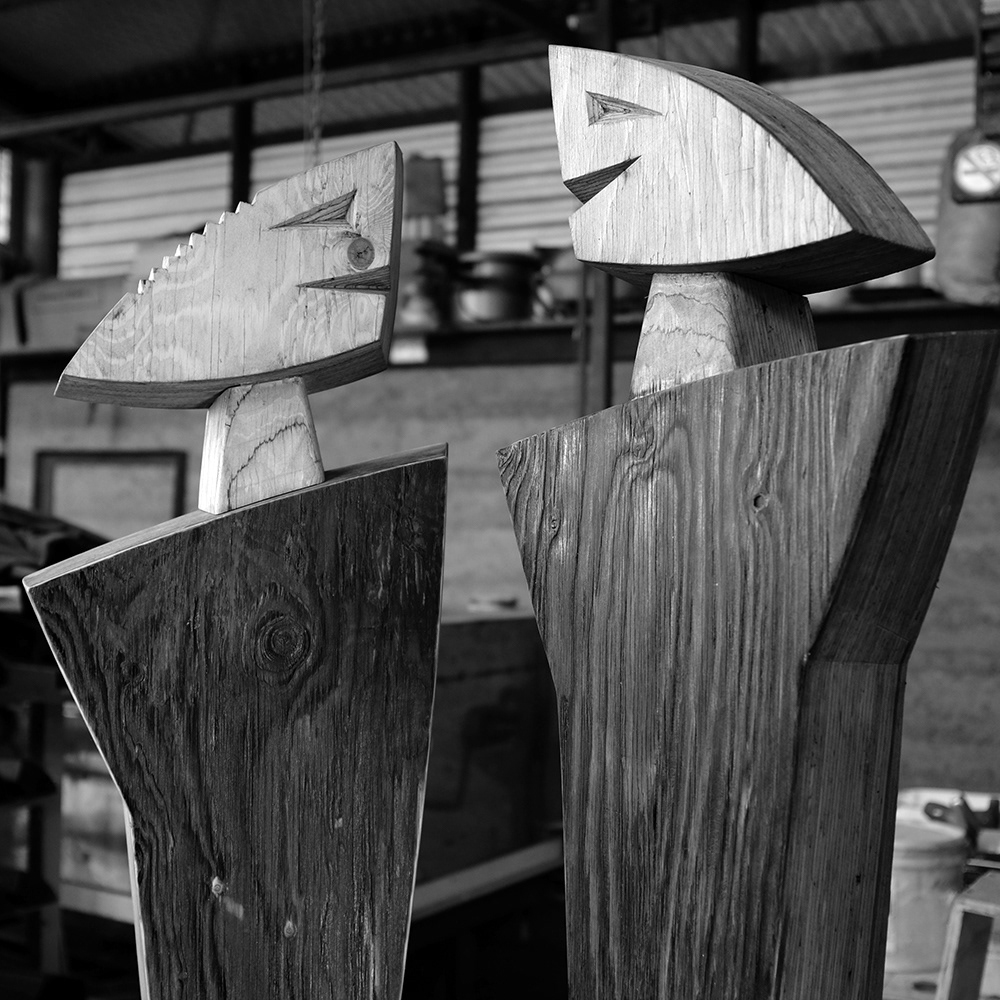


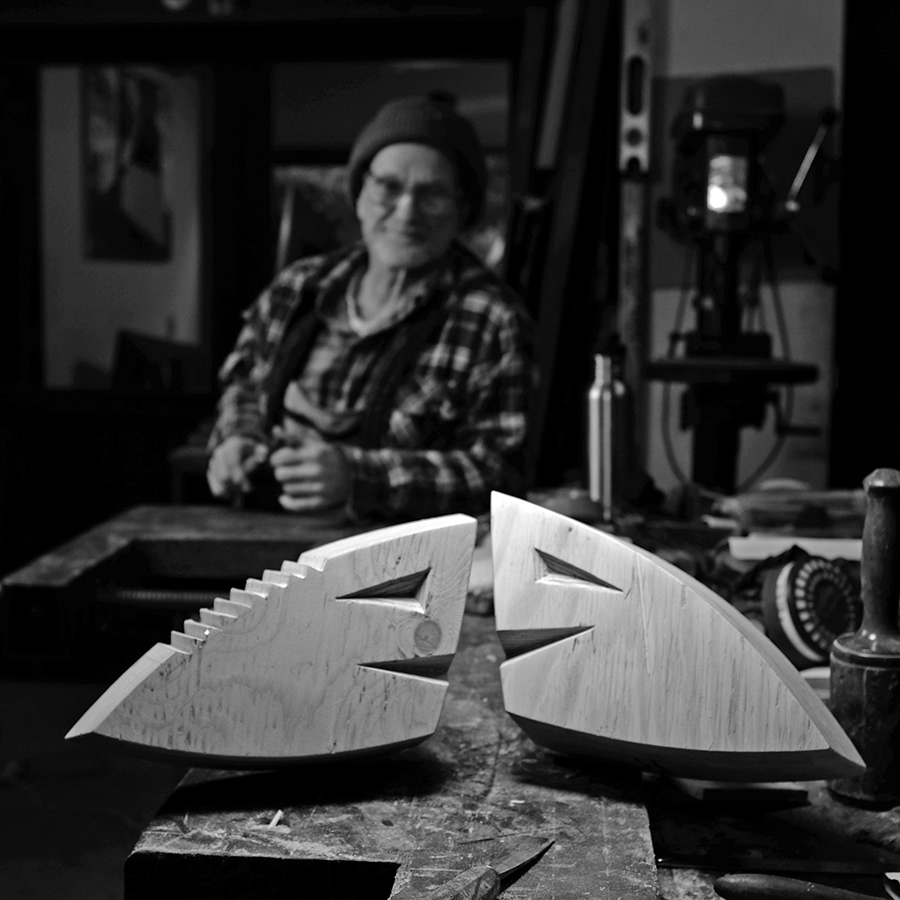
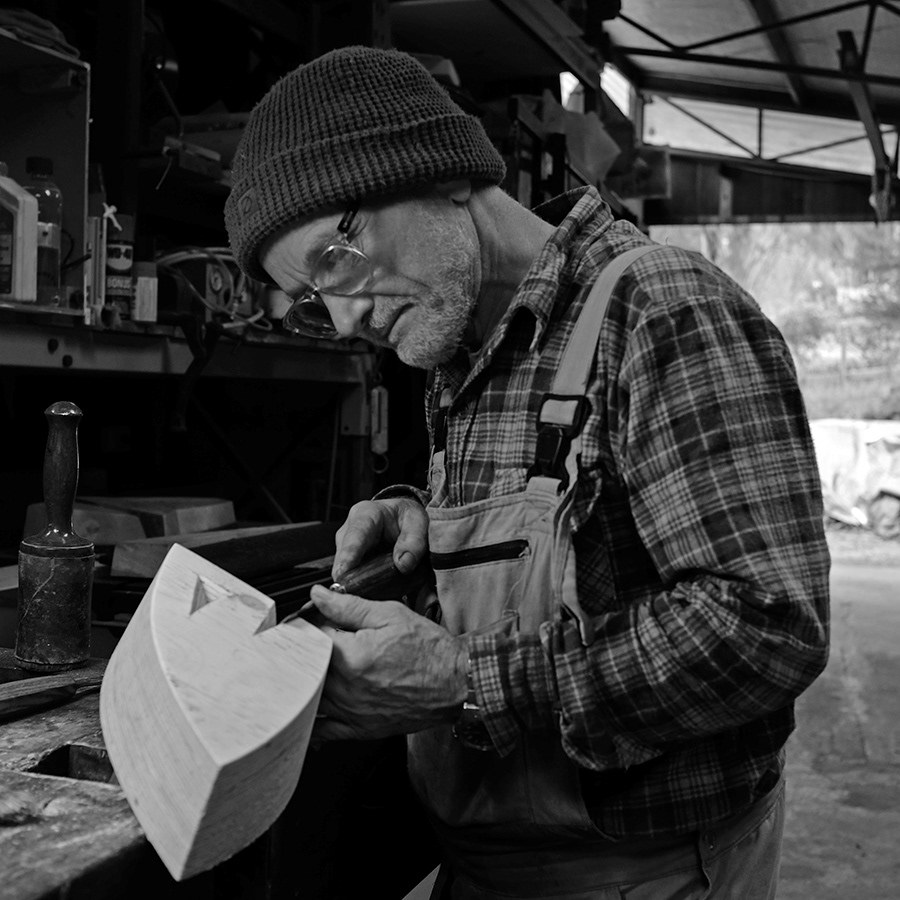
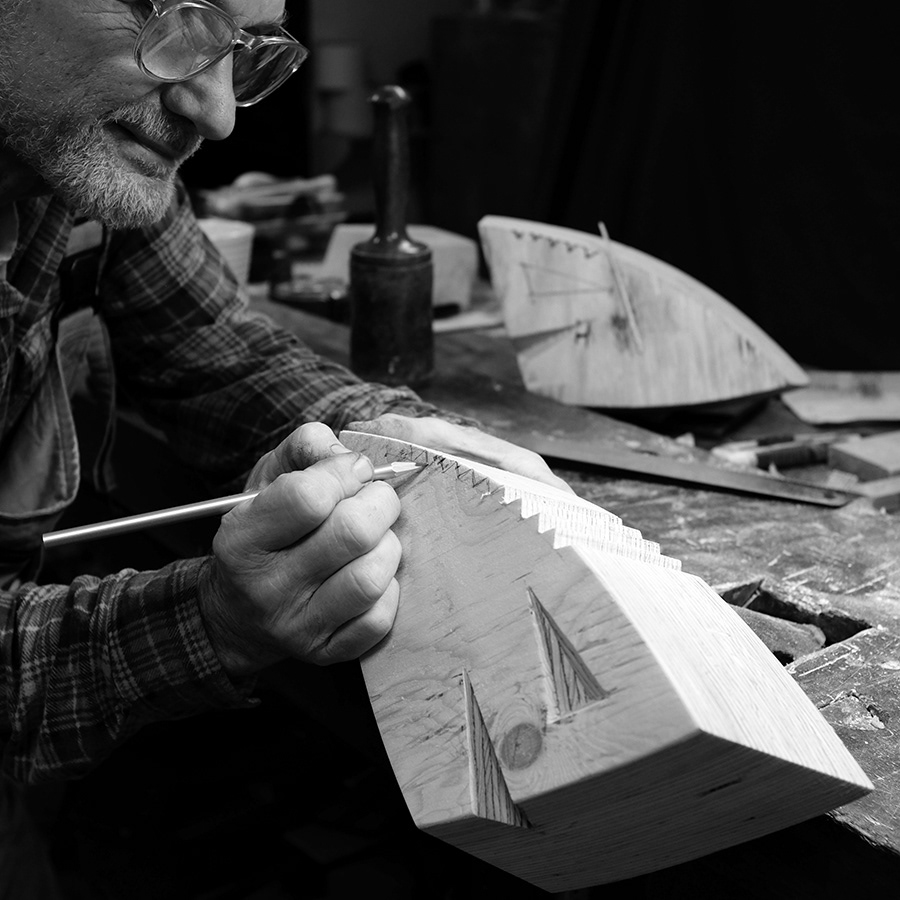
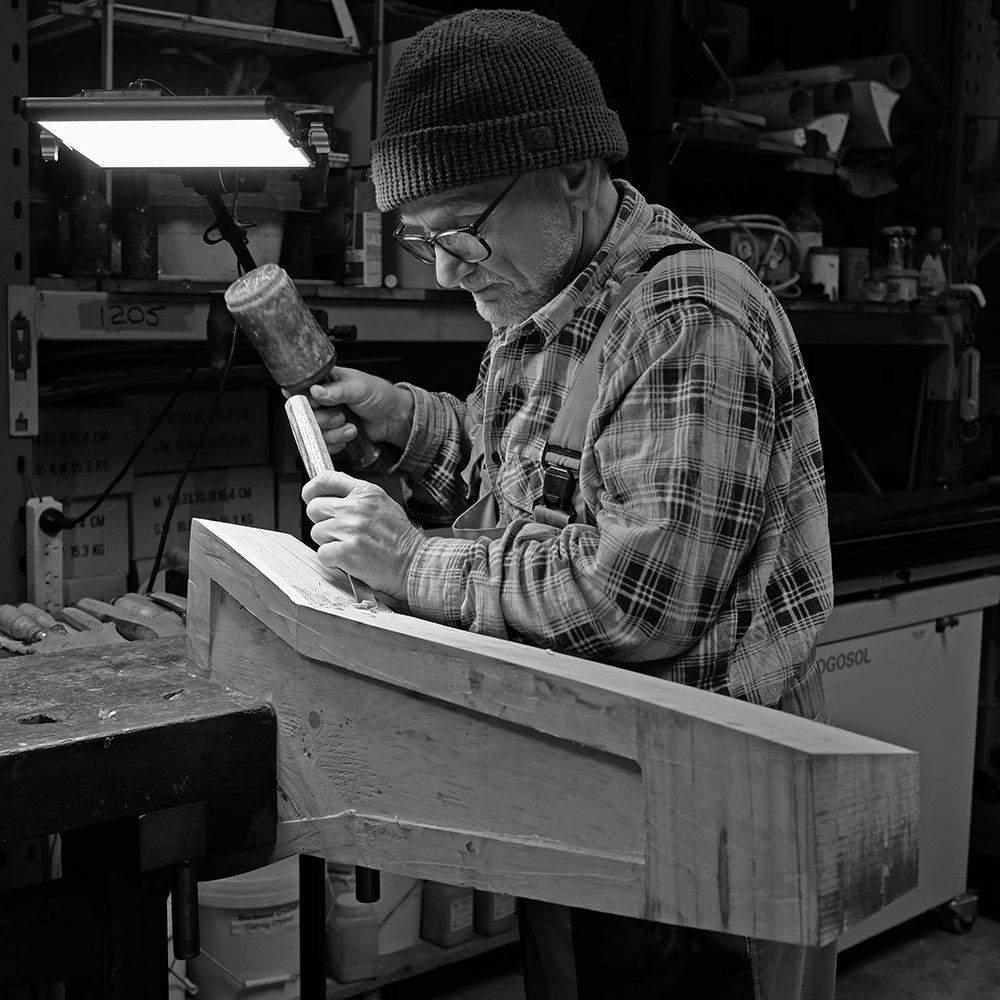
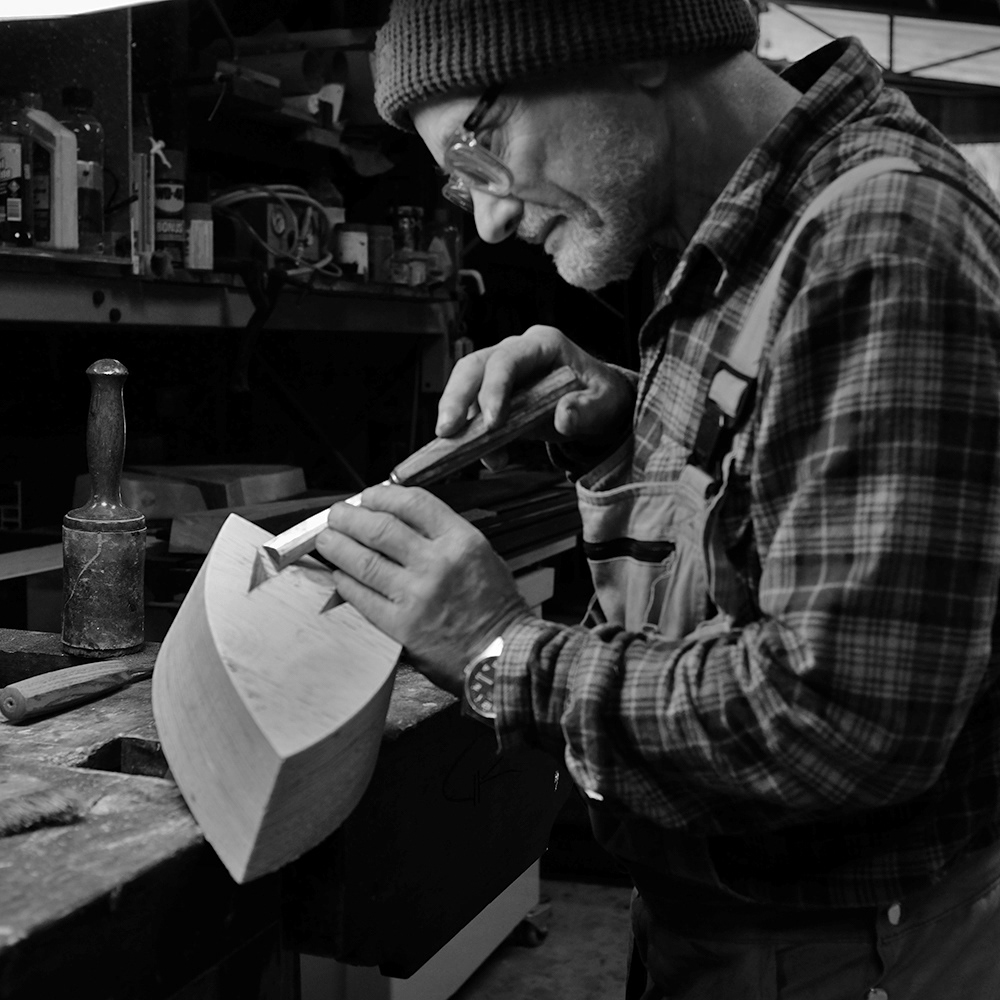
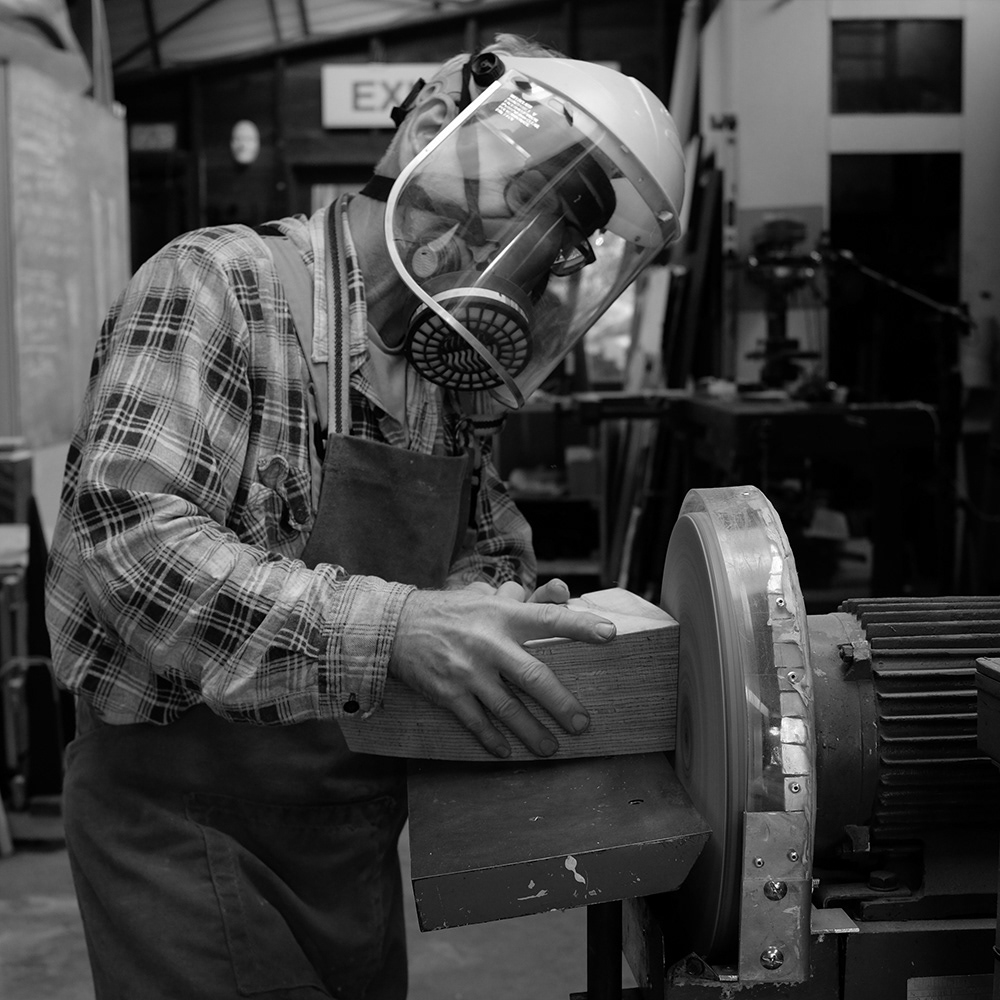

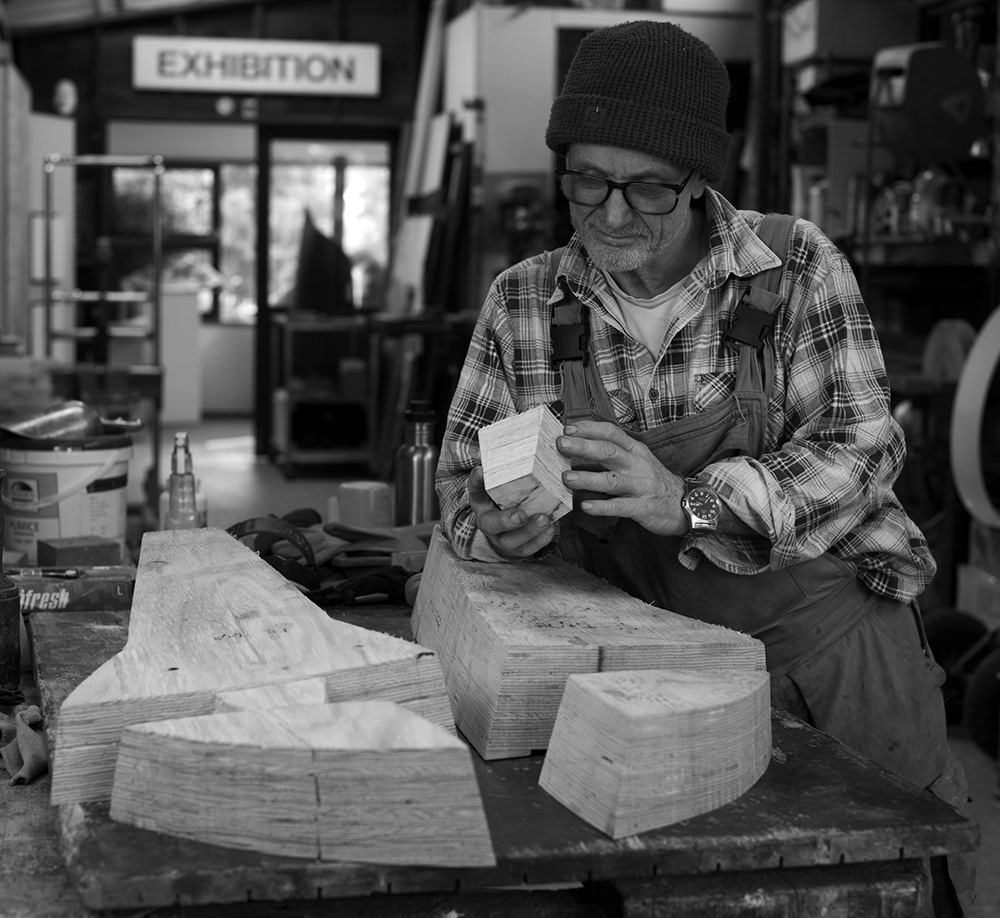
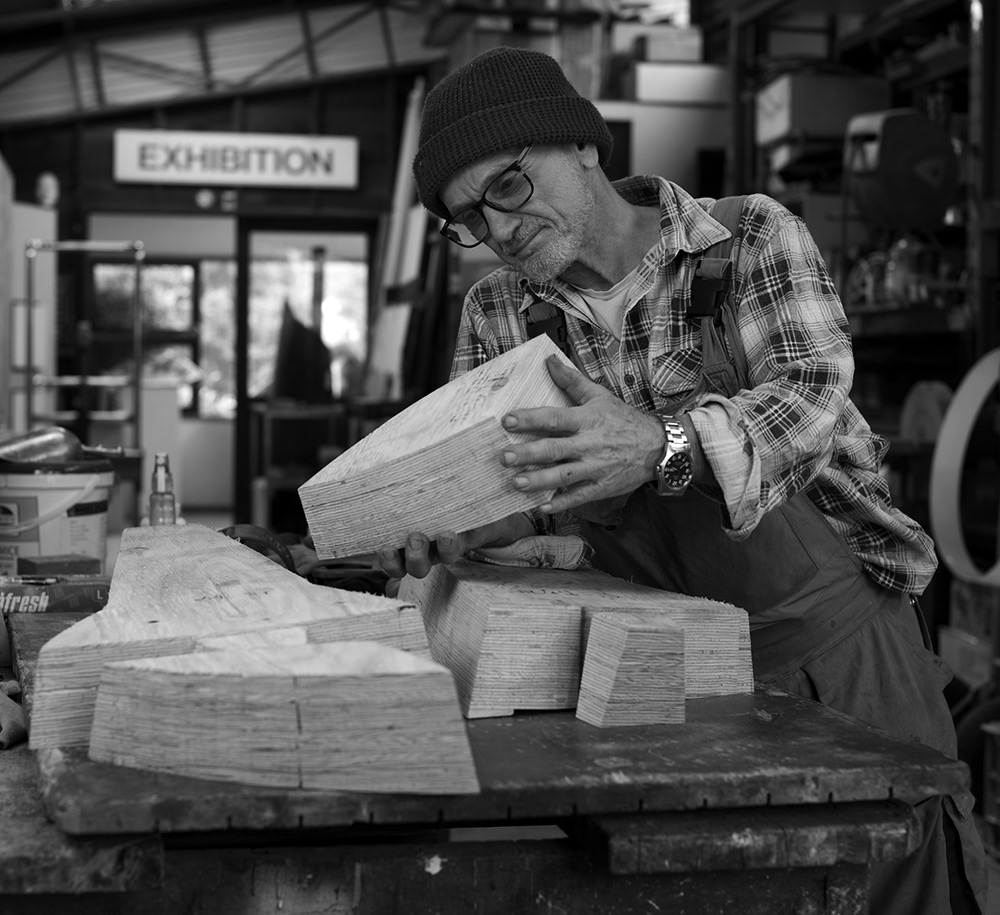
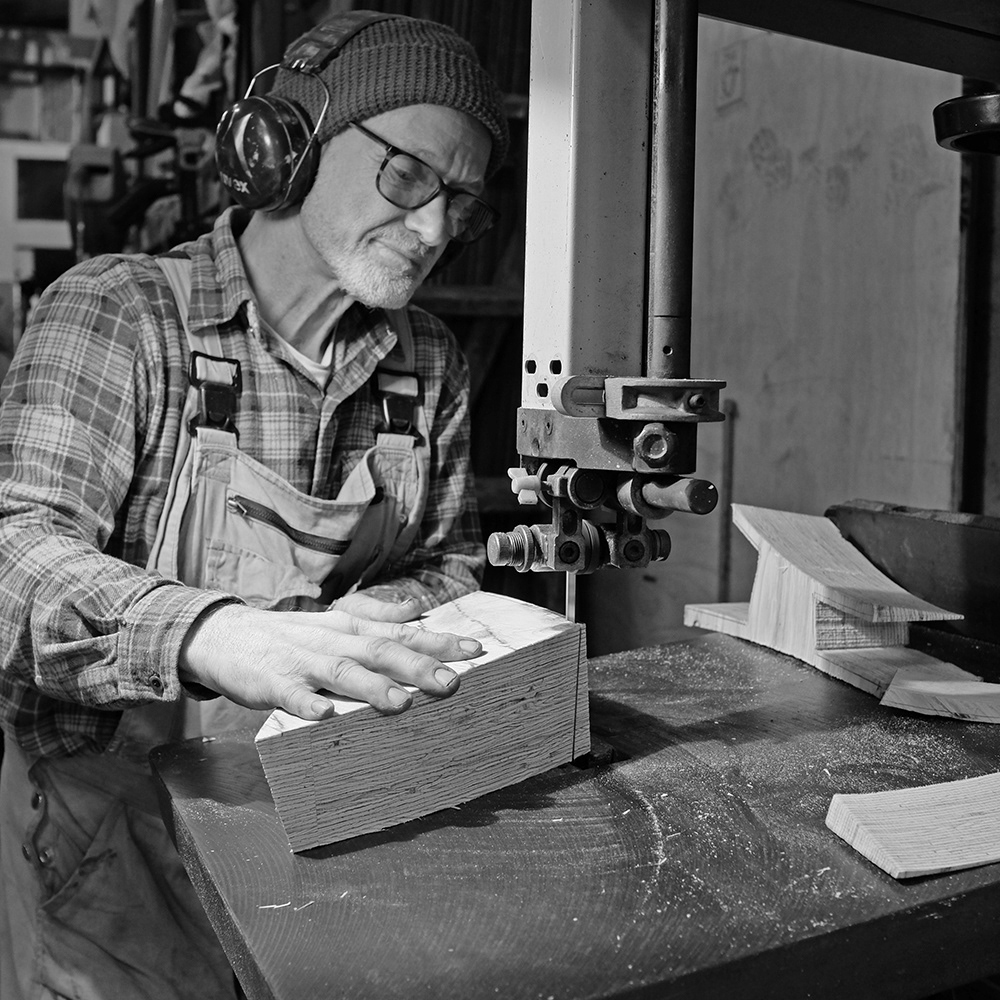


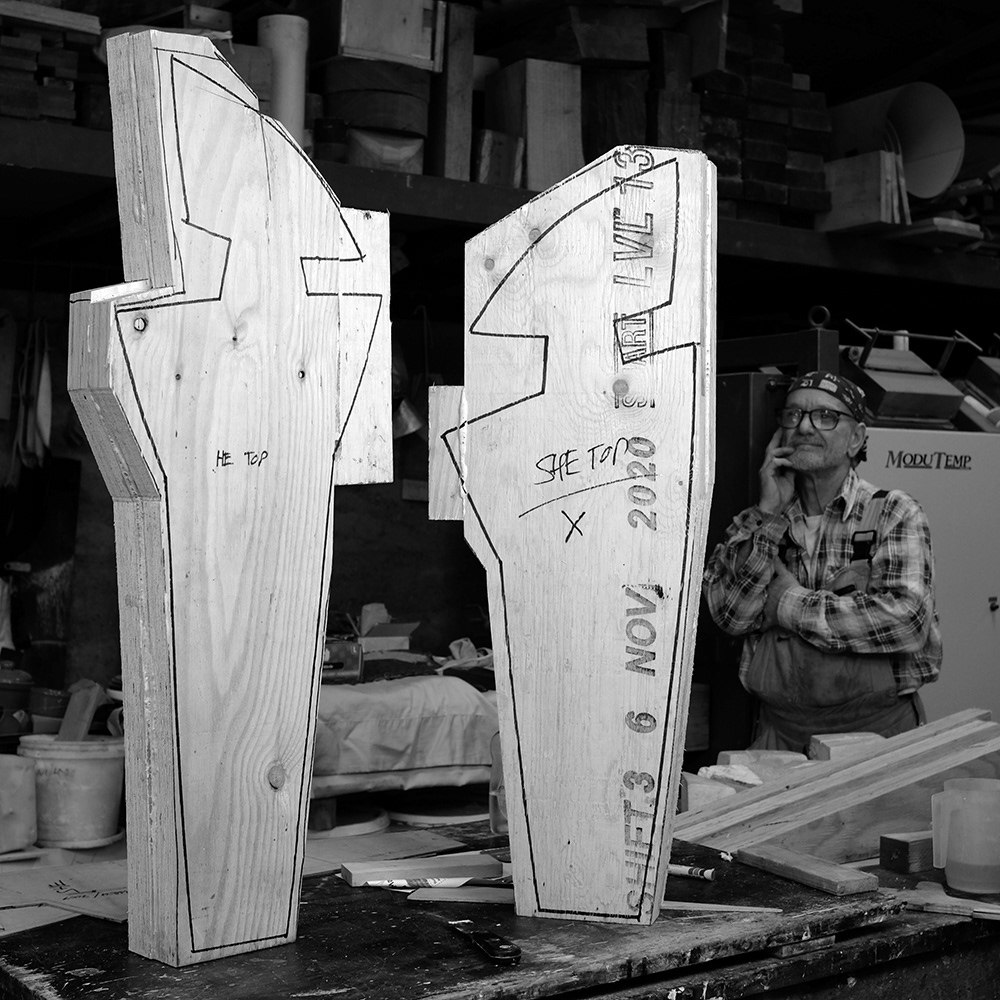
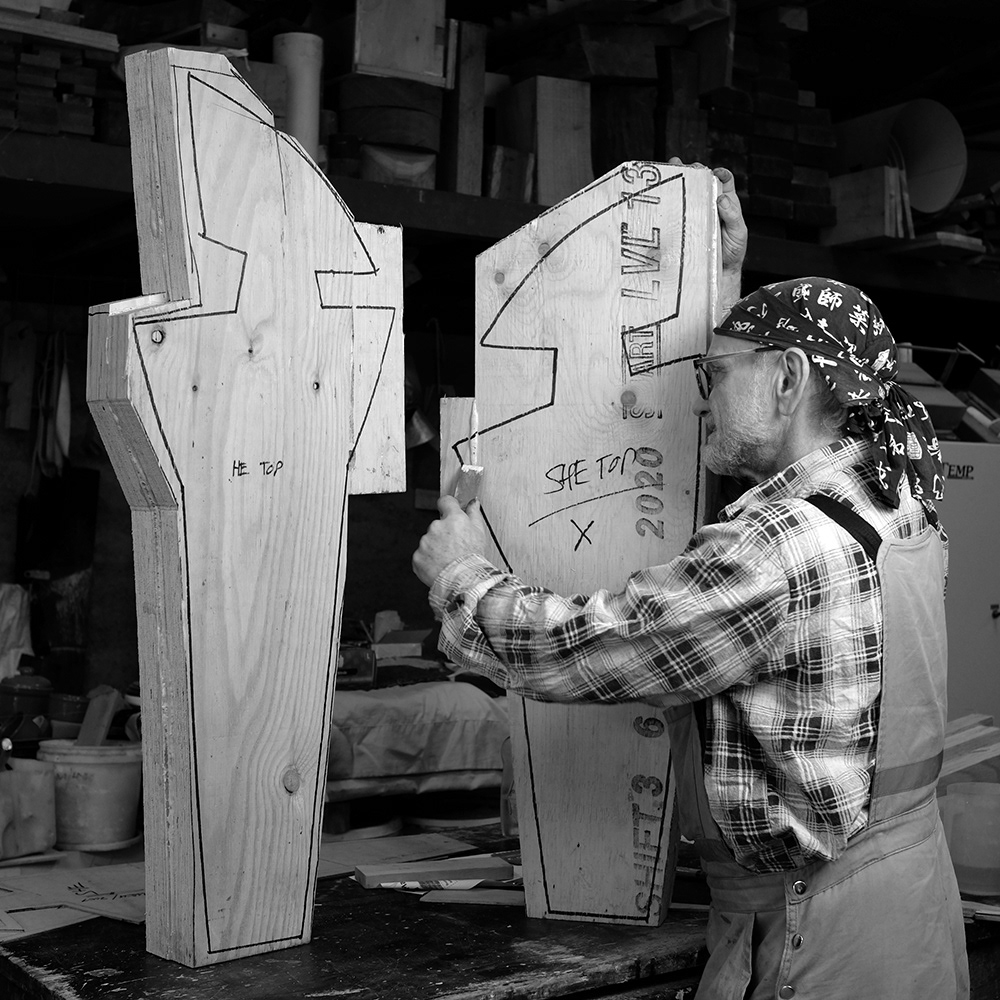
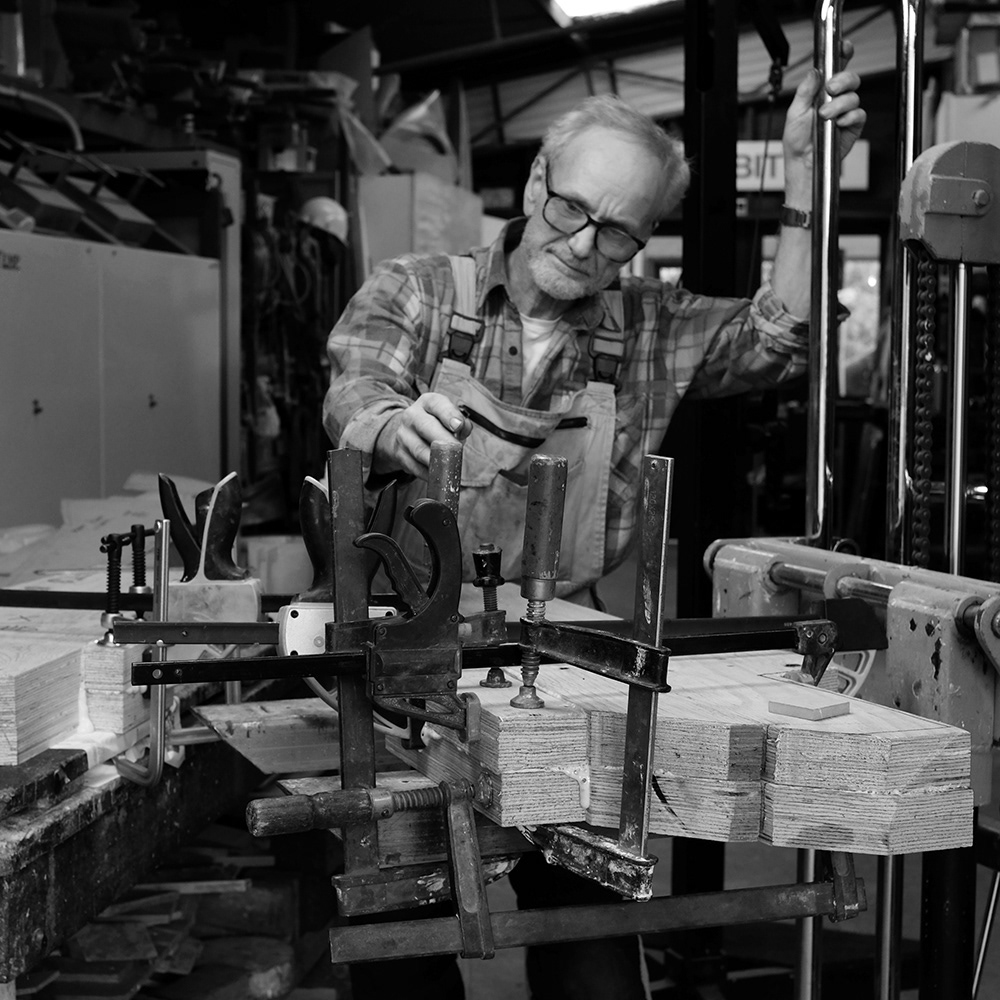
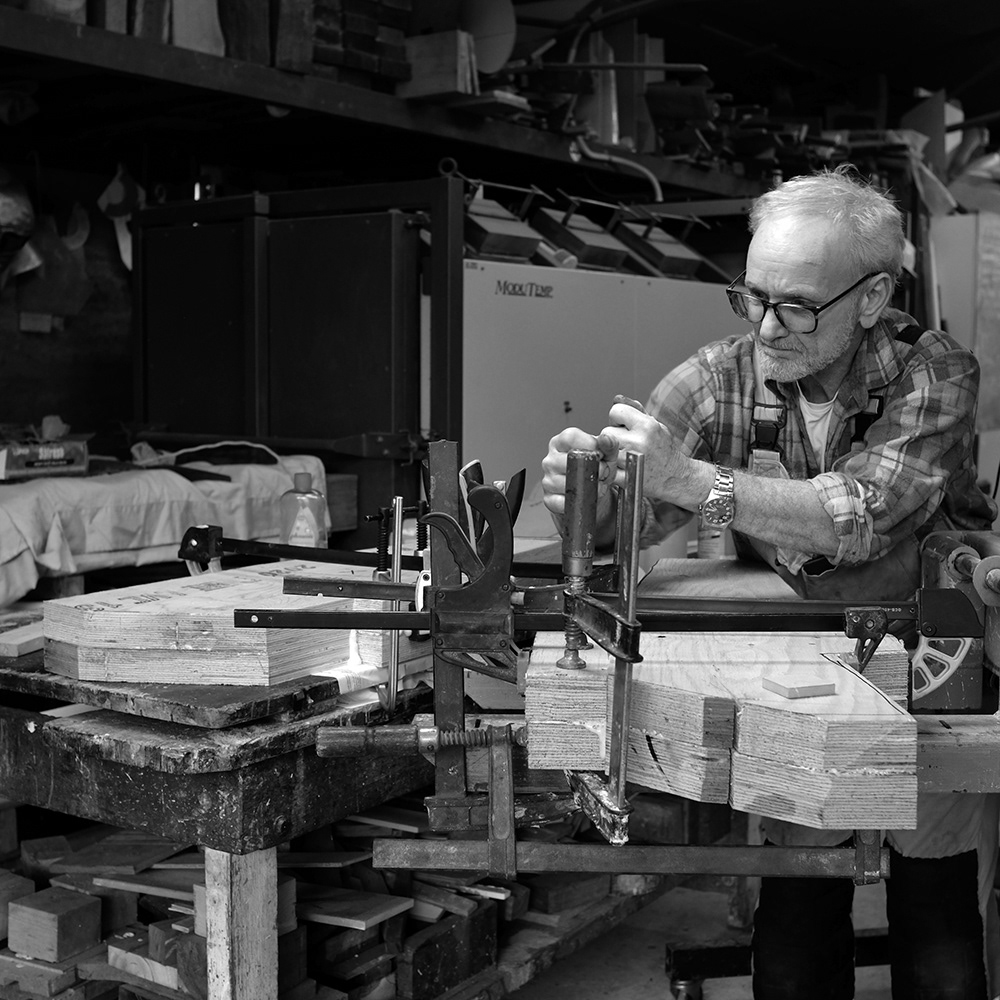
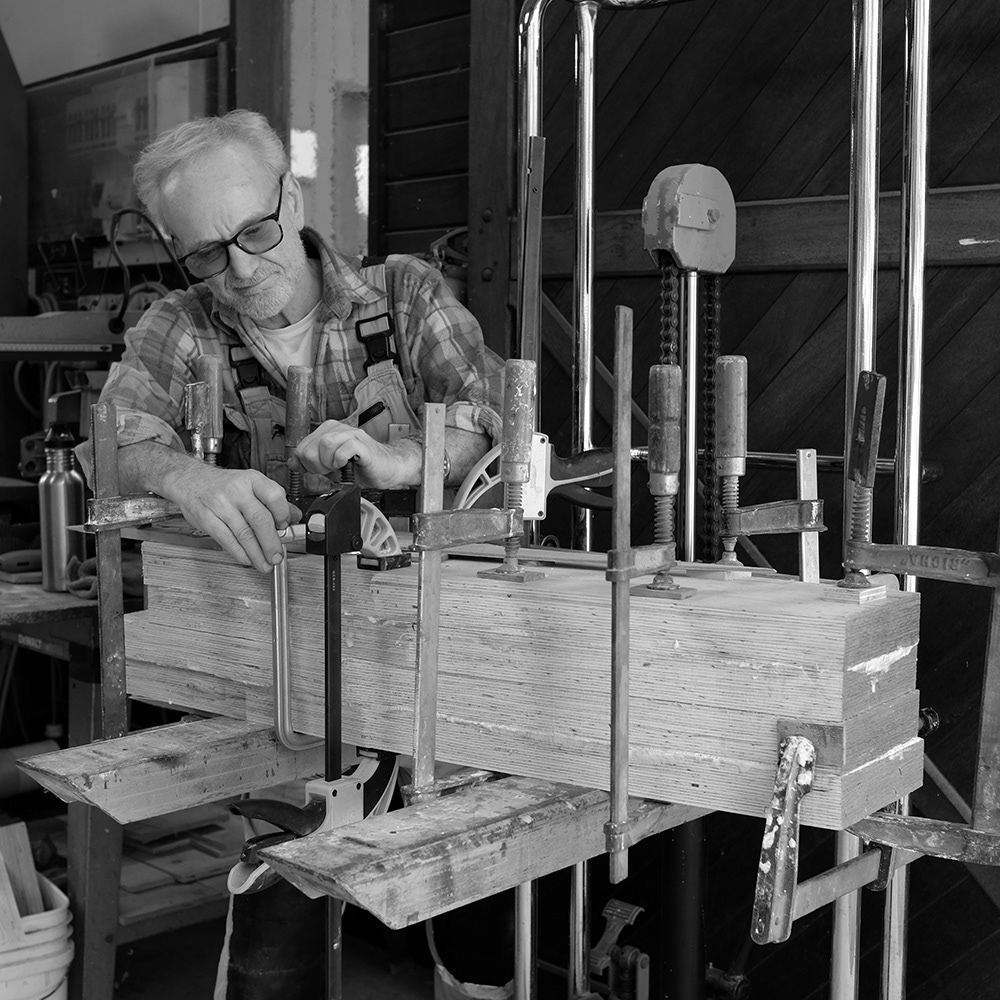

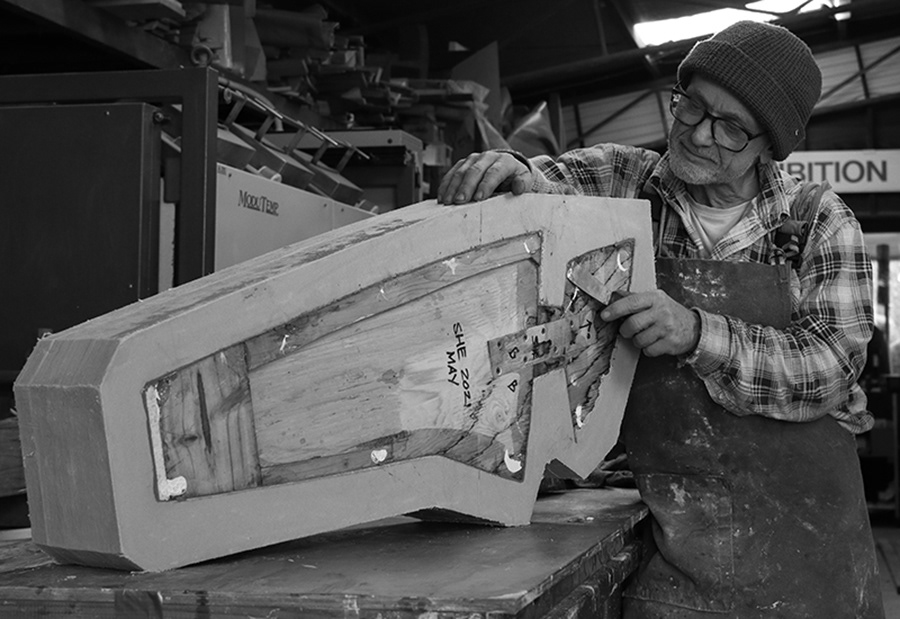

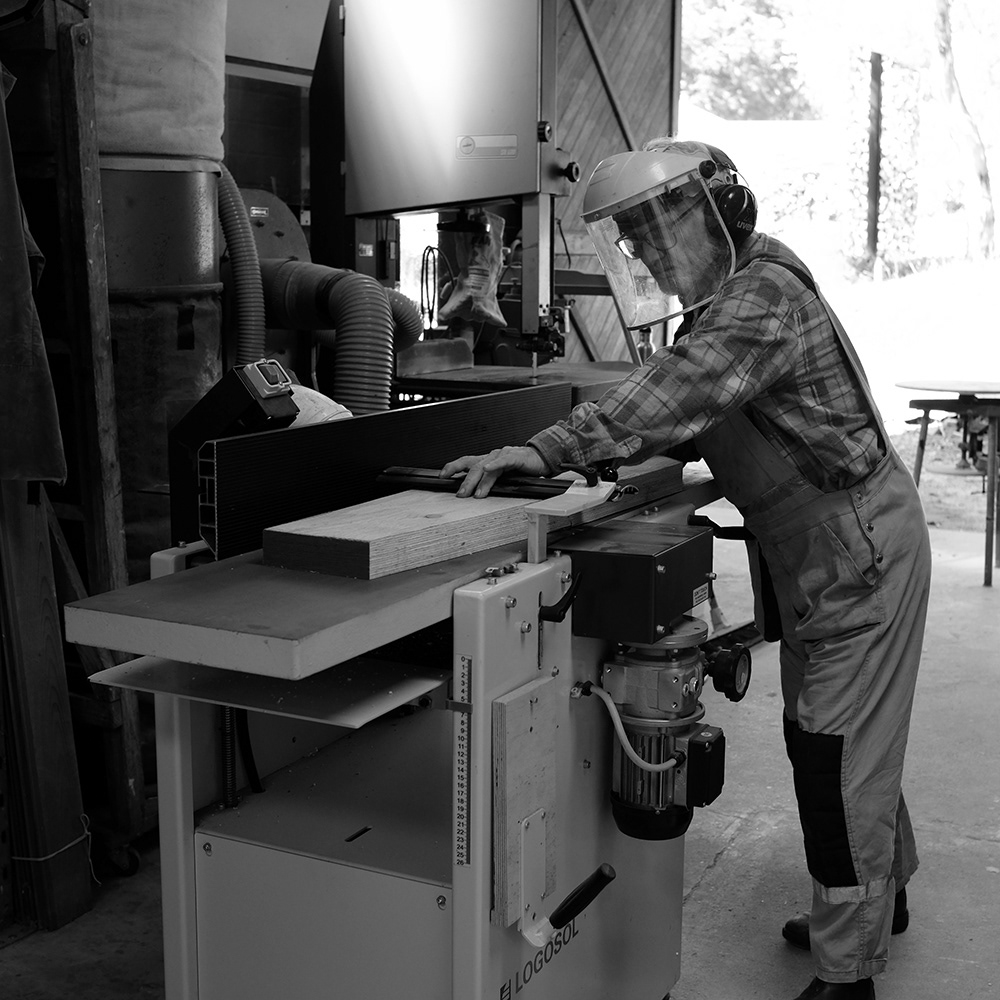
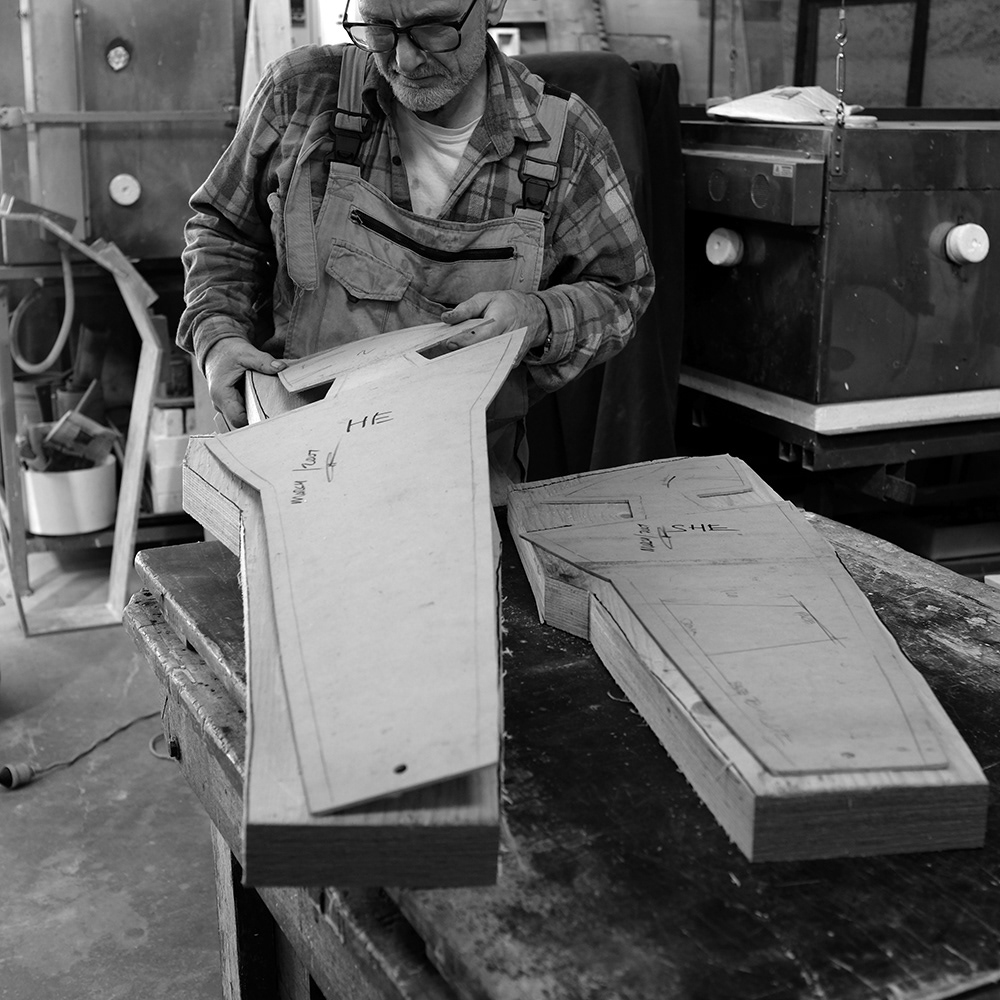
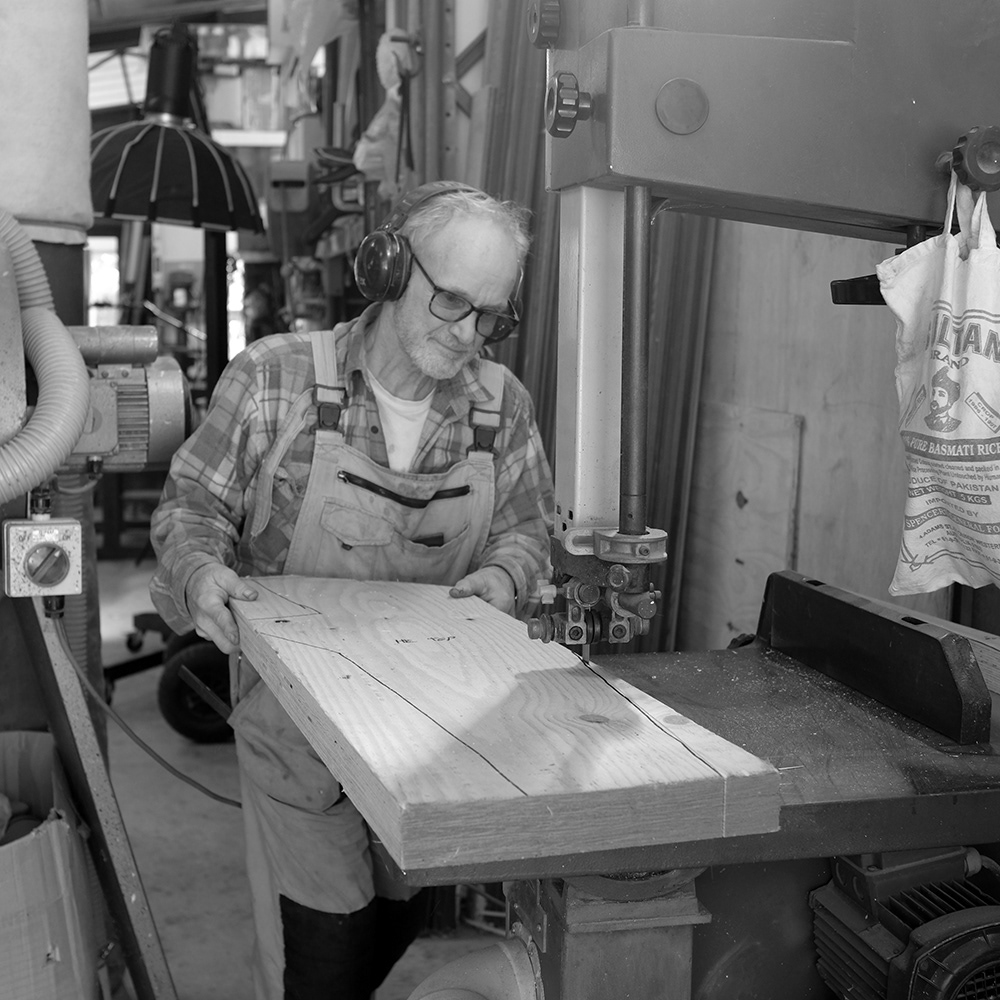

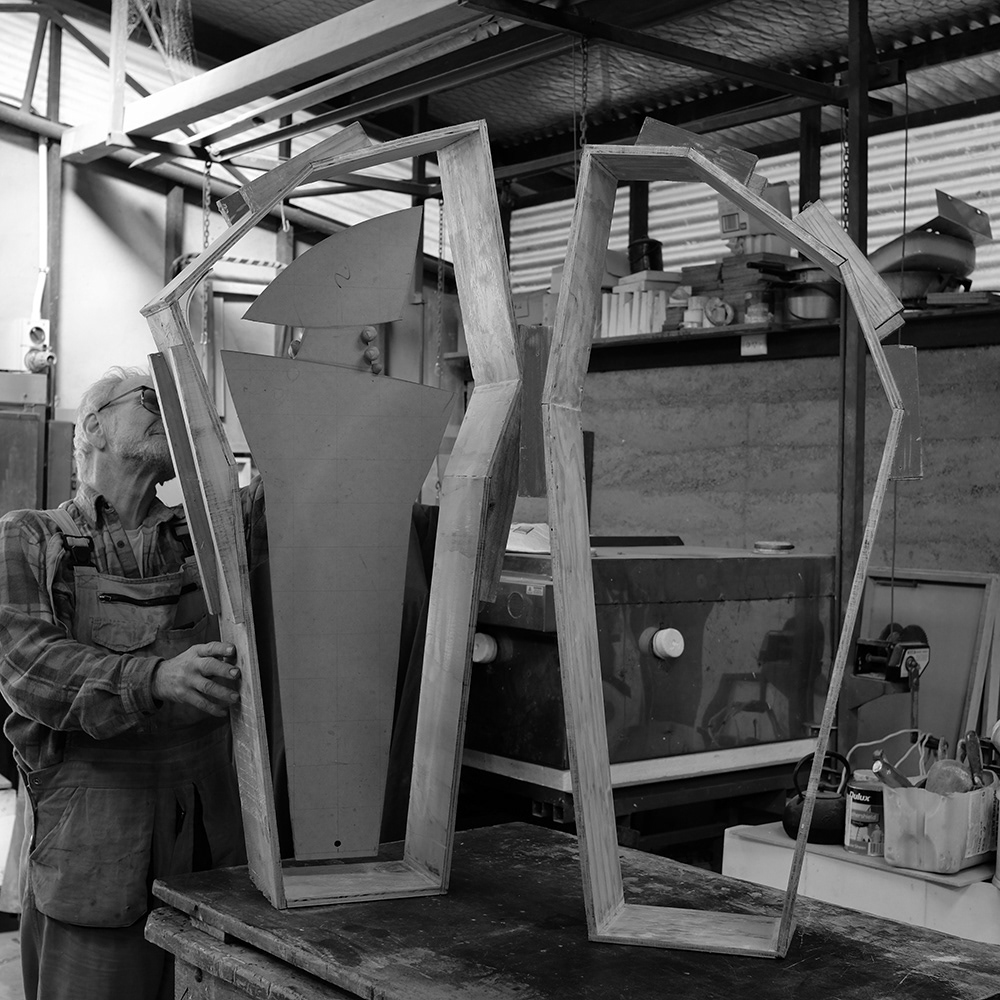

Date 1 May 2021. This is the outer formwork that I use when making a mould for casting glass.
