

As stated in the DOE 2018 Race to Zero Student Design Competition Guide, "Participants in the U.S. Department of Energy (DOE) Race to Zero Student Design Competition (Race to Zero) prepare creative solutions for real-world issues in the building industry. A zero energy ready building is a high-performance building so energy-efficient that a renewable energy system could offset all of the building’s annual energy consumption. Teams must demonstrate the effective integration of building science principles and best practice guidelines for the building envelope and mechanical systems."
Summary:
Located on the 1400 block N. Marston St. in Brewerytown, Philadelphia, this project aims to find an alternative solution to low-income housing. There have been many public housing developments in the neighborhood, however, they are of too high density, cheaply built, and visibly different from market rate housing. The goal of this project is designing low-income housing that is as desirable as market rate housing, while reducing gentrification, and creating a better quality of living. The urban detached model has not yet been investigated in the city of Philadelphia and aims to challenge PHA's affordable developments. PHA has made efforts exploring the single family home that actually houses multiple families. We are constructing the single family home. Through the design process the low-income model and market rate model will be analyzed alongside each other to prove that the low-income detached model can be just as energy efficient and desirable as the market rate through more cost effective means.

Design at 30%
During the second semester of the competition I recruited teammates to combine our efforts to make NewMod produce net zero energy. Our team was selected as one of the finalists to present our design to a panel of industry expert jurors, compare our efforts to those of other teams, learn from presentations by thought leaders, and create contacts within a variety of organizations dealing with energy consumption. The winning teams are recognized at an Awards Banquet, and the winning designs are published on the Race to Zero website. We had the honor of presenting at the National Renewable Energy Laboratory in Golden, Colorado in April 2018.
Here is our final written submission including construction documents:









































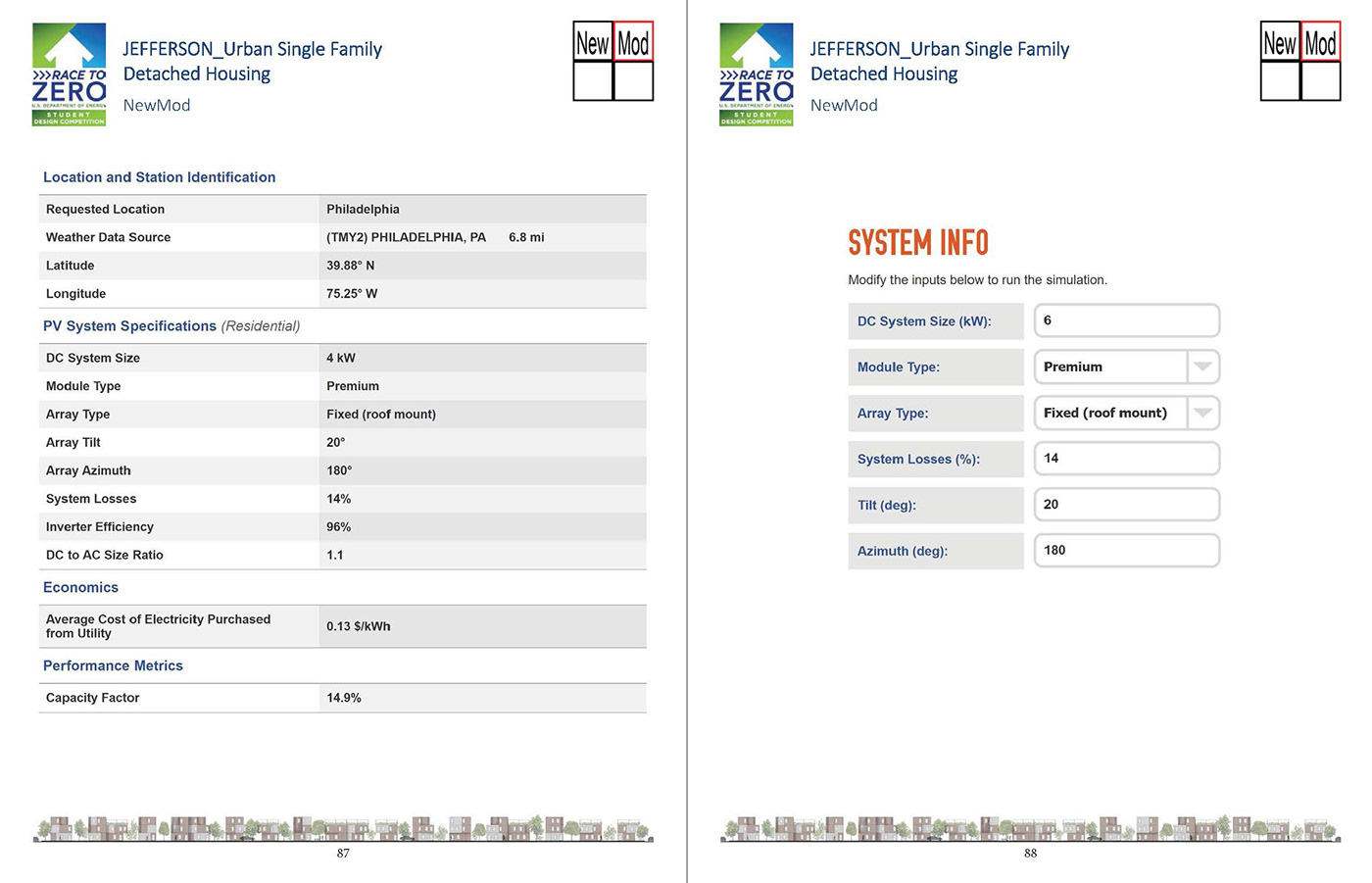



Here is our presentation given at NREL to industry leaders and jurors:

Hello, we are NewMod, from Thomas Jefferson University. (Introduce ourselves)

We worked with several Industry partners through the development of this project.
-Simplex Homes, a Modular home builder, reviewed and informed our construction processes.
-Callahan Ward, a developer in Philadelphia, gave criticism about site, material, and cost based decisions
-We were in contact with Darnetta Arce, the Executive Director of Brewerytown-Sharswood Neighborhood Action Committee, who gave feedback to us based on community decisions and ideas
-We were also in contact with Herman Arce, Jan Pasek, and Nichole Tillman from PHA who informed us on low-income developments in the area that were of interest, as well as standards that informed our affordable design.
-Lastly, Petit group gave criticism and feedback for our work throughout the entire process.
-Callahan Ward, a developer in Philadelphia, gave criticism about site, material, and cost based decisions
-We were in contact with Darnetta Arce, the Executive Director of Brewerytown-Sharswood Neighborhood Action Committee, who gave feedback to us based on community decisions and ideas
-We were also in contact with Herman Arce, Jan Pasek, and Nichole Tillman from PHA who informed us on low-income developments in the area that were of interest, as well as standards that informed our affordable design.
-Lastly, Petit group gave criticism and feedback for our work throughout the entire process.

Since the 1960’s Philadelphia has been undergoing a state of revitalization, which brings gentrification. Gentrification is defined as the process of renovating and improving a house or district so that it conforms to middle-class taste. Historic neighborhoods have seen newer developments take over the established community. While this benefits middle class families, it most notably displaces existing low income families. As we searched for a site for this project, we were drawn to Brewerytown, Philadelphia due to the opportunity for renewal. The area has many vacant lots, and its residents are above the 50% poverty mark. As a result, we decided it would be a perfect place to design a new low-income model that would benefit the community. As we researched the implications, the project grew to be much larger than just solely about an affordable unit.

We began a critique on the many recent developments in the area, constructed by the Philadelphia Housing Authority, from here on referred to as PHA. PHA is a municipal authority providing Public housing services in Philadelphia, PA. As we walked around the neighborhood, we quickly noticed that we were able to point out which areas were public housing. The small communities were visibly isolated from the rest of the neighborhood. To continue, through more research, we discovered that these families living in these communities were relocated there, basically being told that they had to be removed from people’s view. PHA is unintentionally stating that low-income families do not deserve and can not afford the same quality of living that the standard citizen would have.

From here, we looked back at PHA’s past projects. At the beginning, PHA and other housing agencies were most involved in high-density building typologies. We found out that these developments were poorly executed and were made up of mostly high-rise apartment buildings, such as the Blumberg Apartments in Sharswood, Philadelphia, which neighbors our site. Families had very small living spaces, no privacy, and no comfortable community space. High-density living has also been known to affect people's physical and mental health, while increasing crime and social isolation. Most now realize the ineffectiveness of these projects, and have begun tearing them down.

Recent efforts to develop more appealing low-income housing are these pockets of “suburbia” in the city. These complexes seem out of place in an urban environment. They are meant to emulate the quality of living that families have away from the city; more space, privacy, big lawn, etc. However, these homes actually house two to four families, becoming duplexes and triplexes. In this way they are reducing unit density in the community, but increasing density within the individual units. These homes are clearly seen as typical
“low-income” housing by not connecting the homeowner to the neighborhood and being poorly constructed of cheaper materials.
“low-income” housing by not connecting the homeowner to the neighborhood and being poorly constructed of cheaper materials.

Other projects include everything from smaller apartment buildings to attached housing and row home styles. Again, these typologies don’t offer enough privacy and space for the residents. They don’t create an equal quality of living. They also are solely made up of affordable housing, so there is no diversity that can be brought in when incorporating market rate housing alongside them.

However PHA states, “Despite concerns over gentrification, the city can't afford to slow development [due to a rising population]. So, it must find ways to encourage growth while protecting long-term homeowners and creating neighborhoods that are economically and racially diverse.” This has yet to become a reality. The PHA is attempting to create a more appealing community by isolating it from the existing neighborhood.
This project will combat these design flaws by exceeding the PHA requirements and creating a better quality of living for low-income families.
This project will combat these design flaws by exceeding the PHA requirements and creating a better quality of living for low-income families.

The site that NewMod will occupy is located on the 1400 block N. Marston Street in Brewerytown, Philadelphia. Located close to major artery roads of the city, there is ready access to public transportation. North Marston Street is a one-way street that is very narrow and has no street parking. It is mostly abandoned, with a few condemned structures. The lots in this neighborhood are unusual, they are very narrow and deep. The new zoning code is not ideal for Brewerytown lots. It requires setbacks that force either the building footprint to be smaller, or a full infill of the site. This provides an opportunity for exploration of new housing solutions for Philadelphia.

We began looking at multi-family and attached housing methods, but eventually landed on the single family urban detached house. This typology has yet to be investigated in the city. We discovered that it provides more equality between the units, and privacy for the residents. To maintain diversity and density of units on the site, market rate housing sits alongside affordable homes. The new zoning code requires that there is a minimum rear yard, side yards and setback from the street. Due to these conditions, the building footprint is 16ft. by 40ft. This project fits 30 detached units along North Marston Street.

Our goal is to create an integrated community, where a person standing on our street will not be able to tell the difference between a low-income home and a market rate home. We are designing low-income housing that is as desirable as market rate housing, while reducing gentrification, and creating a better quality of living through more cost-effective means. Through the design process, the low-income model and market rate model are analyzed alongside each other, although the focus still remains on the low-income unit.
The street is developed with new lots to draw residents to an area of the city that is ready and able to grow. The street width is maintained however it is redeveloped so that a new system of stormwater management creates areas for short term parking alternating along the road. The frequency of the basins allow stormwater filter into the ground on site and create a more consistent soil and ground health along the block. Both housing models are pushed away from the street front by the plant life found within the basins, front yards and side yards. Having residents and visitors to the site be unable to distinguish the difference between the two housing types is achieved through an even curb appeal.

While the Market rate houses will have a third story, as opposed to two stories, the low-income models will have a Photovoltaic trellis that raises the height of the building exterior to create an even height along the street. Along with visual attraction, the models take advantage of Energy efficient systems that lower the cost to live in the house. By investing money for the added time and consideration in the development of the building, the home-owner is able to see significantly lower electric bills. The whole project is powered by electric energy which is fully supported by the Photovoltaic system on the roofs. A low cost solar array is made possible by creating a building envelope that keeps energy within the house. By having each unit built of modules constructed in a closed environment, this ensures quality of construction and tightness of the assembly. Building modular also saves on cost by reducing time of construction and labor.

The Module is dictated by an even division of the lot available. Each unit receives the same base kit of modules which are based on spaces in the home. These modules can be placed in a variety of sequences, enabling the street to be comprised of several different configurations for both building types. In this way the block becomes a community, and through careful consideration, NewMod fits into the neighborhood unlike some PHA developments.

By creating a unit that is exposed on 4 sides, daylighting is increased, cross ventilation is available, and site strategies are reinforced. The interior of the building directly benefits from this new model. It is now able to have windows on all facades to allow for natural light into the spaces rather than relying solely on artficial light sources, which means less energy consumed through the day.

Each window has a multi-purposed extruded aluminum detail. It is angled so that on the top edge it acts as a solar shade, and on the other 3 edges it becomes a light shelf, helping to reflect light into the interior.The interior of NewMod is designed to provide a high quality of life in both market rate and low-income units.

The building is constructed using low cost but high quality materials. Once again, raising the standard of living. Each wall in the assembly is rated by UL to verify fire safety and security within the home. Using hardwood floors as opposed to laminates in combination with well arranged floor spaces gives an immediate sense of quality. The kitchen is designed to have expanded cabinet and pantry space that meet contemporary market rate standards.

Proper amounts of lighting are installed throughout the house. Flush mounted fixtures in the ceiling provide the necessary light without detracting head space from the modules. All lighting throughout the house uses fixtures that accept low wattage LED bulbs to provide illumination.

The circulation module becomes home to the mechanical and plumbing core of the house. It is a vertical stack of closets. The kitchen and bathrooms are arranged to be in close proximity to this core. All of the appliances and fixtures meet, or exceed, Energy star and Watersense standards. While choosing appliances, we weighed financial concerns equally with energy saving requirements.

New Mod is built from offsite constructed modules. These modules are based on spaces in the home. These modules are assembled onsite with connections fitting together to complete full wall assemblies.

Some modules will require some additional lateral bracing to eliminate wracking and movement thorough transportation and installation. These wood members will be removed when installed and are onsite for additional blocking as needed. The modules are narrow enough to arrive via flatbed on a 8 foot wide truck and be craned into position. To simplify connections between mechanical systems, the circulation module becomes the host to the mechanical core of the house. This means that alterations, whether holes for plumbing lines or cuts for duct work, can be factored into the joists before the modules are shipped to site. The same measures will be taken for electrical fixtures and appliances. The final system connections will be handled on site as needed.

The interior walls are made of 2x4 inch studs and the exterior walls are constructed of 2x6 inch studs, both 24 inches on center. By having less framing, that means there are fewer possibilities for thermal bridging, increased volume for insulation, and reduction in construction time. Exterior single stud framing resolves such issues therefore reducing the cost needed to construct complicated framing details. There are typical framing conditions related to jack studs and structural plates that can be eliminated due to redundancy of modular connections.

Fiber batt insulation will be put into the 2x6 stud framing. A layer of rigid insulation and R Zip Sheathing will be added on, along with an exterior fiber cement rainscreen cladding system. The total R-value of the wall is 46.75, 24.15 is accounted for within the interior cavity and the other half, 22.6, is found by totaling the exterior layers. The Exterior cladding is connected via vertical fur strapping so that water may drain properly from the air cavity. R-ZIP sheathing has a weather barrier built into the exterior and an additional water barrier is added to it. A self-adhered air barrier is applied between the rigid insulation and plywood sheathing. The air barrier’s performance is increased when partnered with plywood sheathing. It is able to control air and humidity that has reached that point in the wall, by holding any remaining moisture, while air is working to dry the sheathing. On the other side of the wood studs with batt insulation is a variable permeability vapor retarder which regulates vapor and humidity from the interior. All connections of the assembly will be taped over to act as control layer for vapor and thermal bridging in points where the insulation was breached. This ensures that water, vapor, and air barriers protect the wall’s insulation. Batt insulation will also be added to the first framing cavity of connecting modules and along all rim joists for extended thermal bridging protection.
Rigid Insulation will be added on the interior and exterior of the foundation. The footers extend to or exceed 3 feet into the ground to meet the 36-inch frost line in Philadelphia. The 4inch foundation slab sits on top of a layer of rigid insulation. The foundation wall rises 12 inches above grade so that groundwater does not have a direct path into the assembly. Metal flashing is located between the above grade wall insulation and foundation insulation to provide closure and protection against exterior conditions.

The roof of NewMod aids stormwater strategies implemented on the ground. A vented blue roof slowly drains the water from the roof and keeps moisture out. The roof now acts as a control for stormwater management by keeping water on the roof and slowly releasing it to prevent ground level flooding. Due to the roof holding water longer than conventional construction, there is a second water barrier before the insulation. The vented blue roof draws any vapor out of the assembly through an air cavity beneath the insulation.

The indoor Air Quality is simple to maintain with less energy by designing a tight envelope. NewMod is easily controlled by a mini-split and ERV system.The ERV was selected for Philadelphia’s humid summers and dry winters. The ERV not only recovers heating and cooling loads but it works to regulate the humidity in the air. As conditioned air is carried through the house, its temperature and moisture properties are changed to meet comfort levels. The ERV is located within the conditioned spaces of the building so that it can both supply and exhaust the entire house from a central location. A minuscule negative draw is enough to circulate air throughout the house. By creating such a tight envelope, it needs to be known that any exhaust fans besides the ERV will create an immense negative pressure. The kitchen will be unable to have an exhaust hood and the oven and range need to be fully electric. The bathrooms are also unable to have their own exhaust fans, however the ERV returns are in close proximity to the kitchen and bathrooms.
Through designing a low income and market rate model, mechanical systems see minor differences. The low-income unit handles all of its supply air through Alpine ductless mini-splits. The a mini-split 4-zone supply system that uses an ERV, and wall mounted indoor heat pumps to distribute air and ventilate all spaces within the home. The Market rate uses a ducted system with an air handling unit in the basement, again using balanced ventilation through an ERV. Air is collected from a small ductwork system at each exhaust location, and the unit delivers fresh air to the AC return air duct. The vertical ductwork will run through the circulation module and feed into spaces to circulate supply air.

The hot water is distributed through PEX tubing. PEX is flexible, cost effective, and much lighter than copper pipes. A thermostatic system mixes an insulated volume of 180° water with incoming cold water to demand so that no residents are scalded by the super hot water within the tank. Bathroom and Kitchen modules are located as close to the mechanical core as possible to simplify onsite connections and ensure water is delivered quickly and at proper temperature.

NewMod makes use of the solar array harvesting energy on the roof. The system selected will be made of flat, glazed panels angled at 20°. The array is sized to cover the electrical loads of the Energy Star Appliances and mechanical systems while still maintaining a minimal impact on the final cost of the project. The array will heat the hot water tank to keep the energy within the home. Innovative integration of a photovoltaic array with systems eliminates the project’s need for demand energy sources. All of this is achieved within the teams price point.

NewMod’s primary goal is to show that not only can new living standards be made, but they can be achieved while adhering to buildings standards of the future. NewMod is able to reach a score of -1 on the HERS index, setting it apart from typical housing. NewMod is understood to be a cohesive assembly of integrated systems that complete a building. The exterior envelope, mechanical systems and interiors work together in producing a holistic Net Zero Energy Home. A score of -1 is achieved by tightly sealing the building, ensuring all joints and connections are sufficiently sealed and insulated, and having all systems work with the enclosure and environment instead of combating their effects.

NewMod also performs well on the LEED scale, an analysis of new construction yields a Platinum rating. This does not account for post-occupancy or pre-construction considerations. All fixtures, systems and appliances in the house are environmentally responsible. All are selected to meet energy standards set by Energy Star, Water Sense, Underwriter Laboratories, and Net Zero. This is another reason that NewMod is set apart and exceeds PHA developments.

In order to construct a project that can better low-income standards, the Philadelphia Housing Authority is challenged directly. Breaking down each material, fixture, and assembly on the interior and exterior, NewMod is able to build a house for $120 per square foot.

In Market rate, we see some differences in construction and excavation costs, as well as interior finishes. Adding an unfinished basement and third story increases construction expenses. This increases the amount of materials needed, yet still is able to be built for $140 per square foot.

The PHA builds homes for $154 per square foot. PHA is required to use union labor, across all fields, which would double the cost to build NewMod. Even with the addition of a photovoltaic array, the cost of the low income model is lower than the PHA standard of the surrounding neighborhoods. This breakdown of costs has proven that high quality systems, finishes, and appliances to meet net zero are now feasible in a low income project.

So what we have achieved is providing a model to PHA that meets zero energy requirements in a sustainable way that costs less and is better built than what is currently available.
Therefore, we are challenging the idea that low-income has to be separate from market rate housing. Effectively combating gentrification by reducing the displacement of low-income families to less desirable areas.
We have accomplished this by developing the single family urban detached house. It provides open green space, flexible interiors, and uses energy efficient systems. NewMod has proven that these methods are feasible for low income housing.
We have achieved an integrated and a diverse community that takes up an entire block, where equality is created between the affordable and market rate unit. Now the low-income home is just as appealing as the market rate home.
NewMod is able to create a new standard of high quality urban living that comes at a low-income price point using Zero Energy methods.

Closing statement: Now we ask you, would you live on this street? If your answer is yes, then we have accomplished our goal. Thank you!