
This project required me research and design an innovative clamping system dedicated to tasks within a workshop environment, developed to suit an appropriate brand chosen from a selection of clamp brands through a user inclusive design process. The process is detailed below.

The chosen brand BESSEY, is a recognizable brand that has grown to be one of the largest hand tool clamp manufacturers in the world, distributing some 1300 different wood working and metal working clamp tools in more than 100 countries worldwide. Desktop research was conducted in order to understand the brand ethos, product range, existing technologies and innovations, manufacturing processes and how the brand is applied to BESSEY products. This was followed by an analysis of the brand as well as other competing brand's clamping technologies in order to understand existing approaches to usability and ergonomic consideration.

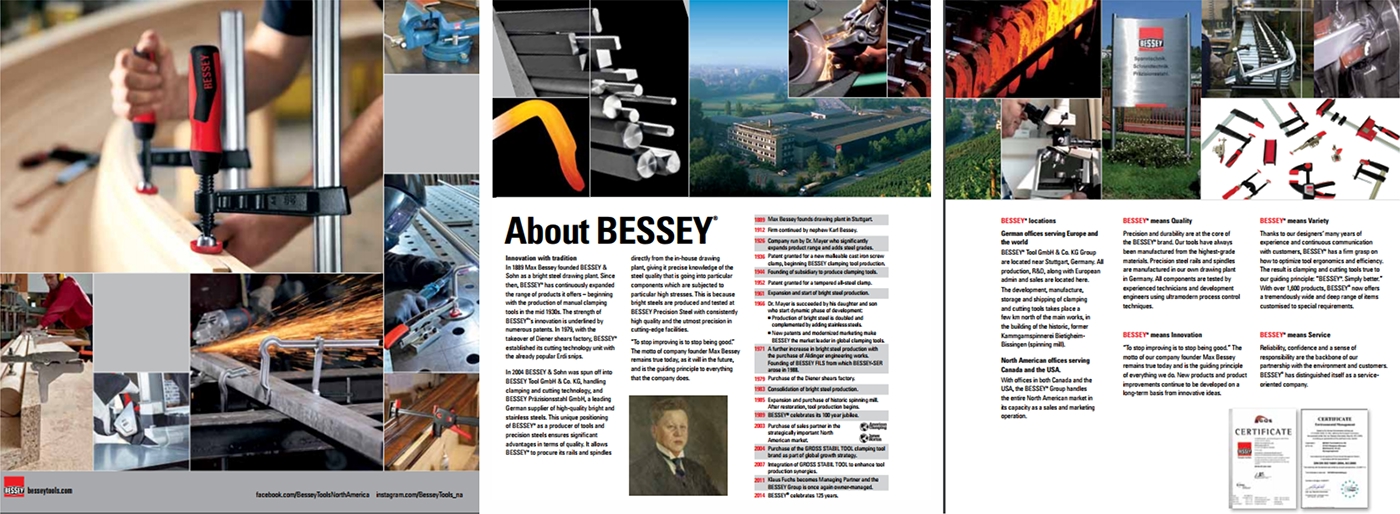


Precedent board| Bessey woodworking clamping system range

Precedent board| Clamping systems by competing brands

Engineering sketch| Exploring existing clamping system
In order for the design outcome to reflect empathy with the human interface of the product and a correct level of visual , 3 users were identified and included in the design process in order to obtain user ergonomic data, opinions on personal preference, and product requirements .
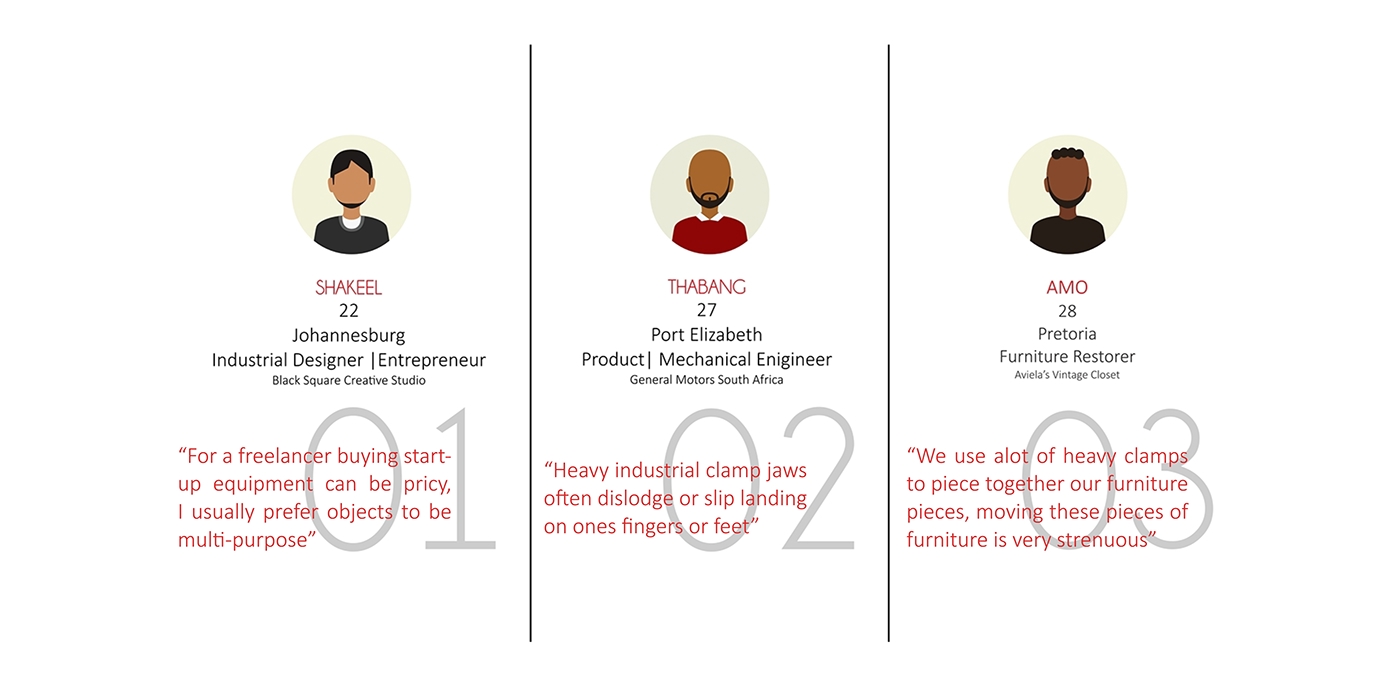
User profiles
After the first stage of user feedback , a male and female persona was identified for whom the clamp would be designed for. This persona includes the broader category of both male and female customers who are likely to buy the product and reduced to a single persona of each gender representative of this group. The market represented by the personas are home owners and makers with home based or small studio workshops.

Persona boards| Male and female representative of target market.

As a starting point a vast collection of doodles, very free sketches and models were produced for the purpose of brainstorming and exploring various potential concept directions . Safety was one of the major concerns highlighted by users, stating that on many occasions heavy clamps have fallen on their feet, others pointing out that it is virtually impossible to lift and move clamped objects without the help of someone else or other technologies and this often results in back strain .My focus was specifically on conceptualizing a clamp which addresses these health and safety concerns of workshop environments . A moving clamp that would allow individuals working alone in a small scale studio workshop without sophisticated industrial lifting and moving technologies or even a helping hand to move objects with ease. This was followed by presenting three of the concepts with the most potential to the users in order to obtain feedback based on the level of innovation and practicality of the design. Based on the feedback from the users and peers ,the most preferred concept was taken forward to the development of the design process.
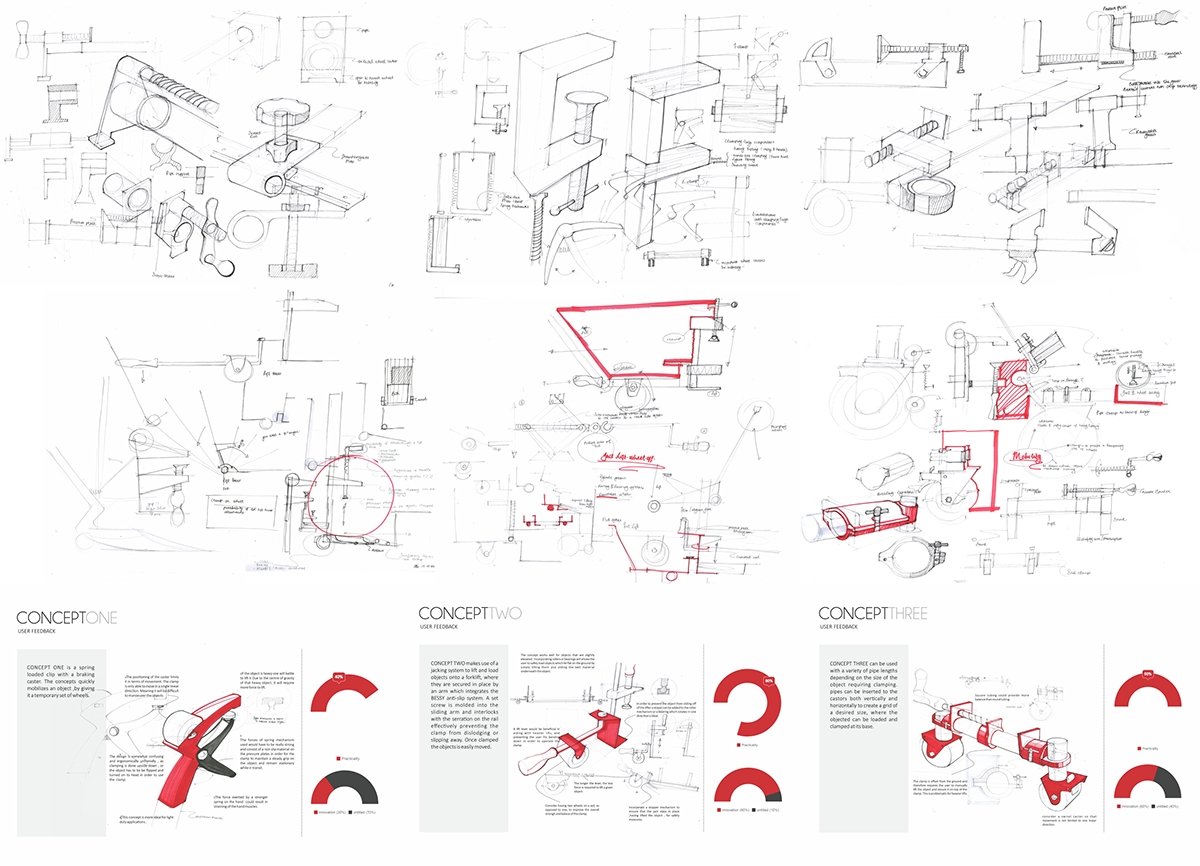
Ideation sketches
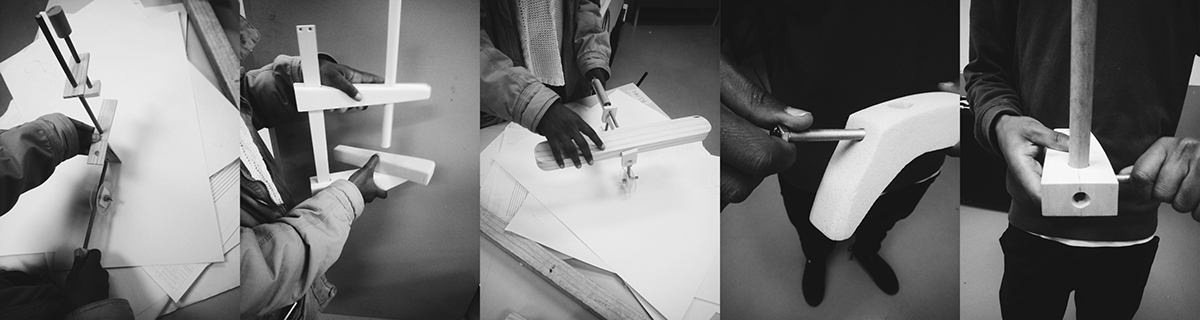
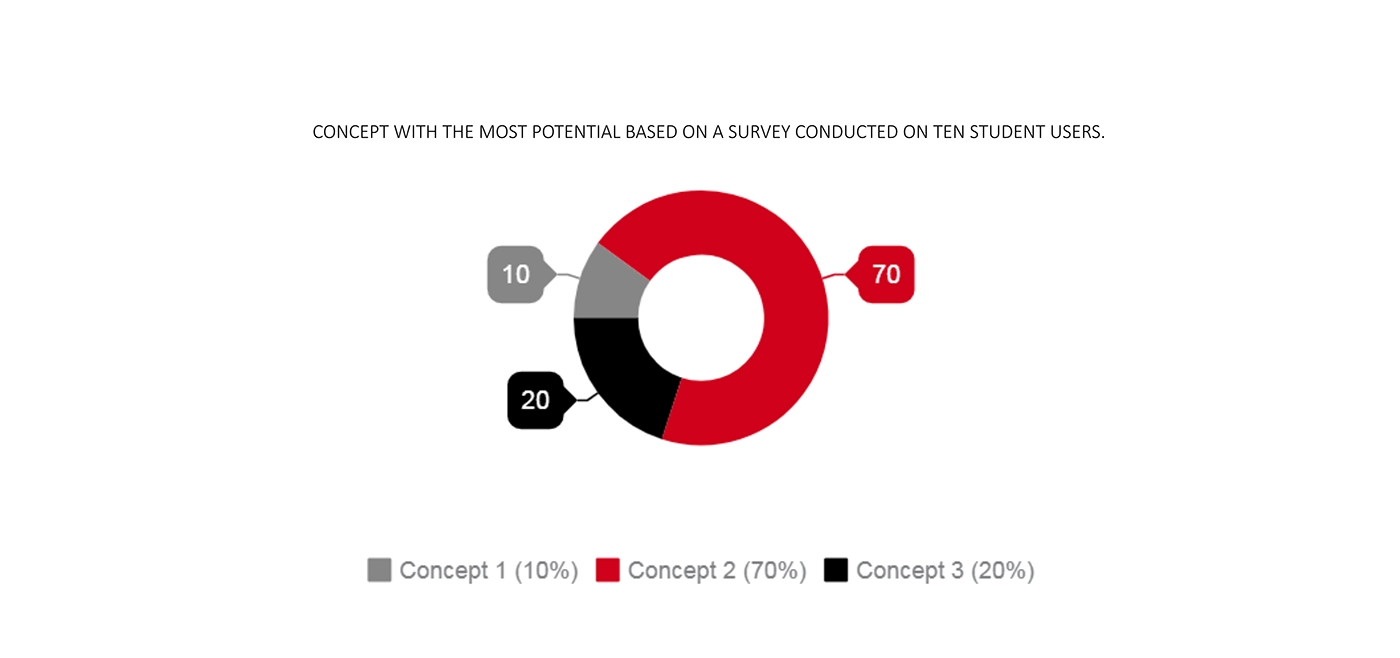
Concept direction feedback data capturing

Having Identified a need and come up with a concept that would address it , the next stage was to realistically think of the usability, function and technical aspects which would render my concept a viable product for market. The work-ability of the concept was explored through sketches and developmental models which where presented to users to test and give feedback and input on the various aspects of the design.


Once every aspect of the design was technically resolved ergonomics and interaction with the product was explored. A 1:1 Scale working model of the design together with polyurethane foam handle models were fabricated for user testing. Users got the opportunity to get a feel of how the clamp would work and its various potential configurations , and give feedback based on what they found most comfortable and effortless to use.

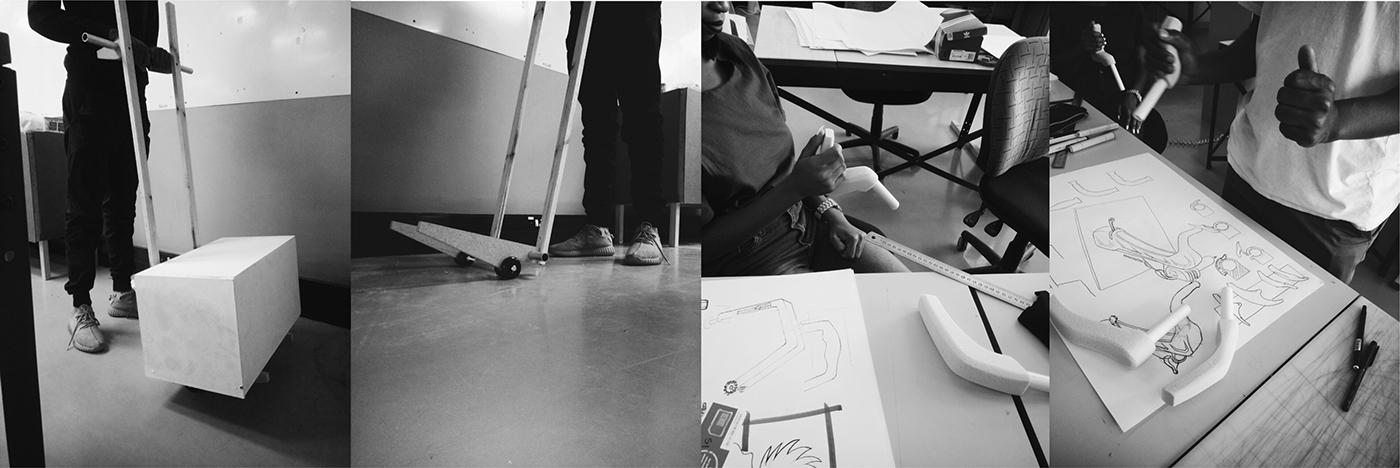
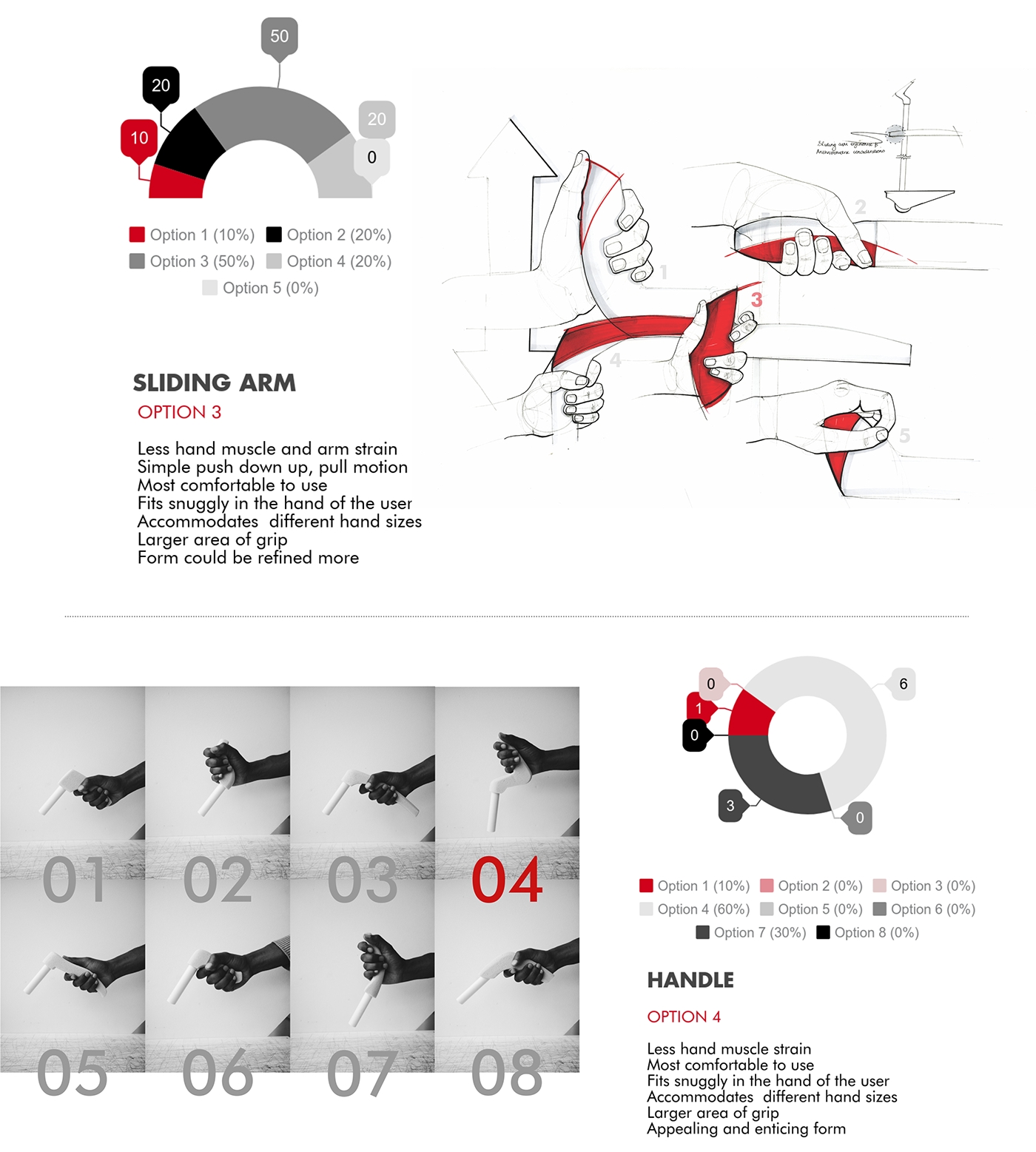



Screenshots of CAD assembly of clamp
The final design is inspired by Bessey's original malleable cast iron screw clamp which dates back to 1936. The F-clamp system is used to secure objects onto the moving clamp, the design consists of two horizontal arms joined together by a vertical bar. Maximum safety is guaranteed with an anti-slip system, the sliding arm is effectively prevented from slipping away by a clamping tee-knob which screws into the sliding arm applying pressure to the pole and securing the arm in place. The sliding arm features a large ACME thread ball screw which allows for the clamp to be tightened. The ball screw consists of a pivoting pad which accommodates angled surfaces and a plastic cap which ensures that the clamping pressure doesn’t blemish object surfaces. A fixed steel Jaw houses a brake castor which offers a temporary set of wheels to heavy or clamped objects, with the addition of a second clamp, the F clamp transitions into a portable clamp-on trolley. A 300mm throat depth means that large objects are effectively secured. While the screw secures objects in place, a strap is secured around objects with a ratchet buckle ensuring objects remain fixed in place during motion. An ergonomic handle ensures comfort and effortless pushing and pulling of the moving clamp.
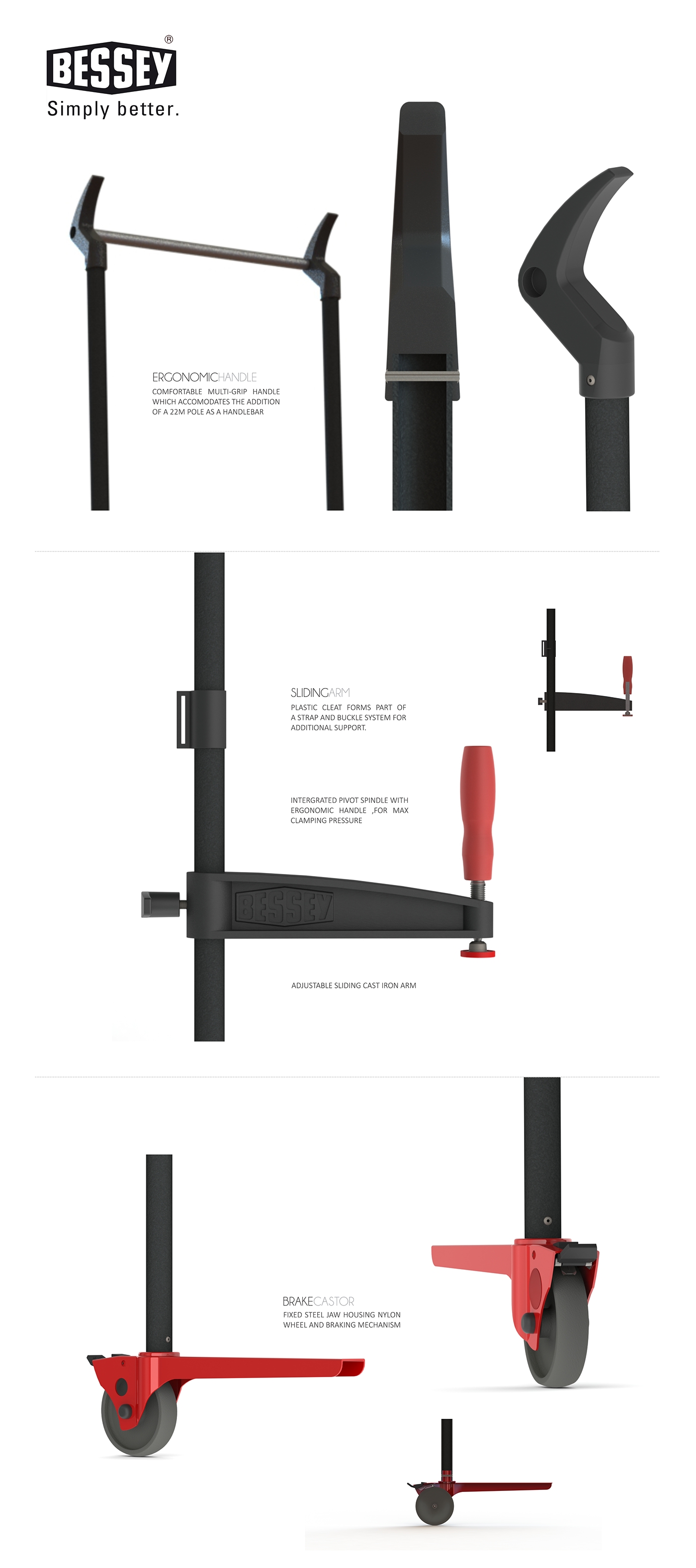
CAD renders highlighting clamp features

In-situ CAD render of the clamp in use as a moving trolley

In-situ CAD render of clamp in use as a F-clamp
