









If you read further we show you the process behind the making of the Braille printer. The printer in this Case is called Braille Box.
Index Braille have their facilities in Gammelstad, a suburb to Luleå in the north of Sweden. They have produced braille printers for three decades. They have the biggest market share in the world. The introduction of Braille Box will surely not change that.
Index Braille have their facilities in Gammelstad, a suburb to Luleå in the north of Sweden. They have produced braille printers for three decades. They have the biggest market share in the world. The introduction of Braille Box will surely not change that.






Their office is really nice, especially the fishes :) If you take a close look behind the aquarium in the film below you can see our great office that Index Braille provided for us throughout this project.

We made a plan on how to attack the problem given to us. We started off with a phase called Analyze. We gathered information about "user needs" and "the technology inside the product" through research, interviews and observations.










We collected a lot of inspiration from all kinds of areas and through different activities and made moodboards out of the result. We wrote down all the words we could come up with regarding Braille Box based on the result from the analyze phase.




We used the words and the moodboards as inspiration when we went in to the Concept phase to sketch and build mock-ups.
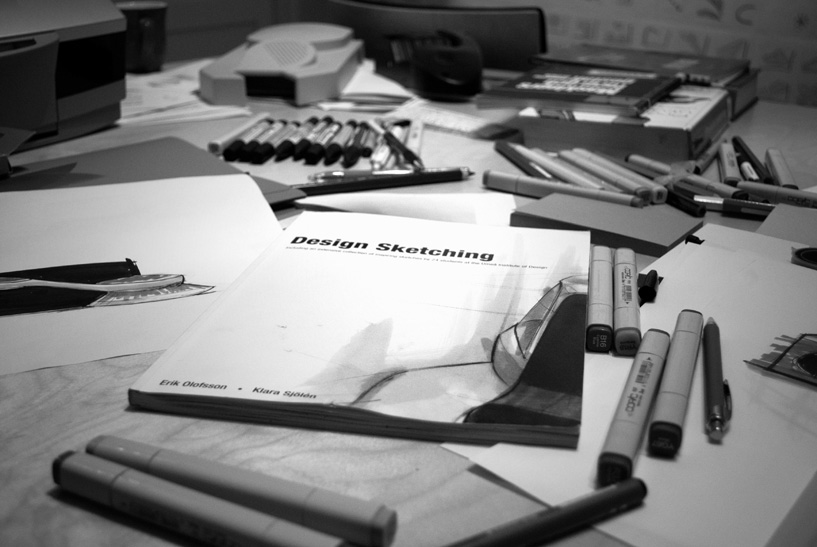




We made a lot of sketches. To get an overview of the material we decorated the walls in our office with all the material we produced. In order to get a better understanding on how some of our favorite shapes behave in three dimensions we made a lot of models in clay and foam. We made the models in the scale 1:4.







We compared different shapes, picked the best ones out and went back to the drawing board and made more detailed sketches.





We used a few methods to compare the different concepts. Finally we choose one concept of which you can see some sketches above. We decided to work with the asymmetrical shape to give the user a tactile instruction on which areas to use. We made more foam models in scale 1:4. Finally we made a full scale model in white and grey cardboard to evaluate how the shape behaves in its actual size.





We developed a recess at the backside that provides space for all wiring so that the printer may be placed in a corner without pinching any cables. The moment captured above was the first time we discussed the recess.



We played at least two pool games per day in order to free our minds and get more creative. After we had decided which concept to develop further we started working on details.

We started the Realization phase by making the shape in a CAD-environment to get a hint on how well the outer case integrates with the mechanics.

Index Braille was very convinced that aluminium was to be the main material of choice. We really wanted to add glass to get a tactile contrast between the different materials. In order to decide exactly what materials to use we called a lot of distributors to get samples with different properties.

When we got our different material samples we did some hardcore testing. We bent, hit and scratched the samples to see what happened. We also built models to test the functionality of some design feats. Among other things we bent a 10 mm thick PMMA-plate (Acrylic) 90 degrees with a relatively small radius. This test was done to see if a L-shaped service door was possible to produce by just bending it, and to see how well the radius enfolded the mechanics.





The service door needs hinges in order to be opened easily. We therefore made a model to test the functionality on a pair of hinges we latched on to.



The noise that is generated by the braille mechanics is really, really loud. Due to that Braille Box has to be a completely sealed unit. To test how much we could block the noise out we built a soundbox. We made the box of MDF with a thickness of 10 mm which makes it comparable to a 2 mm aluminium plate which will be used in the final solution. The only uninsulated areas on Braille Box are the two vents that will be placed in the back of the printer. To get a realistic result from the simulation we drilled holes and designed and assembled some homemade exhaust silencers. We covered the inside walls with a sound absorbent material.









We made the sound tests in accordance with ISO 3744.

Above you see a rendering of Braille Box in an early stage. Below you see some renderings that shows Braille Box in a later stage in the development process. These renderings give you a good hint on the final result.










It has to be a physical interface on Braille Box. The interface is made of a tape with imprint buttons. We made a frame to the interface that gives it a style that better suits the holistic design. The interface has braille text and sound feedback to make it easy for the visually impaired user to interact with the product.

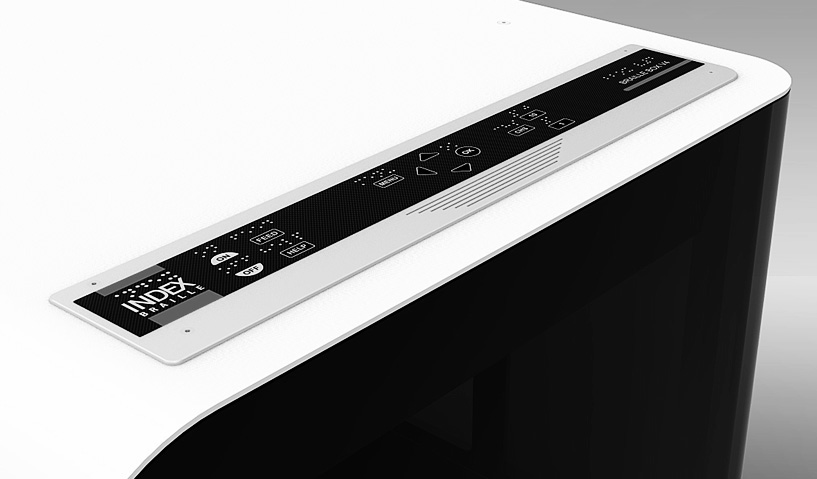
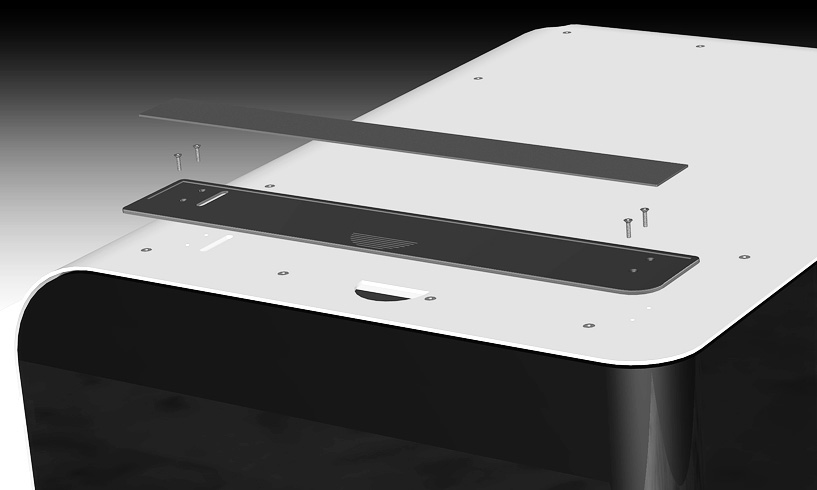

We made ergonomic tests with the help of Jack, a simulation feature in our CAD-software that makes it possible to measure different kind of anatomic tensions when using the product.

Some visually impaired people can perceive light- and color contrasts. To give those users an extra verification on which state the printer is in we added some LED-lights that blinks when an error occurs. We made some tests on different kind of LED’s.

We worked a lot with the choice of colors. To give the visually impaired the best possibility to understand the product it was of great importance that we used contrasting colors. The greatest contrast is between black and white. To fulfill the user needs we choose to work with black and white. Areas where the user can interact with the product are black (or dark grey) and areas that are not for interaction are white.

A lot of discussions with manufactures and a lot of detail adjustments where done before we finally could send the first prototype of Braille Box into production. I can’t describe the joy we felt when the first parts arrived. Almost everyone in the development team was involved in the assemblage of the first Braille Box.









This is the first prototype of Braille Box, manufactured in the spring of 2010. Since then Index Braille has produced four more prototypes. They did a lot of testing and made many technical improvements before it finally reached the market in the beginning of 2011. In the spring of 2011 Braille Box was awarded a Red Dot seal for high design quality and is now on display in the Red Dot Design Museum in both Essen (Germany) and in Singapore. To read more about Braille Box and the Red Dot Design Award, follow this link. Thanks for reading our story about the creation of Braille Box.