Driven by Process - Rotational Planters
This project aims to explore the beauty of designing for a specific manufacture process and how the constraints of engineering, mould tool making and ultimately process selection can influence design decisions. The visuals that follow showcase designs for rotational moulded planters. The planters have been designed around the constraints of real world manufacture, and tooling data has been developed for one chosen concept. The tooling data at this stage is ready to be reviewed by a tool maker, where the product could then go on to be manufactured.
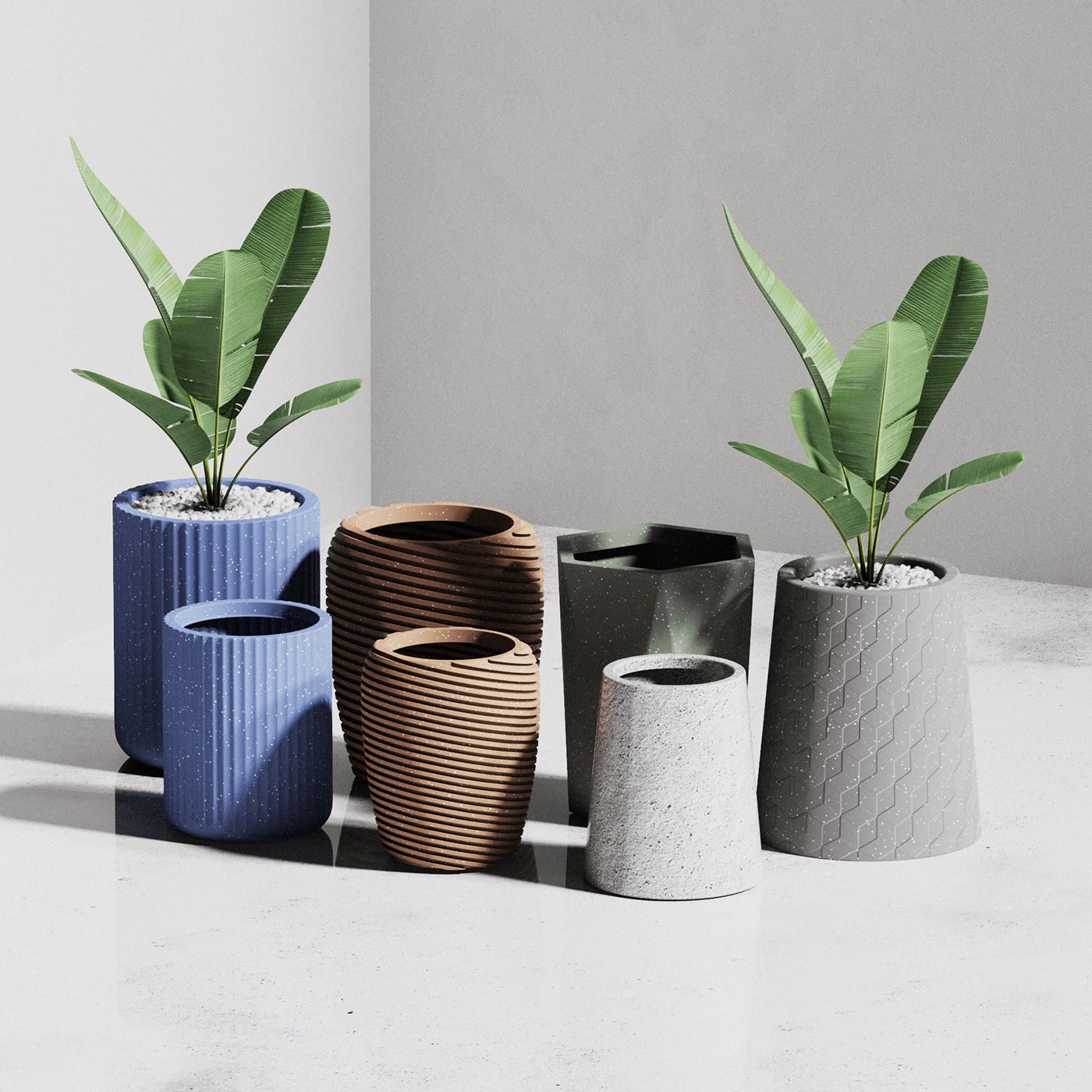






CMF.
The colour, material and finish has also been driven entirely by the process. Often with rota moulding, a speckled finish can be achieved and applied to the object to create a concrete like effect in the powdered polymer. The finish often has a roughness and bump texture that is inherent to the selected process as the powder coats the internal faces of the tool.



The Mould Tool.
As well as designing the planter, the mould tool data has also been developed specifically for a rotational moulding machine. The visuals below show the data that has been developed for initial review. The tool has been split into a three part aluminium around the centre ridge of the planter. A top piece enables the return lip to be moulded around the lip of the planter, while an insert in the bottom creates a drainage hole. A 45mm flange around the splitting edges allow the tool parts to be located together with pins and clamped in a jig ready for rotation.


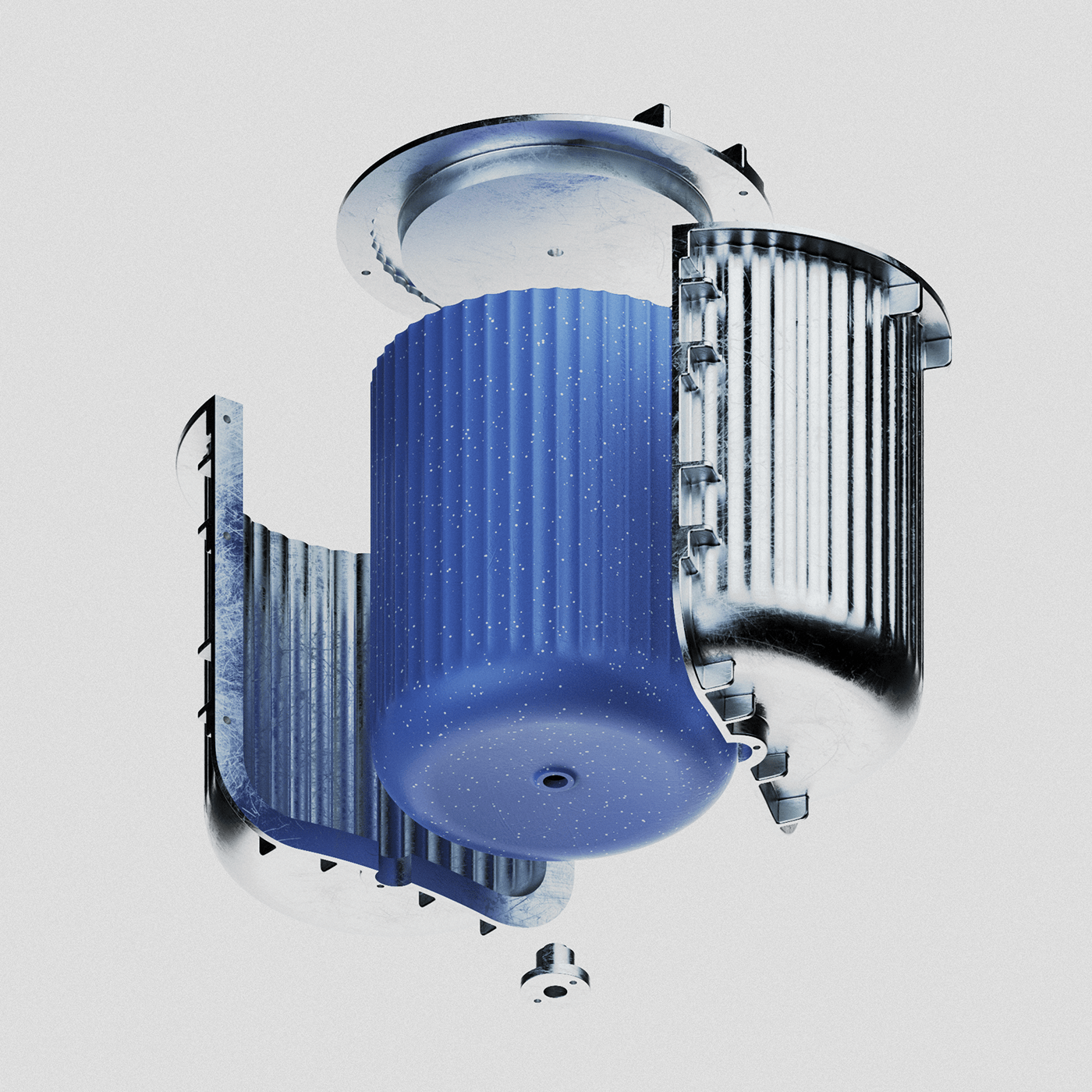
Once the tooling parts have been machined and ready for moulding, polymer power is entered into the empty cavity. The tool is clamped and then rotated in a rota moulding machine. The polymer powder heats and bonds to the internal faces of the tool. Once it completes it cycle, the tool is opened, and the moulding shrinks by roughly 3% from the tool. The moulder is then left with a hollow body that is trimmed around the top edge. The 'flutes' in the moulding design help to prevent warping and provide a rigid structure for the planter and polymer when setting.







The Result.
The moulding is now ready to be palleted and transported to storage to be sold to the customer. The design of the planter has been developed to fit in with a contemporary environment. Any pattern could be designed into this data as long as it fits and works with the constraints of the tool. Designing with manufacture in mind helps to produce better designs that will work and prevent less issues during the manufacture stage.


Thanks for taking the time to view my work.